Tuesday, November 18, 2014
How to Replace the Injectors on an E38
BMW based its 7 series of cars, made from 1994 to 2001, on its E38 platform. The 740I --- the most popular vehicle in the series --- featured an eight-cylinder, 4.4-liter engine. All of the engines in this series use fuel injection, which requires a fuel injector to deliver fuel to the engines at high pressure. The fuel injectors for the E38 incidents are part of the fuel rail assembly on top of the engine.
Instructions
- 1
Remove the upper intake manifold with a socket wrench and detach the electrical connectors for the fuel injectors. Disconnect the vacuum hose on the front of the fuel rail.
2Attach a pair of locking pliers to the adjustment screws on the hose clamps for the fuel return line on the fuel rail. Turn the screws counterclockwise to loosen the clamps and disconnect the fuel return line from the fuel rail. Remove the flare nut on the fuel line with a 12-millimeter socket and disconnect the fuel line from the fuel rail.
3Spray compressed air around the base of the fuel injectors to keep debris out of the injector ports. Remove the mounting bolts for the fuel rail with a 10-millimeter socket.
4Pad the corner of the valve cover with a clean shop towel and pry the fuel rail with a small pry tool to lift the injectors out of the manifold. Push the fuel lines to the side and remove the fuel rail assembly from the engine.
5Pull the fuel injectors from the fuel rail assembly and connect the new fuel injectors. Install the fuel rail assembly to the engine and fasten the mounting bolts for the fuel rail.
6Connect the fuel line to the fuel rail with the flare nut. Connect the fuel return line to the fuel rail by attaching the hose clamps and fasten the retaining screws on the clamps.
7Connect the vacuum hose to the front of the fuel rail and attach the electrical connectors to the fuel injectors. Replace the upper intake manifold with a socket wrench.
Monday, November 17, 2014
How to Replace a Ford Exhaust Manifold
The exhaust manifold collects the exhaust from all of the cylinders and channels it away from the engine through the exhaust pipe. An exhaust manifold that is cracked will no longer work efficiently and you will need to replace it. Leaking exhaust exposes anyone riding in the car to carbon monoxide fumes as well. It does not take very long to replace the exhaust manifold on a Ford. You can do the job yourself in your driveway with some basic tools.
Instructions
- 1
Cool the engine completely before you begin this project or severe burns could result. Disconnect the negative battery cable. Unplug the wiring harness from the electric fan. Remove the fan shroud from the radiator using a wrench. Disconnect the electrical wire from the heated oxygen sensor.
2Remove the nut and bolt securing the catalytic converter to the exhaust manifold using a wrench. Remove the bracket bolt from the oil dipstick tube using a wrench. Remove the bolts from the exhaust manifold heat shield using a socket and ratchet. Remove the heat shield from the manifold.
3Remove the exhaust manifold by loosening the bolts with a socket and ratchet. Remove the manifold from the engine block. Remove and discard the exhaust manifold gasket. Place a new exhaust manifold and gasket on the engine block. Tighten the retaining bolts with the socket and ratchet. Install the oil dipstick bracket and tighten the nut with a wrench.
4Connect the catalytic converter to the exhaust manifold and tighten the bolt and nut using a wrench. Install the exhaust manifold heat shield using a socket and ratchet to tighten the bolts. Connect the electrical wire to the heated oxygen sensor. Install the electric fan to the radiator and tighten the bolts with a wrench.
5Plug the wiring harness into the fan. Connect the negative cable to the battery and tighten the terminal nut with a wrench.
How to Adjust a Mustang Emergency Brake

Adjust the emergency brake on your Mustang right from your home garage and save money. You can adjust it from inside the car so you dont have to get yourself dirty by working under the car. Is time to adjust the parking brake when you park downhill and the parking brake starts to slip. This means that the parking brake cable has slackened inside the cable rod and needs to be tightened with the adjuster nut. Tension put on the emergency brake over time causes the parking brake to slip.
Instructions
- 1
Locate the parking brake in the front center of the inside of the vehicle. Remove the console cover that houses it.
2Lift up the emergency brake lever four notches.
3Look for the parking brake cable rod. On this rod is an adjuster nut. Turn that nut with the pliers until it is loose but make sure it doesnt fall off all the way.
4Release the parking brake and tighten the nut.
5Raise and lower the emergency brake lever four times. This will set the adjustment of the parking brake.
6Park the Mustang on a downhill slant and engage the parking brake only. It should hold the vehicle in place. If it doesnt, repeat the adjustment.
How to Replace a Fuel Regulator

A cars fuel injection system supplies fuel to the engine. In order to get optimum performance from your vehicle, the fuel must flow at a steady pressure. Regulators control the fuel flow, making sure it is consistent. Like other mechanical parts, regulators can break down and require replacement. Symptoms of a faulty regulator include lower gas mileage, excess smoke from exhaust pipes and leaking oil from the engine. Replacing a fuel regulator can be a difficult task for inexperienced owners, but if you have basic car repair experience, you can save money and replace it yourself.
Instructions
- 1
Relieve the pressure in the fuel tank by opening the gas cap. Open the hood of the car and separate the cable from the negative battery terminal. Pull out the cushion on the rear seat. Remove the screws on the service hole cover and take off the cover.
2Disconnect the electrical wiring from the fuel pump assembly. Use the fuel line disconnect tool to unplug the fuel outlet pipe from the fuel pump bracket. Unscrew the retaining screws for the fuel pump bracket with the socket wrench. Pull off the return hoses from the bracket. Take the assembly out of the fuel tank.
3Use the socket wrench to remove the fuel suction support from the fuel pressure regulator. Separate the fuel filter from the regulator. Find and remove the O-ring from the regulator.
4Apply a thin coating of gasoline to the O-ring and insert it into the new fuel pressure regulator. Attach the regulator to the fuel filter. Connect the fuel suction support to the regulator using the wrench.
5Replace the fuel pump assembly in the fuel tank and reconnect the hoses to the fuel pump bracket. Attach the retaining screws to the fuel pump bracket and connect the fuel outlet pipe to the fuel pump bracket.
6Reattach the wiring for the fuel pump assembly. Reinstall the service hole cover with the socket wrench. Reinstall the rear seat cushion and reconnect the negative battery cable.
How to Compare Garages

Its a good idea to proceed with caution before agreeing to car repairs at a garage. Take a few days to compare garages to decide which car garage is the best for you.
Family and Friends
Many car owners have a trusted mechanic they turn to for repairs, but if the work needed on the car is outside the mechanics specialty, ask for a erral. Aside from your mechanic, ask family members or friends if they know of a good car garage. Chances are good someone you know has had to have their car repaired at a garage. They can offer some pointers on where to get the best deal.
Insurance Providers
Your insurance provider often has information on good car garages. Many car garages leave their business cards and information with car insurance companies because its the best way for them to get more business. Additionally, these garages must meet high standards and have certification before they are a business car insurance companies are willing to recommend.
Compare Estimates
Most car garages will provide you with a free estimate. Make sure you get a detailed list of estimates. Dont be surprised if the part you end up buying at the garage cost more than it would at an auto parts store.
Customer Service
Do the staff and mechanics act professional? Do they treat you with courtesy? Do they get work done on time? Do they work well together? How garage staff treat you now is not likely to change once you are their customer. Pay attention to how you feel being in this place of business and how others act toward you. If the mechanic is rude or the counter person would rather text instead of assisting you, take your business elsewhere.
Personnel and Credentials
Some car repair requires work done by a certified mechanic or a specialist. Some garages may have these mechanics, some may not. Make sure the garage is candid about what kind of repairs need to be done on your car and whether they have the right mechanics for the job. The better garage to go with is the one that has the kind of mechanic youll need for your car repair.
How to Replace an A C Service Port
Years ago in the days of R12 rigerant, when an air-conditioning service port went bad on your automobile, a Schrader valve could simply be serviced by itself. In todays 134A world, things have gotten a bit more complicated and costly. You cannot just replace the inside of a Schrader valve; now you have to replace the entire line where the port is located.
Instructions
- 1
Connect either the high side or low side hose on an A/C servicing station to the appropriate service port. Do not connect a line from the air-conditioning servicing station to the defective port. Evacuate the R134a rigerant into the rigerant tank on the air-conditioning station by turning on the evacuation pump and running it until all the rigerant has left the system.
2Disconnect both ends of the line with the defective service port and remove the line. Cover the connections on the A/C system with clean shop rags to prevent dirt and moisture from getting into the A/C system.
3Inspect the connections for discoloration. If the connections are clean and slightly oily there are probably no other problems that caused the service port to go bad. Blackened connections could be a sign of internal compressor problems. Investigate further and perform any necessary repairs.
4Connect the ends of the replacement line with the built-in service port just as the old line was connected. Ensure that any O-rings or seals at the ends of the lines are replaced and lubricated with mineral oil before the new line is installed.
5Connect the other hose from the A/C servicing station to the replacement port. Start the evacuation pump and run it for 15 to 20 minutes to ensure that all the moisture has boiled out of the A/C system. Note the vacuum readout on the A/C station. Allow the system to sit for 10 minutes. Recheck the A/C stations vacuum readout to ensure there is no loss in vacuum. A loss indicates a leak in the system, probably in one of the two replacement line connections. Repair as needed.
6Remove the service hose from the high side service port and start the vehicle. Turn the climate control switch to "Maximum." Set the machine to charge the system with R134a and the correct amount of compressor oil through the low side service valve. When enough rigerant is in the system, the air-conditioning compressor will start and draw the rest of the desired amount of rigerant and oil into the system. Remove the low side hose, completing the replacement of the service port.
How to Fix Eclipse Headlights

