Tuesday, November 12, 2013
The Effects of Surface Finish on the Resistance of Metals
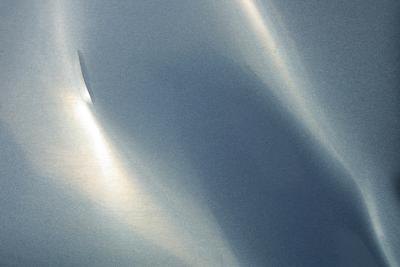
Surface finishes or coatings for metal offers corrosion resistance, improves the appearance of a particular metal, protects against tarnishing, reduces the amount of wear and increases a metals resistance properties. Most finishes are not designed to alter the resistance properties of the metals that they cover.
Black Oxide Coating
Black oxide coating is a conversion coating that is used as a finishing process for steel. This process uses an alkaline aqueous salt solution, operated at 285 degrees Fahrenheit, to cover steel or iron parts. Once parts are dipped into the solution it forms an abrasion resistant surface that dulls the glare of light, improves surface lubrication and doesnt exhibit a white corrosion state which could cause an electrical short. Black oxide coating doesnt change the dimensional, mechanical, or physical properties of any part that is dipped within this solution. Black oxide coating isnt typically used for electrical applications but if it is employed for this purpose it doesnt lower the resistance properties of the metal that it covers.
Chemical Finish
Chemical finish black is designed to retard corrosion for copper and copper alloys and this process doesnt provide abrasion resistance. Chemical finish black is used to make a copper part appear black in color to reduce the gloss on the surface of copper and to prepare a copper surface for future coatings such as varnish or wax. This process doesnt change the dimension of a copper part and this process isnt used on food service and water supply items. Chemical finish black doesnt diminish the resistivity of copper.
Silver Coating
Silver coatings are used for electroplating applications within electrical and engineering fields and it is also implemented for decorative purposes within the jewelry industry. This type of coating process improves the tarnish and corrosive resistance of a metal. Silver coatings are favorable for soldering applications and its hardness varies from 90 to 135 on the Brinnell Scale which is used to determine the hardness of a particular substance. Silver coatings do not change the resistive properties of the metal that it covers; it enhances them instead.
Tin Plating
Tin is known as Titanium Nitride and it is one of the most commonly used coatings that is used for machinery and tools across various industries. Tin improves the surface qualities of tools because it forms a hard barrier that is resistant to friction, abrasions and corrosiveness. Tin is also a primary coating because of its other characteristics such as adhesion, ductility, chemical stability, lubrication and resistance to temperature. When tin is used in electrical processes it typically doesnt alter the resistive qualities of the metal that it coats.
No comments:
Post a Comment
Note: Only a member of this blog may post a comment.