Properly working headlights on a car are vital for your safety and the safety of other drivers on the road. Fixing the headlights on your Mitsubishi Eclipse is an easily implemented task with the use of just a screwdriver and a few minutes of your time. The specific headlight required for your Eclipse will depend on the year it was made so consult a auto parts specialist if there is any questions on the unit required for your specific car.
Instructions
- 1
Purchase you replacement headlight. Check with the auto parts representative for the correct fixture for your year of Eclipse vehicle and the proper side that you are fixing. They should be able to give you the exact part for your needs.
2Turn your car off and remove the keys from the ignition. Pop the hood of your Mitsubishi and make sure that it is properly secured so it does not close while you are repairing the light.
3Look at the rear of the light fixture and locate the four screws around the light perimeter that holds it in place. Remove these screws with a flathead or Phillips screwdriver, whichever that specific year of car and light fixture call for.
4Place one hand on the back of the light fixture and one on the front. Gently but firmly push the light towards the front of the car. Stop pushing when you have pushed it forward 2 to 3 inches.
5Work your fingers behind the light fixture and disconnect the wires that are connecting the light to the car. There will be up to three sets of wires. Pull the wires away from the unit gently to disconnect them and set the old light aside.
6Remove your new headlight from the packaging and slide it into the space where the old light unit was. Connect the wires in the back of the new light, push the light into place, and secure the light into place with the four new screws that came with the new unit or the old screws.
7Turn the lights on to test your new headlight. If for some reason it does not work properly, unscrew the unit and make sure the wiring is properly connected. If not, take the new unit back and get a different one to try.
What are the Functions of Carbon Brush

Carbon brushes are electromechanical conducting devices that connect to moving parts to provide an electric current. They are typically used in motors, generators and alternators. Many carbon brush uses exist, but the three basic uses are in household applications that run on alternating current (AC), automotive applications that run on direct current (DC) and industrial applications that run on both AC and DC.
Household
Carbon brushes are a common component in household appliances such as power tools, gardening equipment and office equipment. Vacuum cleaner turbines, hair and hand dryers, and washing and drying machines are also common applications of this type of carbon brush, which is generally much smaller than its industrial or automotive counterparts. Micro-carbon brushes, for example, are precision parts designed for toys, electric razors, and audio and video equipment. In such small dimensions, carbon brushes are often placed inside tiny battery-operated mini-motors designed to transmit power silently and with the least amount of friction to moving parts such as wheels and razors.
Automotive
Cars generally use small and auxiliary carbon brushes for DC motors, starters and alternators. Alternators are devices that convert mechanical energy to electrical energy. They consist of a wire-coiled rotor that produces a magnetic field when a current runs through it. Automotive carbon brushes are used to supply the current to the wire coil in the alternator. Automotive carbon brushes can be found in most passenger vehicles, motorcycles, trucks and oil- and diesel-fueled cars. Even smaller, specially designed carbon brushes are used in steering wheels and contacts for airbags.
Industrial
Industrial carbon brushes are used on large commutator machines, in which the current between the rotor and external circuit is periodically reversed. These include AC and DC motors, slipring rotors, traction motors, turbogenerators, windmills, hydro power stations and steel, cement and paper mills. Industrial carbon brushes also can be used to power battery-driven cars, cable cars and trolley buses, and they are often used in construction vehicles such as forklift trucks and cranes. Brushes connect the generator to the rotor through the commutator, which has copper segments, or lands. The brushes bear the brunt of wear and tear between the rotating rotor and the non-moving generator while conducting electricity between them. Industrial brushes are specially designed to withstand extreme temperatures.
How to Remove the Rear Seats in a 1999 Acura TL

The Acura TL was debuted in 1995 as a mid-size luxury sports vehicle. You can remove the rear seat on your 1999 Acura TL at home, saving yourself a trip to the dealer or mechanic. Sometimes it may become necessary to remove the rear seat so that you can have it reupholstered or replaced. It is kind of a heavy, bulky job but it doesnt take long to do. Allow about 30 minutes or less to complete the task once you have obtained a socket wrench set.
Instructions
- 1
Slide the front seats all the way forward to give yourself some room to work in the back.
2Lift up the back of the rear seat cushion in the crevice to find a bolt. Remove the bolt with a socket wrench.
3Pull the latches underneath the rear seat cushion forward to free them from their hooks. Remove the seat cushion from the Acura out one of the side doors.
4Find three bolts under the seat back and two above the seat back near the headrests. Remove all five bolts with a socket wrench.
5Pull the seat back forward and out of the vehicle.
Jeep Liberty Wire Harness Problems

In 2004, Chrysler informed the National Highway Traffic Safety Administration that it would recall certain Liberty model Jeeps equipped with 3.7-liter engines, citing problems with the two valve cover studs. In 2006, Chrysler recalled some two-wheel drive Liberty vehicles with 3.7-liter engines, because of issues with the left oxygen sensor wiring harness.
Significance
If affected Jeep owners dont repair the defects prompting the recall, the wiring harness issue could cause a fire under the hood. Liberty owners should contact the manufacturer or the NHTSA, supplying their Jeeps VIN number, to see if its been recalled.
Risks
In both recalls, the risk of fire stems from the chance that the alternator harness and/or the wiring harness could come into contact with a hot exhaust pipe, leading to potential personal injury and/or property damage.
Remedies
Dealers must add protective caps to the valve cover studs and re-route affected wiring harness to repair the alternator wiring harness issue. To repair the oxygen sensor wiring harness problem, dealers must secure the excess length of the wiring harness and fix any damage already done to the wiring.
How to Install Head Studs
Head studs increase the holding power between the engine block and the engine head. This keeps an installed head gasket in place when under the stress of a high horsepower engine. A head stud looks similar to a bolt without the hex head. The coarser threads of the stud hold secure in the threaded holes of an engine block and the finer threads hold a nut to keep the head secure to the engine block. Improperly installing head studs will cause damage to the engine block and to the head, costing you a lot of money in replacement parts.
Instructions
- 1
Spray brake cleaner into a threaded engine block hole. Push the end of a pipe cleaner into the hole to clear it of debris. Pull the pipe cleaner from the hole. Rotate the pipe cleaner and push the other end in the hole. Repeat the process of spraying brake cleaner and cleaning the hole with pipe cleaners until the end of the cleaner pulls from the hole free of debris.
2Thread a chaser tap in the cleaned hole. Run the tap to the bottom of the hole. Remove the tap. Spray brake cleaner in the hole. Push a wire brush in the hole. Pull it quickly from hole. Repeat the wire brush cleaning three to four times. Blow compressed air in the hole to remove remaining debris. Clean each threaded engine block hole as described.
3Apply red threadlocking sealant on the larger coarse threads of the head studs.
4Align the sealant coated threads of each head stud with a threaded engine block hole. Turn each bolt clockwise with the correctly sized wrench until the stud tightens in the hole and the bottom of the stud hex nut sits tight to the top of the engine block.
How to Replace the Water Pump on a 2001 Grand Cherokee 6 Cylinder
The Grand Cherokee is a mid-size sport utility vehicle produced by the Jeep division of Chrysler. The WJ versions of this vehicle include the 1999 to 2004 models and represent a complete redesign over the previous Grand Cherokee. The most common engine in the 2001 Grand Cherokee is a 6-cylinder, 4.0-liter engine. The replacement of the water pump on this engine requires you to remove additional components to access the water pump.
Instructions
- 1
Allow the vehicle to sit over night to ensure the coolant will not burn you. Place a container under the radiator drain and remove the drain cock. Drain the contents of the radiator into the container and replace the drain cock. Store the coolant for later use.
2Disconnect the cable for the negative battery terminal with a socket wrench so you dont start the engine inadvertently. Detach the electrical connector for the cooling fan and remove the accessory drive belt. Disconnect the cooling fan and its pulley from the engine.
3Remove the retaining bolts for the water pump pulley with a socket wrench and disconnect the power steering pump. Detach the coolant hose and heater hose from the water pump. Disconnect the mounting bolts for the water pump and remove the water pump. Discard the gasket for the water pump.
4Clean the mating surfaces of the water pump and engine to remove any traces of the old gasket. Place a new gasket onto the new water pump and install the water pump to the engine. Torque the mounting bolts for the water pump to 17 foot-pounds with a torque wrench.
5Attach the heater hose and radiator hose to the water pump. Install the water pump pulley and torque its mounting bolts to 20 foot-pounds. Connect the power steering pump and the cooling fan assembly. Torque the mounting bolts for the cooling fan to 31 inch-pounds. Install the accessory drive belt and attach the electrical connector for the cooling fan.
6Connect the battery cable to the negative terminal with a socket wrench and ill the cooling system. Start the engine and check for leaks in the cooling system.
How to Reset a Honda Element Computer

You can reset the computer on your Honda Element right from your home garage, saving yourself a trip to the mechanic. The Honda Element is equipped with an onboard diagnostics (OBD) computer, which receives and stores trouble codes from sensors positioned throughout the vehicle. When it receives one of these codes, it alerts you by illuminating a warning or service light on the instrument panel. Once you have had the problem looked at and fixed, you or your mechanic will need to reset the computer in order to shut off the lights and keep your vehicles computer functioning properly.
Instructions
- 1
Find a port under the dashboard on the drivers side of the vehicle that is the same size and shape as the connector on the OBD code scanner. Plug the scanner into the port.
2Put the key into the ignition and turn it to the "on" position but dont start the engine. The vehicles power turns on the scanner. Let the scanner read the trouble codes.
3Press the "reset" or similar command on the face of the scanner to reset the vehicles computer. Unplug the scanner and shut off the vehicle.
4Wait 60 seconds then start the engine. Verify that the warning and service lights have shut off on the vehicles instrument panel.
What Are Automotive Replacement Parts

If you have owned a car for any length of time, you have probably already figured out that cars will break down from time to time. Cars are made up of a complex arrangement of mechanical and electronic parts, all of which have the capacity to fail or malfunction. Fortunately, replacement parts exist to replace virtually any component on your vehicle that breaks.
Replacement Parts
Automotive replacement parts are parts that are made to replace existing parts when they break. Replacement parts are manufactured by both the vehicle manufacturers and aftermarket parts manufacturers. You can by a replacement for virtually every component on your vehicle, including body panels, knobs, dials, wiring, belts, pumps, pulleys, sensors and even the mechanical parts such as the engine and transmission. Granted, if your vehicle is not a common make or model, you will often have a harder time finding replacement parts or have to get used parts, but the components are still out there and available for purchase.
OEM Parts
Original Equipment Manufacturer parts (OEM) are auto parts that were manufactured by the same company that made the original part. This means that the part is identical to the original item that was in your car in every way possible. OEM parts are often considered desirable by mechanics and vehicle restorers because they keep the vehicle in as close to original condition as possible.
High Performance Parts
Performance parts are designed to be more sophisticated and higher quality than the original manufacturer parts. These may correct design flaws that the original parts experienced. They may also be designed to improve performance by increasing horsepower or the capacity of a component. for example, a larger radiator to improve efficiency of the cooling system.
Used Parts
There is a large market for second-hand or rebuilt auto parts. Some components, such as alternators and starters, can be professionally rebuilt and used again. Rebuilding typically involves replacing the internal components of the part. Used parts can be purchased from a parts reseller such as a junkyard. Used parts tend to be less expensive than new parts and many used parts come with a warranty.
Wednesday, October 15, 2014
My Lexus RX 300 Cigarette Lighter Wont Stay In

If your Lexus RX 300 cigarette lighter will not remain in place when pushed inward, there are a few steps you can take to repair the problem. You can fix a cigarette lighter for a Lexus RX 300 as a do-it-yourself project, but if your efforts do not solve the problem, you should take it to your local Lexus dealership for repair service.
Instructions
- 1
Retrieve your manual. Then, check the fuse box. The fuse box of a 2001 Lexus RX300 is located behind the coin holder drawer, to the left of the steering column. Check your manual to see which fuses operate the cigarette lighter socket. If the fuse is blown, you will see a small, broken wire in the interior of the plastic shell of the fuse. Replace a blown fuse with a fuse rated for the same amperage.
2Pull out the ash tray to gain access to the lighters wiring connector. The 12 volt and ground wires are connected to the socket. Also, identify an L-shaped wire that has a rubber coating. This is a fuse. Find the two small terminals at the bottom of the L-shaped, rubber-coated fuse. Remove the fuse, then bend a paper clip in an L-shape and place it where the L-shaped, rubber coated fuse was positioned. You should position the L-shaped paper clip at the end of the socket.
3Remove the ash tray from its panel. Remove any small Phillips screws. Then, remove each spring found on the side of the ash tray.
4Disassemble the lighter assembly or lighter housing, by loosening a hex nut at the bottom of the lighter assembly. To accomplish this task, the panel must be off. Then, reassemble the lighter assembly. Check to see if your lighter will stay in position when pushed inward.
5Replace the lighter with a standard size cigarette lighter from your local auto parts store. If a fuse is not burned out, and if disassembling and reassembling the lighter socket still does not help the lighter stay in, take your RX 300 to a Lexus dealership.
6Explain the problem with the RX300 cigarette lighter fixture, and ask a Lexus service professional to inspect your cigarette lighter socket. The dealership should inspect your RX300 to check for any possible wiring or electrical problems.
Wednesday, August 27, 2014
1998 Subaru Legacy Abs Wheel Sensor How to
The wheel sensor system on a 1998 Subaru Legacy is directly controlled and monitored by the anti-lock braking system, or ABS, computer. It order to determine which wheels are locking-up, the ABS computer monitors the speed of each wheel individually and compares that speed to the vehicle speed sensor value and the other front wheel. In the event of a wheel lock-up, the ABS computer selectively limits brake pressure until the wheels return to a normal rolling condition. Replacement wheel speed sensors are available for purchase from auto parts stores, Subaru dealerships, and online parts websites.
Instructions
Front Sensor Removal
- 1
Break the lug nuts loose with a lug nut wrench. Raise the front of the vehicle with a jack and support it with jack stands. Remove the lug nuts and tire.
2Locate the wheel speed sensor on the inside of the steering knuckle. It is made from black plastic and has a single wire protruding from it that runs up the inside of the strut assembly. Disconnect the sensor connector inside the engine compartment.
3Remove the bolts holding the sensor harness to the strut assembly with a ratchet and metric socket. Remove the bolts holding the wheel sensor to the knuckle housing with a ratchet and metric socket.
4Remove the sensor from the housing by gripping the sensor between your thumb and foinger and slowly twisting it back and forth while pulling out of its mounting hole.
Front Sensor Installation
- 5
Slide the new sensor into its mounting hole on the steering knuckle flange. Insert a feeler gauge between the sensor reluctor wheel and the sensor hole. Press the sensor down into its mounting hole and set the clearance using the feeler gauge. The specified value is 0.9 to 1.4 mm.
6Install the sensor retaining bolt and tighten it to 17 to 31 foot-pounds using a torque wrench.
7Feed the sensors wire up to the engine compartment and reconnect it to its primary electrical connector. Position the sensor wire bracket on the strut assembly and reinstall the bracket retaining bolt. Tighten the bolt to 17 to 31 foot-pounds using a torque wrench. Reinstall the tire and lug nuts. Lower the vehicle to the ground and tighten the lug nuts to 65 foot-pounds, plus or minus 7 foot-pounds.
8Check to make sure that the sensor wire isnt distorted or strangled. Test drive the vehicle to make sure that the sensor operates properly and that no ABS error lights illuminate on the dash board.
Rear Sensor Removal
- 9
Break the rear lug nuts loose with a lug nut wrench. Raise the rear of the vehicle with a jack and support it with jack stands. Remove the lug nuts and tires. Remove the bolts holding the front seat cushion hinges to the body with a socket and metric ratchet. Lift up the front edge of the seat cushion and detach the rear hooks from back of the seat. Remove the lower seat cushion from the vehicle.
10Remove the bolts holding the lower-edge of the back cushion to the body. Pull the release strap to release the folding lock on the top of the back cushion. Fold the cushion down toward the body and disengage its retaining hooks. Remove the back cushion from the vehicle. Disconnect the ABS connector thats beneath the rear seat and push the wire through the rubber grommet hole in the body.
11Slide underneath the rear of the vehicle on a mechanics creeper and remove the bolt holding the rear ABS sensor to the backing plate behind the wheel hub. Remove the bolt holding the sensor wire to the trailing link. Pull the sensor out of the backing plate and remove the sensor assembly from the vehicle.
Rear Sensor Installation
- 12
Set the sensor wire into position on the trailing link and reinstall the trailing link bolt. Tighten it to 17 to 31 foot-pounds using a torque wrench. Reinstall the ABS sensor into the backing plate and set the gap between the backing plate and the sensor with a feeler gauge; the specified value is 0.7 to 1.2 mm. Tighten the sensors retaining bolt to 17 to 31 foot-pounds with a torque wrench.
13Feed the ABS wire through the rubber grommet and into the cabin, then reconnect the ABS sensors electrical connector inside the vehicle. Set the seat back cushion into position and attach the lower seat cushion hooks to the mounting holes. Fold the seat back cushion up until it latches into position, then reinstall the seat back cushion retaining bolts.
14Set the lower seat cushion into position and engage the rear latches with the retaining hooks on the back of the seat. Fold the seat down and reinstall the seats retaining bolts. Reinstall the tires and torque the lug nuts to lug nuts to 65 foot-pounds, plus or minus 7 foot-pounds. Lower the vehicle back to the ground, then test drive it to ensure that the sensors operate properly.
Can I Use Starting Fluid on a 6 9 Diesel
International surely had no way of knowing just how important their new 6.9 liter diesel would become when they introduced it in 1978. While the 6.9 liters 170 horsepower and 338 foot-pounds of torque arent particularly impressive by todays standards, the fact is this engine laid the foundation for a partnership between International and Ford that would eventually culminate in the well-known Powerstroke series.
Starting Fluid
Starting fluid is a mixture of various volatile hydrocarbons, primarily diethyl ether and heptane, butane and propane. Starting fluid has a much lower auto-ignition temperature than gas or diesel, making it an ideal fuel to start engines with ailing ignition or fuel-injection systems. The 6.9 liter diesel is a simple engine, and responds to starting fluid the same way that any other diesel does. A three to five second burst of starting fluid sprayed directly into the intake tube should be all you need if the engine is capable of starting at all.
The Addiction Myth
Some old-timers will tell you that starting fluid is a death sentence for any engine, especially diesels. According to the wisdom of ages, diesel engines get "addicted" to starting fluid and will forever more require it after the first application. This is patently untrue; starting fluid is a fuel just like any other and your engines physical structure in no way changes just because you start it with ether. More likely, this "addiction" is simply a worsening of whatever condition it was that forced you to use starting fluid in the first place.
Saturday, June 7, 2014
How to Weld an Exhaust System Pipe

Welding is a skill that some people take years to perfect, and it can be done in a multitude of different ways. One of the most common and inexpensive methods of welding is MIG welding, which will work perfectly for an exhaust system. Welding two exhaust pipes together will seal the joint and make the exhaust system leak-free. This is a complicated process and should be done by someone with experience in welding; otherwise, you risk injury.
Instructions
- 1
Jack up the car using a jack and put it on four jack stands. Make sure there is enough room for you to move easily around the underside of the car. Crawl underneath the car and locate the section of exhaust tubing you want to weld. Examine the wall thickness of the tubing.
2Compare the wall thickness of the tubing with the system setup diagram on the inside cover of the welder. Set your welder to the settings listed for that gauge of metal. These settings will vary with each welder.
3Clamp the exhaust lines together using the exhaust clamp, making sure to butt the two pieces of exhaust tubing together perfectly. Put on the welding helmet and gloves.
4Set the ground clamp for the welder on the exhaust. Place the end of the welder approximately 1/8 inch away from the surface of the exhaust. Pull the trigger. Work the puddle you see through the helmet into crescent shapes, working your way back and forth until you have a 1 inch long weld. Repeat the process on the other side of the exhaust clamp.
5Remove the exhaust clamp then weld the remaining perimeter of the exhaust tubing. Remove the vehicle from the jack stands using the jack.
Friday, June 6, 2014
Air Ride Suspension Components
Air ride was first used in 1909, but it was quickly eliminated as the systems had a tendency to leak. Properly functioning air ride systems were a common feature in luxury automobiles in the late 1950s. These systems use several components to change the ride quality and height.
Compressor
The air compressor is typically hidden behind the rear seat or in the trunk. The compressor uses the 12 volt power to run an internal piston and build air pressure. This air is used to adjust the ride height or quality.
Pressure Switch
The pressure switch is an integral part of keeping this system operating properly. This pressure switch measures the pounds per square inch (psi) in the system and turns the compressor on and off as needed.
Air Bags
The air bags are underneath the vehicle and connected to the suspension. The air bags are rubber bags that fill with air provided by the compressor. The bags perform a few functions: ride height adjustment and ride style. The bags raise the vehicle by inflating and lower the vehicle by deflating.
Lines
The air lines in this system transfer air from the compressor to the air bags. These lines are typically rubber with braided steel covers.
Adjustment Switch
Some trucks and SUVs have a switch inside the cabin to adjust the system. The switch is designed to raise and lower the vehicle at the drivers command.
Disabling Switch
Some vehicles, Ford, Lincoln and Mercury primarily, have automatic adjusting shocks that work whether the vehicle is off or on. When you lift these vehicles, for any reason, the system senses the change in pressure and begins inflating the air bag. When this happens, it can cause the system to blow a hole in the air bag. This is why the disabling switch was put on these vehicles. This switch is typically in the trunk.
How to Replace the Fuel Filter in an 85 Buick Century
The fuel filter on a 1985 Buick Century is designed so that gasoline flowing to the engine is free of harmful debris. The fuel pump, located inside the gas tank, has a built-in strainer. This keeps large debris from leaving the tank but smaller debris and sediment can get past the strainer. If not changed, the small debris will eventually clog the fuel filter; this can affect gas mileage and engine performance. Fuel filters should be changed annually or every 30,000 miles.
Instructions
Remove the Fuel Filter
- 1
Open the hood and locate the fuse panel. Open the fuse panel and locate the fuel pump relay. Pull it out by hand.
2Start the engine and let it run. The engine will stall once the fuel system has depressurized. Turn off the engine and replace the relay back in to the fuse panel. Close the fuel panel.
3Crawl under the car behind the driver-side rear wheel well and look for the fuel filter. The fuel filter is canister-shaped with a fuel line entering and exiting the filter; it will be in a mounting bracket on the frame rail. You can also trace the fuel line from the gas tank to find the fuel filter.
4Place a drain pan under the fuel filter to catch any gas in the fuel lines or the fuel filter.
5Disconnect the inlet fuel line from the fuel filter by pinching the tab on the quick-disconnect fitting and pull the fuel line off the fuel filter. If the fuel line is held on by a hose clamp, loosen the clamp with a screwdriver. Remove the outlet fuel line the same way.
6Use a socket wrench to loosen the bolt on the mounting bracket and slide the fuel filter out of the bracket. Discard the fuel filter.
Install the Fuel Filter
- 7
Slide the new filter in the bracket. Make sure the arrow on the fuel filter is pointing toward the front of the car. The arrow designates the direction of fuel flow. Tighten the bracket bolt with the socket wrench. The fuel filter should be tight in the bracket.
8Push the inlet fuel line onto the fuel filter until it clicks in place. If held on by hose clamps, push the fuel line over the fitting on the fuel filter. Slide the hose clamp over the hose and fitting and tighten it with a screw driver. Do the same for the outlet fuel line.
9Start the engine and let it to run for at least 5 minutes.
10Check the fuel filter and fuel lines to make sure there are no gas leaks.
How to Repair a Driveline
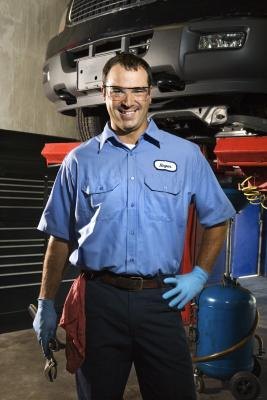
An automobile driveline connects the engine to the axles, giving them the power to turn and move the vehicle. It connects the engine to these parts via a number of joints and clamps. When these parts are faulty, the car might shudder when you give it gas, or it might clunk loudly when the transmission is downshifted. The noise, as well as leakage at the joints, are signs that you need a repair. Most home mechanics can handle minor repairs, which involve replacing rubber boots and adding grease. But for major repairs, its best to take the vehicle to a licensed automotive mechanic. If you are doing the work yourself you will need access to a hydraulic car lift.
Instructions
- 1
Drive the car into a workspace with a hydraulic lift. Attach the lifts wheel or frame locks onto the car. Initiate the lift so that the car is suspended. Place the lift safety blocks into position to secure the lift arms in place. This will ensure the the car wont crush you if the hydraulic pressure begins to fail.
2Locate the CV joint boots at the end of the driveline. Examine them for tears or leakage of grease and oil. If you find tears or leaks, pull the old rubber boot off the linkage because it needs to be replaced. Examine the CV link of the driveline to the axle and the opposite end at the transmission. Use a flashlight if visibility is poor. Look for corrosion or rust if the CV boot was torn, opened or exposed.
3Regrease the CV joint and insert a new CV boot onto the driveline axle and transmission connections if the joints are in good working condition and the rubber boot was bad. If the boot is still good and shows no signs of tears or leaks, slip it back onto the joint.
4Lower the car and bring it to a licensed mechanic if you can see clear signs of corrosion to the CV and transmission joints of the driveline. Have the mechanic lift the car with his equipment. Show him what youve observed and where the corrosion is. Have the mechanic replace the driveline and joint couplings as necessary.
How to Pick a Flexplate for SBC

One thing to remember when picking a flexplate for a small block Chevy (SBC) is that the 1986 and newer Chevy small block engines require a weighted flexplate to help keep the vibration out of the engine. If you bolt an old style neutral balanced flexplate to an engine when it requires a weighted flexplate, you will feel considerable vibration from the engine. The weighted flexplate has 14 1/2-inch diameter and 168 teeth, and requires an offset bolt pattern starter. The smaller flexplate has a 12 3/4-inch diameter and uses a starter with the two bolts adjacent to each other.
Instructions
- 1
Determine the flexplate needed. Count the teeth on the flexplate to be replaced. If it has 168 teeth it is the larger one. The other choice is a 153-tooth plate. If you dont have a flywheel on the engine and the engine is 1986 or newer, it needs the larger-weighted flexplate.
2Select the flexplate manufacturer. If the vehicle is expected to last a long time, then use a high quality GM replacement flexplate. The GM original equipment flexplate is more expensive. If the vehicle has a low life expectancy, then the purchase of a used or aftermarket flexplate should suffice.
3Inspect and clean any used flexplate with spray brake cleaner before purchasing it. Check for hair line cracks in and around the crank bolt holes and be sure the teeth are clean and not worn.
4Match up the flexplate with the proper starter. The 168-tooth flexplate uses a starter that has bolt holes in the mount that are offset or staggered. The smaller plate uses a starter with mount holes that are adjacent to each other
Specifications of a Car Battery
Examine battery life and quality when purchasing a new car battery. The make, model and year of a car are also considerations in purchasing the appropriate battery. Understanding the various specifications of a battery allow the purchaser to make an informed decision. An improper battery creates more difficulty in starting your car under adverse weather conditions.
CCA or Cold Cranking Amps
The batterys cold cranking amps (CCA) rating is one of the most important specifications of a car battery. The CCA is defined as the discharge loads, which are measured in amps, that a battery with a full charge delivers for 30 seconds at 0 degrees Fahrenheit and still maintains the voltage at or above 7.2 volts. The CCA rating needs to meet or exceed -- based on the climate of your area -- the cars original equipment manufacturer (OEM) cranking requirements. Colder climates especially require higher CCA ratings because of the increased power needed to crank a sluggish engine with a cold battery.
RC or Reserve Capacity
Another specification of a car battery is the reserve capacity (RC), according to the Auto Guide website. The number of minutes a battery at full charge can be discharged at 25 amps at 80 degrees Fahrenheit until the voltage drops below 10.5 volts is the definition of the RC. By connecting either two 6 volt batteries in a series or two 12 volt batteries in parallel, the RC is boosted if necessary. More RC is better whether the climate is hot or cold.
Series Number
The series number of a battery is an alphanumeric designation that matches up the correct shape and size for the model of car, according to the Cars Direct website. Series numbers appear like 24, 78R or 22F, and so on. The series number on car batterys specifications is an indication of the proper battery for the year, make and model of the vehicle.
How to Remove a Cylinder Head From a 1988 Sportster

Head removal for a 1988 Evolution-powered Sportster is the same whether the motorcycle has an 883 cubic centimeters or 1200 cubic centimeters engine. It can be accomplished by a skilled mechanic without removing the engine from the frame or removing the gas tank. It is a chore that is easier to describe than to do, but the tear down should not take longer than 90 minutes. An entire top end job including the removal of both cylinder heads and reassembly is considerably more complicated and takes significantly longer.
Instructions
- 1
Close the petcock. Run the motorcycle in neutral until the bike stops. Disconnect the enrichener knob and cable from the clip under the fuel tank.
2Remove the air cleaner cover after loosening the two the bolts on the front of the cover with an Allen socket and a socket wrench. Disconnect the breather tubes from the top of the air cleaner.
3Remove the air cleaner, then the air cleaner backing plate with an Allen socket and socket wrench.
4Loosen the fuel line from the carburetor with a flathead screwdriver and remove the fuel line by hand. Remove the idle and throttle cables from the throttle cam on the top front of the carburetor.
5Remove the carburetor and the enrichener assembly from the engine by pulling the carburetor from the intake manifold.
6Disconnect both header pipes from the exhaust manifold on the right side of the motorcycle with a hex socket and socket wrench. Remove the copper crush gaskets from the exhaust manifold.
7Loosen both oxygen sensors from the header pipes with an open end wrench. Disconnect the mufflers from the muffler support bracket with an open end wrench.
8Pull the entire exhaust system from the motorcycle.
9Disconnect the spark plug wire from the cylinder head you intend to remove. Remove the spark plug with a spark plug socket and a socket wrench.
10Loosen the 6 bolts that hold the rocker cover to the cylinder head one half turn at a time in a crossing pattern with an Allen wrench. Remove the rocker box cover.
11Remove the metal D-ring. Remove the rocker box cover gasket.
12Unbolt the breather assembly from the rocker arm support plate with a hex socket and a socket wrench.
13Cut both pushrods under the head you intend to remove with bolt cutters. Remove the pieces.
14Gradually loosen all four cylinder head bolts in the exact sequence described in the service manual for your motorcycle one quarter turn at a time with a hex socket and socket wrench. Remove the head after all four head bolts are completely loose.
How to Reset the Air Bag Lights in a 1995 Nissan Sentra

You can reset the airbag light on your 1995 Nissan Sentra without the aid of any special tools. The Supplemental Restraint System (SRS) light will illuminate on the instrument panel when there is a malfunction with the airbag assembly. When this light turns on, have the vehicle towed to a mechanic rather than risk driving it. Theres always the chance the airbag will accidentally deploy while you are driving it. When the problem has been repaired, shut off the SRS light yourself.
Instructions
- 1
Look for and open the fuse panel cover. You can find it underneath the steering column. Pull down on it from the top using your fingers.
2Find the yellow plug. This is the electrical connector for the airbag system. Pull this plug out of the panel.
3Wait 10 minutes, then secure the yellow plug back in place. Put the fuse panel cover back on.
4Put the key into the ignition and start the engine. Look at the instrument panel to verify that the SRS light has turned off.
How to Disable the Airbag Light on a Ford Mondeo
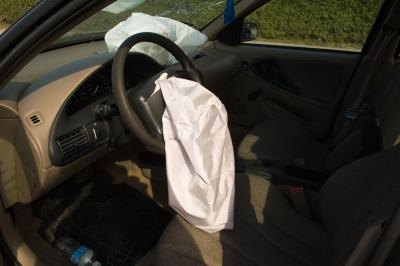
The airbag warning light in a Ford Mondeo may illuminate when the airbag is malfunctioning. After you have had the airbag assembly looked at by a mechanic and fixed, you need to reset the airbag or SRS warning light on your Mondeo. You need to purchas a diagnostic reset tool from your dealership or any auto parts store to do this job.
Instructions
- 1
Locate and open the fuse panel which can be found underneath the steering column on the dashboard. Pull down on it from the top with your fingers.
2Plug the connector end of the diagnostic reset tool into the pinned receiver port on the fuse panel.
3Put the key into the ignition and turn it to the "II" position. Wait for the diagnostic reset tool to stop blinking. This means the SRS light has been reset.
4Unplug the diagnostic reset tool and turn off the vehicle.
5Turn the engine on and verify that the SRS light has shut off of the instrument panel.
How to Fix Large Cracks on a Windshield

If your vehicle gets old enough, chances are your windshield will get chipped or cracked. Replacing an entire windshield can be costly and is not environmentally friendly. In many cases windshields dont need to be replaced, particularly if the damage is minor. Most small chips and cracks can be easily repaired. You can do the job yourself in a few steps.
Instructions
- 1
Prepare the windshield by thoroughly cleaning the cracked area. Before you begin the repair process, make sure the windshield is clean, free of debris, and completely dry.
2Take a razor blade and scrape off any excess glass particles that might be trapped in the crack itself, as well as any dried sap, bug carcasses, or other debris.
3Clean the windshield thoroughly with soap and water, and let dry. Once completely dry, apply the glass cleaner solution.Solutions come in a variety of types, including chemical-based and eco-friendly.
4Follow the directions on the auto glass repair kit, making sure you follow the exact steps. The synthetic glass resin used in these kits can be volatile if not applied correctly.
5Apply the syringe of liquid glass compound to the inside of the crack, snapping and pulling the syringe across the length of the crack slowly. Use your clock or watch to precisely time these motions so the resin will fill in the crack without allowing any trapped air bubbles.
6Fill in the entire crack from end to end with the resin, then let it sit under direct sunlight or ultraviolet lamp. The UV rays will chemically alter the resin from a liquid to a solid state.
7Let the resin set for several hours to allow the curing process to finish. Once finished, use your razor blade to scrape any excess resin from the windshield.
What Is a Crank Position Sensor

The crankshaft position sensor is an electronic component designed to fine-tune the timing of a vehicles engine. The sensor works with the vehicles on-board computer to ensure the vehicle runs at optimal performance.
Purpose
The crankshaft position sensor monitors the position and speed of the crankshaft to control the ignition system timing. The component aids in variable valve timing by monitoring the movement between the vehicles pistons, valves and the engine, noting the engines revolutions per minute.
Function
Made from magnets and an inductive coil, the crank position sensor is positioned next to the crankshaft. The crankshaft has several pins spaced an equal distance apart which is read and calculated by the magnets within the sensor as the crankshaft spins.
Location
These sensors are located in the lower front of the engine block either directly next to the crankshaft, within the main crank pulley or the flywheel. The crankshaft position sensor can be identified as a long, thin, black cord.
German Made Impact Tools

When it is important that a screw or a bolt is very tight, or if you need to loosen rusty or too-tight ones, an impact tool does the job. It converts the downward impact of its motor into a turning motion, which loosens almost any tight nuts, bolts or screws. With the fine craftsmanship of impact tools made in Germany you cant go wrong. Several well-known German companies produce impact tools for the professional or the hobbyist.
Elora Werkzeugfabrik
Elora Wekzeugfabrik is known for the manufacture of cutting-edge hand tools, and their impact tools are in demand among many professionals. Elora focuses on impact screwdrivers and screwdriver sets, hex bits and adapters. Elora impact screwdrivers are for left- and right-hand use, and feature a non-slip grip. Elora impact screwdriver sets feature a driver, several different-sized bits, and a hex adapter. Hex adapters, different bit inserts and Phillips bits can also be purchased separately.
Gedore Tools
The Gedore company has been manufacturing quality tools for over 90 years. The company claims that its tools are known for their safety features, precise manufacture, excellent ergonomics and long life. Gedore offers several impact drivers and impact screwdriver sets. Their impact extensions come in different sizes and can be used on all popular impact nut drivers. They also have impact sockets for use with air-operated and electric nut drivers, square drives which can be used to screw in and unscrew nuts from 1/4-inch to 2 1/2-inch diameters, and impact reducers in different sizes. Car impact socket sets are also available.
Stahlwille
Founded under the name of Edualrd Wille GmbH & Co.KG, Stahlwille manufactures high-grade tightening tools of all kinds. They specialize in machine-powered impact tightening tools, such as wrenches, socket tools, drives and connectors. They offer long impact sockets and impact hex sockets, in sets or singly. They also offer impact sets, which include drivers, adapters and different sockets. Different drivers, some with inside hexagon for screwdriver bits, also come separately.
Hazet
Hazet was established in 1868, and today the company is among the most advanced in Europe. Hazet offers a popular line of impact wrenches, covered with a shock-resistant ultra-light plastic or magnesium housing, giving them maximum performance with little weight. The wrenches also have a powerful twin-hammer mechanism and several power settings for forward and reverse. Their cold-insulated handle minimizes vibrations, and the exhaust air is guided downwards through the handle. Hazets impact wrenches come in several different sizes.
How to Lower Your 883 Sportster

You can lower the front and the back of a Harley. Numerous aftermarket vendors sell "drop in" fork lowering kits that will lower your front end. But lowering the front end decreases ground clearance, which means your bike will no longer -- barely -- clear that parking lot speed bump. Getting hung up on that bump will damage your bike. Since this is an 883 Sportster, usually an entry-level Harley, a better place to begin might be to slightly lower the rear end by installing shocks that are one inch under stock length. Your seat will be lower, and an entry-level biker can do it himself.
Instructions
- 1
Raise the Sportster to fully upright and level by slightly raising the bike on a motorcycle jack, by driving the front wheel into a motorcycle chock, or by clamping the front wheel upright in a motorcycle clamp.
2Unbolt the lower right shock mounting bolt that connects the old shock absorber to the frame. The bolts on Sportsters shipped after 2005 come off with an Allen socket. Earlier models unfasten with a deep well hex socket.
3Remove the bolt, nut and washer. Remove the top mounting bolt on the right shock and save all the hardware.
4Remove the left shock by repeating these steps.
5Spread three or four drops of thread locker over the screws of all the mounting bolts with your finger. Bolt the new, 1-inch-under-standard-length shock absorbers into the same holes with the same bolts that held the original shocks in place. Use a torque wrench and an Allen or deep well hex socket to tighten the bolts to 48 foot pounds of torque.
6Lower the jack or remove the bike from the chock or clamp. Push the rear end of the bike down and let it rebound up to be sure that the new shocks work.
Thursday, May 22, 2014
Harley Flywheel Assembly Tutorial

Harley-Davidson flywheel assemblies have undergone one major change in the last century. From 1909 until 1986, Harley crankshaft assemblies were actually constructed of numerous individual parts. Harley simplified this construction in 1987. One dives deep into the crankcase either because one has thrown a rod or otherwise blown ones engine apart or because one wants to balance the flywheels. Nothing else is worth it. Reaching the flywheel assembly requires the complete disassembly of the rest of the engine. Here is what you can do to a flywheel assembly on a post-1986 engine after you have taken everything else apart.
Instructions
- 1
Hold the flywheel assembly so it does not tumble out of the left crankcase half. Rotate the bottom end assembly in an engine stand so the assembly is upright and the flywheel shafts are horizontal.
2Caully slide the flywheel assembly out of the left crankcase.
3Install aluminum vise jaws and shop rags in the jaws of a bench vise. Clamp the flywheel support structure in the vise.
4Insert the crankshaft end through the hole in the middle of the flywheel support structure.
5Slide the structures knurled locating pin down the slot in the structure to engage the crank pin hole. Hand tighten the locating pin.
6Slide the structures hold-down clamp down the slot to engage the inboard side of the right flywheel half. Hand tighten knurled nut at bottom to secure. Repeat step above to secure the hold-down clamp on the opposite side of the flywheel.
7Position the wedge attachment on the inboard side of the thrust washer. Turn both hex nuts on the bottom of the wedge attachment an equal number of turns with an open end wrench to draw the wedge halves together.
8Install two 6 1/2-inch-long, 3/8-inch bolts with flat washers through the channels in the bridge of a main shaft bearing inner race puller-installer. Thread both bolts into the wedge attachment an equal number of turns.
9Apply graphite lubricant to the threads of the main shaft bearing inner race puller-installer forcing screw. Start the forcing screw into the bridge of the inner race puller-installer.
10Place the cupped side of the hardened plug against the end of the sprocket shaft. Thread the forcing screw through the bridge until the screw makes firm contact with the hardened plug.
11Heat the bearing inner race for 30 seconds with a heat gun. Turn the forcing screw with a breaker bar and hex socket until the thrust washer and bearing inner race move 1/8 inch.
12Loosen the hex nuts on the long bolts in the wedge attachment with an open-end wrench. Turn each nut an equal number of times to separate the halves of the wedge attachment.
13Turn the wedge attachment one half turn and retighten the hex nuts on the long bolts. Tighten each nut an equal number of turns to draw the wedge halves together.
14Heat the bearing inner race for 30 seconds with a heat gun. Turn forcing screw with a breaker bar and hex socket until bearing inner race pulls free of socket.
15Discard thrust washer and bearing inner race. Original post-1986 equipment flywheels are now completely disassembled.
16Reassemble the flywheel assembly with a new thrust washer and new bearing inner race. Other parts may be cleaned and reused.
Car Electrical System Troubleshooting

A vehicle that shows signs of electrical problems can be frustrating, as many people use to tamper with electricity. However, with the right tools and information, even a novice can troubleshoot some of todays common auto electrical issues.
Circuits & Voltage
Components in an electrical circuit cannot be powered without voltage. Theore step one in troubleshooting for electrical problems in a vehicle is to see if voltage is reaching the circuits load point, for example a light bulb. A test light or voltmeter will work well when performing this check.
Circuit Breakers & Fuses
An absence of voltage at the circuits load point could be due to blown fuses or issues with the circuit breaker. Replacing fuses will often only bring about temporary fixes until the problem that caused the blown fuse in the first place is found. A jumper wire can be used to bypass a circuit breaker, allowing you to check it. A working circuit means a non-working circuit breaker.
Intermittent Troubleshooting
Intermittent electrical issues are considered to be the most difficult kind to deal with, and often stem from loose wire connections. Because of this, wiggling the wires while testing for changes in voltage could help reveal the location of the bad connection.
Wednesday, May 21, 2014
How to Remove a 3S FE Cylinder Head
The Toyota 3S-FE engine is a four-cylinder, 2.0-liter engine with a double overhead camshaft. It was produced from 1986 to 2000. During that period, it was the engine that powered various Toyota vehicles, including Camry models for 1987 through 1992. The cylinder block in the 3S-FE engine is iron, and the cylinder head is an aluminum alloy. The removal of the cylinder head for this engine should require four to five hours for an experienced mechanic.
Instructions
- 1
Put a drain pan under the radiator, and open the radiator drain. Allow the coolant in the radiator to drain into the pan. Replace the drain plug. Seal the container, and store it for later use.
2Disconnect the throttle cable and its bracket from the throttle body with a socket wrench if your vehicle has an automatic transmission. For all vehicles, detach the accelerator cable and its bracket from the throttle body. Remove the actuator and its bracket from the cruise control if your vehicle is so equipped.
3Detach the hose from the air cleaner with a socket wrench. Disconnect the alternator and oil pressure gauge from the engine. Loosen the lug nuts on the right front wheel with a lug wrench and raise the vehicle with a floor jack. Support the vehicle with jack stands and disconnect the right front wheel assembly. Detach the splash shield from the right front wheel well.
4Disconnect the lower cross member for the suspension with a socket wrench. Remove the exhaust pipe from the catalytic converter and disconnect the distributor from the engine. Disconnect the electrical connector for the water temperature sender gauge and remove the sender gauge from the vehicle. Detach the switch connector for the cold start injector.
5Disconnect the radiator hoses and emission control hoses from the engine with a socket wrench. Detach the water bypass pipe and the exhaust gas recirculation valve from the engine. Disconnect the air hose for the throttle body and remove the throttle body. Remove the hoses from the power steering unit if your vehicle is so equipped.
6Disconnect the intake manifold from the engine with a socket wrench and discard the gasket. Disconnect the fuel pipe from the injectors and remove the injectors from the engine. Unscrew the spark plugs and remove them from the engine.
7Disconnect the camshaft pulley and the No. 1 idler pulley with a socket wrench. Remove the spring from the timing belt tensioner and detach the No. 3 cover for the timing belt. Support the timing belt to prevent it from shifting on the crankshaft pulley.
8Disconnect the grommets on the cylinder head cover with a socket wrench. Label the grommets to ensure you install them in their original positions. Remove both camshafts from the engine.
9Remove the 10 mounting bolts on the cylinder head with a socket wrench by loosening them in three separate passes. Tap the cylinder head with a rubber mallet to loosen it from the engine block. Place the cylinder head on a clean work surface. Discard the old gasket for the cylinder head. Remove any traces of the gasket from the cylinder head and engine block with a gasket scraper.
How to Reset the Computer on a 1992 GMC Jimmy
Starting in the late 1970s, vehicles were equipped with on-board computers that were specific to each vehicle. This often meant a trip to the dealership service center for diagnosis and computer resets. The 1992 GMC Jimmy was no exception. A GM-specific computer scan tool must be used to read and clear codes as well as reset the computer. In 1996, the second phase of on-board diagnostics standardized the equipment needed to perform this task so most all repair stations could do this for every type of later model vehicle.
Instructions
- 1
Open the hood of your 1992 GMC Jimmy.
2Remove the black, negative battery terminal bolt from the batterys side post with an 8 mm box-end wrench turned counterclockwise.
3Detach the red, positive battery terminal bolt from the batterys side post with the wrench.
4Turn on the headlight switch inside the passenger cab to discharge any stored voltage in the capacitor. Wait five to 10 minutes.
5Reconnect the red, positive battery terminal bolt to the batterys side post first and tighten it with the wrench.
6Reattach the black, negative battery terminal bolt to the batterys side post and tighten it with the wrench.
Tuesday, May 20, 2014
Transmission Problem With Nissan Titan

On Aug. 9, 2004, Nissan North America notified the National Highway Traffic Safety Administration that it would begin recalling certain 2004 Nissan Titans due to a transmission problem that could affect more than 5,000 vehicles.
Defect
Certain Nissan Titan pickups equipped with column shifters may have been equipped with a part that was damaged during assembly. A defective shift lever assembly could cause potentially dangerous transmission problems in these vehicles.
Risk
Damage to the shift lever assembly could result in a malfunction of the part responsible for holding the lever in the park position.
Solution
Nissan began notifying registered vehicle owners affected by the recall in September 2004. Authorized dealers were instructed to inspect and replace defective column shifters. Titan owners experiencing transmission problems may contact Nissan or the NHTSA with their vehicle identification numbers to determine whether their trucks might have been affected.
How to Install a 1995 Harley Davidson Ultra Classic Electra Glide Ignition Switch

When it debuted in 1995, the Electra Glide, like it predecessors the Hydra Glide and Duo-Glide, was called a "Hog." The name was meant to be a frank evaluation of the motorcycle. In days of yore American bikers perred their Hogs "stripped," "chopped" or "bobbed." The mid-1990s Evolution powered Electra Glide retained many of the rider-friendly (though not mechanic-friendly) features of the 1965 Hog, so a simple job like changing the ignition must begin with some stripping. In this case, you first strip the fairing and then the ignition. Assuming that the old ignition is still in the bike, this process follows a few steps.
Instructions
- 1
Tape rags to the front fender to protect the finish. Remove the fairing screws outboard of the left and right speakers with a Torx head driver or socket.
2Loosen the top left and right screws outboard of the fuel and volt gauges and the screws below the right and left sides of the glove box with a Torx driver.
3Remove the front and rear acorn nuts from both the right and left front turn signal lamp brackets with a Torx driver. Pull the front turn signal lamp assemblies from the motorcycle and allow them to hang at the front of the engine guard.
4Remove the previously loosened screws outboard of the fuel and volt gauges. Raise the outer fairing slightly and rest it on a folded rag. Squeeze the two external tabs to disconnect the headlamp jumper harness connector.
5Remove the three outer fairing screws just below the outer face of the windshield with a Torx driver. Remove the two fairing screws just below the left and right wind deflectors with a Torx driver.
6Turn the handlebars to the right and remove the outer fairing screw below the left side of the fairing cap with a Torx driver. Turn the handlebars to the left and remove the outer fairing screw below the below the right side of the fairing cap with a Torx driver. Lift the fairing and headlamp assembly off the motorcycle.
7Insert the ignition switch key and turn to the "unlock" position. Rotate the knob to "access." Depress the release button at the bottom left side of the ignition with a small screwdriver. Push the key and turn it counterclockwise another 60 degrees. Lift and remove the knob.
8Loosen the switch nut with an open end socket and socket wrench. Remove the nut from the threaded post. Remove the collar and spacer.
9Remove the left and right inner fairing cap screws with a Torx driver. Pull the switch position plate tabs from the slots in the inner fairing cap. Turn the handlebars all the way left and disconnect the fairing cap switch connector by pushing the button on the plug side of the connector to pull apart the pin and the socket halves of the connector.
10Remove the fairing cap from the motorcycle by hand. Slide the ignition switch connector off the anchor on the bottom of the radio and pull the socket and pin halves of the connector apart. Remove the switch housing screws with a Torx driver and lift the switch housing from the upper fork bracket bore and remove the switch housing.
11Slide the base of the replacement ignition switch into the bore of the upper fork bracket. Replace the screws and tighten to 50 inch pounds of torque with a Torx socket and a torque wrench.
12Plug the ignition switch connector back together install that onto the anchor on the bottom of the radio. Plug the fairing cap switch connector back together and install that on the right side of the fairing cap.
13Turn the handlebars all the way left and install the fairing cap over the ignition switch housing. Install the switch position plate fitting tabs in the slots of the fairing cap.
14Reinstall the two fairing cap screws with a Torx driver. Slide first the spacer and then the collar over the ignition switch housing post.
15Replace the nut and tighten to 60 inch pounds of torque with an open end socket and torque wrench. Install the ignition switch knob with the red arrow pointing toward the "access" position. Turn the key clockwise to the "unlock" position then turn the key to "off."
16Tighten the two fairing cap screws to 30 inch pounds of torque with a Torx socket and a torque wrench. Verify the operation of the ignition switch.
17Reinstall the fairing and headlamp assembly. Remove the rags.
Monday, May 19, 2014
How do I Remove the Dipstick From a Blazer Transmission
Checking the transmission fluid level in a Chevy Blazer requires checking the transmission fluid dipstick. The dipstick is located on the passengers side of the engine compartment, near the firewall, at the rear of the engine. The dipstick has a black, plastic, ring-style handle, which is marked.
Instructions
- 1
Open the hood of the Chevy Blazer, and support it with the prop rod, which is located on the drivers side of the hood.
2Locate the transmission dipstick. It is on the drivers side, at the rear of the engine. The handle is marked and sits very close to the firewall of the truck.
3Wipe the dipstick handle with a clean rag. Grasp the ring on the top of the dipstick with one hand, and pull the up dipstick.
4Wrap the rag around the dipstick blade, and slide the dipstick out of the tube, wiping off the transmission fluid. Continuing pulling until the entire dipstick blade clears the tube.
Sunday, May 18, 2014
How to Remove a Fuel Injector from a Ford Diesel Engine
A fuel injector delivers fuel to engine cylinders in a specific sequence. Modern fuel injectors are typically electronically controlled, but older engines used mechanical fuel injection. For example, the large diesel engines in heavy Ford trucks made from 1987 to 1996 used mechanical injection. Removing the injectors in these vehicle also requires you clean the injection system due to the deposits left by diesel fuel.
Instructions
- 1
Clean the nozzle of each fuel injector and the surrounding area with clean engine oil to keep debris out of the engine when you remove the injectors. Clean the connections for the fuel lines on the injectors. Blow the injectors dry with an air compressor.
2Release the retaining clamps for the fuel lines on the injectors. Detach the high-pressure fuel lines and the leak-off tees from the injectors. Push the fuel lines out of the way. Cover the open fuel lines with caps to keep debris out of the fuel system.
3Turn the injectors counterclockwise with a socket wrench to loosen them from the engine. Pull the injectors from the engine with the washer still attached. Cover the injector nozzles and fuel openings with plastic caps to prevent fuel contamination.
4Store the injectors in numbered holders as you remove them. This allows you to replace the injectors into their correct cylinder.
How to Replace the Front Left Turning Bulb in a 1997 Dodge Caravan

Chrysler Corporation began designs for a minivan in the 1970s. The Dodge Caravan debuted in 1984 along side its sister vehicles, the Chrysler Town & Country and the Plymouth Voyager. The 1997 Dodge Caravan was produced in eight different sub-model packages. The turn signal bulb on the 1997 Caravans are all located, accessed and replaced in the same manner, regardless of the sub-model designation. Removal and replacement of the bulbs requires some mechanical skills. Replacement of the 1997 Caravan turn signal bulbs should take about one hour, depending upon individual skills.
Instructions
- 1
Open the hood of the Caravan. Visually inspect and locate the two headlamp mounting bolts at the top rear of the headlamp assembly. Remove the headlamp mounting bolts, using a 3/8-inch drive ratchet and socket with a 6-inch extension -- the addition of an extension between the ratchet and socket will allow you to turn the ratchet completely around while you simply hold the extension and socket in place.
2Pull the headlamp assembly forward and rest the assembly on the front bumper of the Caravan. Reach behind the assembly to access the outermost bulb socket assembly. Remove the bulb socket from the bulb by prying up the small tabs with your fingers or with a small flat-head screwdriver. Rotate the bulb locking cap on the back of the headlamp assembly counterclockwise in relation to its position. Slide the cap back and off the turn signal bulb. Pull the turn signal bulb out of the headlamp assembly and discard it into a trash receptacle.
3Grab a new turn signal bulb from its packaging, using a paper towel or napkin between your fingers and the bulb. Never touch a turn signal bulb directly with your fingers, as the oil from your fingers can cause the bulb to burn out prematurely; the turn signal bulbs also act as running lights on the Caravan, so they heat up similar to headlamps. Insert the new bulb into the rear of the headlamp assembly.
4Install the locking cap over the light bulb and turn it clockwise until it is snug on the rear of the headlamp. Plug the bulb socket into the new light bulb. Reinstall the headlamp assembly back into position on the Caravan. Install the mounting bolts downward through the assembly and begin threading them, by hand, to assure correct threading of the bolts. Tighten the bolts with your 3/8-ratchet, socket and extension assembly until the bolts are snug. Turn the ratchet 1/4-turn farther to secure the headlamp bolts. No torque is needed for the headlamp mounting bolts.
5Repeat the processes in Step 1 through Step 4 to complete the turn signal bulb replacement on the second side of the Caravan. Turn the key to the accessories or "II" position in the ignition of the Caravan after you have completely installed both turn signal bulbs. Turn the left turn signal on and visually inspect its correct operation by either stepping out of the vehicle or checking the bulbs flash lecting off another surface. Turn the right hand turn signal on and inspect its correct operation in a similar fashion. Lower the hood after the operation inspection is completed.
Saturday, May 17, 2014
Transmission Rebuild Guide

When a transmission begins to show signs of trouble, such as slipping, the problem can often be resolved with a fix as simple as adding the proper amount of transmission fluid. However, other issues could result in the need for a total transmission rebuild.
Rebuild Shop
Finding an auto shop willing to rebuild your transmission may take a diligent search on your part. Many shops use to rebuild transmissions, as they can get paid more to replace them instead. Also, the shop will need to know how to rebuild your specific type of transmission.
Rebuild Cost
The cost to have a transmission rebuilt depends on several factors. A general rule is that the rebuild job will cost about half the price of what your transmission cost when it was new. So if your transmission cost $3000 new, you can expect to pay around $1,500 to have it rebuilt.
Rebuild Labor
Once removed from the vehicle, the transmission will need to be completely disassembled. Individual parts are then checked thoroughly. Some only require cleaning, while others are replaced. Seals and gaskets are always replaced in transmission rebuild jobs.
Diesel Ford 350 Ford Recalls

The Ford 350 diesel has been recalled for many problems over the years including a massive 1.1 million truck recall in 2008 for engine camshaft problems. The recalls for the Ford 350 diesel have dealt with everything from battery problems to transmission problems, but none of these recalls were widespread.
Camshaft Sensor Recall
The 2007 Ford 350 diesel saw a major recall for defective camshaft sensor located on the engine of the truck. According to Lemonauto.com, more than 1.1 million Fords were recalled for this sensor problem. The camshaft sensor was working only part of the time and the other part was not working at all, causing the 350 diesel to stall during operation. This Ford 350 problem could create accident situations and theore needed to be recalled for the dealership to inspect the 350 diesel to ensure the camshaft sensor was working properly.
Battery Cable Recall
The Ford 350 diesel saw a recall on just over 1,000 trucks because of a battery cable problem. This 2008 recall was because a battery cable on the positive side of the battery did not have enough clearance from the splash shield bolt. The battery cable was making contact with the bolt causing the cable insulation to burn off, which would short circuit the cable or create a fire hazard. The cable could also damage the battery, starter or starter solenoid because of the short circuit.
Control Module Recall
The 6.4L diesel 350 Ford was recalled in 2008 because of control module problems with the heavy duty trucks. The diesel filter was running at higher temperature than was safe to operate the Ford 350. This higher temperature would cause the 350 diesel engine to run roughly or cause the truck to loose power during operation. The higher temperatures in this diesel filter also caused a build-up of hydrocarbons throughout the exhaust system and white smoke would blow through the exhaust. Flames would also blow out the exhaust system. More than 33,000 Ford 350 diesel trucks needed the control module in the power train or transmission reprogrammed at the dealership.
Friday, May 16, 2014
How to Remove an Astro 4 3 Engine
Removing the 4.3L engine from an Astro van is a challenging project that should only be attempted by an experienced home mechanic with a capable helper. Find a firm level surface that will support the van on stands and allow the engine hoist to roll easily. Safety should be your first concern. Never place any part of your body under the vehicle or engine that is supported by only a hoist or jack and always use a solid support stand.
Instructions
- 1
Disconnect the negative battery cable with a wrench. Drain the coolant into a container for re-use or recycling. Remove the engine cover from inside the vehicle by removing the screws under the hood, the dash lower extension and support rods then releasing the two latches.
2Remove the hood, grille, headlights, radiator support braces, horn, hood latch mechanism and anything else that will prevent the removal of the radiator and ultimately the engine from being pulled through the grille opening. This includes the radiator and shrouds, air conditioning condenser and air cleaner. Disconnect the radiator hoses and remove the radiator with its supports and shroud.
3Disconnect the fuel lines. The V6 engine has constant bleed so no special procedure is necessary to relieve the pressure. Be prepared to clean up any spilled fuel. If not already done, disconnect the transmission cooler lines and clean up any spilled fluid. Label and disconnect all vacuum lines and wiring connections. Disconnect the throttle, cruise control and any other cables from the engine.
4Remove the power steering pump, leaving the hoses connected. Remove the air conditioning compressor. Use rope or wire to support it if necessary. Do not disconnect any part of the air conditioning system; simply lay the components aside. Remove the transmission dipstick if so equipped.
5Raise the van with a floor jack and support it on jack stands. From under the vehicle, disconnect the exhaust manifolds from the exhaust pipe, remove the bell housing cover, bell housing bolts and the starter motor. Unbolt the torque converter from the flex plate and the strut rods. Remove the engine mount bolts and nuts. Support the front of the transmission with the floor jack.
6Attach an engine hoist to the lift plates on the engine, then lift the engine a little and pull it forward slightly. If necessary, have a helper separate the torque converter from the engine with a large screwdriver or pry bar. Be sure the helper is out of the way before proceeding. Continue pulling and lifting until the engine is clear of the vehicle. Gently set the engine on wood blocks or an engine stand.
GMC Truck Steering Problems

General Motors Company and the National Highway Traffic System Administration have announced multiple safety recalls due to steering problems in GMC trucks. Sierra pickups with model years of 2003-2006 may experience difficulty steering due to a range of manufacturing defects. If not repaired, any of these steering problems could lead to a crash.
Power Steering Hose Defect
On October 4, 2005, General Motors recalled 123,592 vehicles including certain 2005-2006 model year Sierra pickup trucks for problems with the power steering hose. A manufacturing defect may cause the hose to break and leak fluid if the steering wheel is turned extremely to the left or right while braking.
Steering Connector Bolt Defect
On January 20, 2005, General Motors recalled certain 2005 model year GMC Sierra trucks to replace the bolt connecting the steering gear to the steering shaft. If not repaired, the defective bolt may break and cause a loss of steering.
Hydraulic Brake System Defects
In January 2004 and February 2005, General Motors recalled certain 2003-2005 Sierra pickups for manufacturing issues that could result in steering problems. A defect in the hydro-boost relief valve in 2003-2004 GMC Sierra trucks may cause the driver to have to use excessive force to steer and/or brake. A potentially problematic hydro-boost assembly in 2004-2005 GMC Sierra trucks may cause an hydraulic fuel leak, which may lead the driver to experience steering and brake problems.
Thursday, May 15, 2014
How to Change a Battery in a Nissan Versa

The Nissan Versa battery mounts near the rear of the engine compartment on the driver side. You need to replace the battery right away if it loses its charge. Buy a replacement battery at a Nissan dealer or auto parts store. Save the time and money spent at a service center by changing the battery yourself. Many auto parts stores and dealerships will accept old batteries for recycling.
Instructions
- 1
Park your Versa on level ground and remove the key from the ignition. Open and secure the hood of the Versa.
2Loosen the battery terminal connection on the negative battery post with a wrench. Remove the cable. Follow the same procedure to remove the positive battery cable.
3Lift the retaining strap off the top of the battery. Pull the batterys bottom tab to lift the strap up, then move the strap out of the way. Remove the battery.
4Insert the new battery into the compartment. Replace the retaining strap and snap it into place. Connect the positive battery cable. Tighten it with a wrench. Attach the negative cable. Tighten the connection with the wrench. Close the hood.
The Differences Between Two Four Barrel Intake Manifolds
Multi-barrel intake manifolds can accommodate two- or four-barrel carburetors on older or performance engines. The intake manifolds job is to connect the carburetor to the intake ports on the engines cylinder heads. Intake manifolds can improve your vehicles performance and increase fuel mileage. It is fairly common for customized carburetor performance engines to feature an upgraded intake manifold designed to increase overall horsepower.
Increased Airflow
The four-barrel carburetor and corresponding four-barrel intake manifold allow increased fuel and air flow through the engine. You will commonly find four-barrel manifolds on large V8 engines that are intended for performance and power where the extra airflow can be turned into improved performance.
Fuel Economy
Four-barrel carburetors work by running the two primary barrels all of the time and only going into the secondary barrels when the driver signals the engine to provide additional power by pressing down hard on the accelerator. When the two secondary barrels open, more fuel and air flow through the intake manifolds and into the engine. Two-barrel carburetors do not have this option; theore they typically get better fuel economy than four-barrels due to the restricted fuel and air flow.
Improved Performance
The increased air and fuel flow from a four-barrel carburetor, in addition to the two extra secondary barrels, create increased horsepower and acceleration when you drive the vehicle. The vehicle receives more fuel, which it can burn to provide additional power when driven. Vehicles with a four-barrel carburetor and intake manifold will accelerate more rapidly and efficiently than a vehicle with a two-barrel carburetor and intake.
Wednesday, May 14, 2014
How to Remove Rounded Wheel Bolts From a Ford Aspire

Wheel bolts, or lug nuts, are the nuts that hold the wheel to the axle of your vehicle. A Ford Aspire has one of the smaller patterns, consisting of only four bolts. The bolts are welded to the hub. The wheel slips over the bolts and the lug nuts are then used to tighten the wheel to the hub. If you are not caul, you can round the corners off of the lug nuts. If this happens, they become stuck. You can use the alligator-like jaws of locking pliers to free them.
Instructions
- 1
Insert the flat tip of a tire iron into the crack between the hubcap and the wheel. Wiggle it until it penetrates 1/2-inch. Pry on the tire iron to pop the hubcap off the wheel.
2Spray the wheel bolts liberally with spray lubricant. Coat the entire bolt and nut until the lubricant is dripping off. Wait one hour for the lubricant to penetrate.
3Open the jaws of the locking pliers. Slip them over the lug nut. The handle of the pliers should be pointing horizontally to the left. Squeeze the handle. If the handle closes too easily, turn the bolt on the end of the locking pliers clockwise and close the jaws again. You should be able to just barely close the jaws on the rounded nut.
4Press the handles of the pliers together with both hands. Using all of your weight, force the handles toward the ground. You should be turning the bolt counterclockwise.
5Bounce your weight on the nut until it breaks loose. If it wont break loose, use a hammer to smack the end of the handles of the pliers until the lug nut breaks loose. Finish unscrewing the bolt with your fingers, or spin the bolt with the pliers if the bolt is stubborn.