Thursday, October 31, 2013
How to Replace the Taillight Bulb for a 2005 Toyota Tacoma

Replacing the taillight bulbs on the Toyota Tacoma pickup is a simple project to undertake in the driveway or garage at home. The Tacomas taillight bulbs sit in plastic assemblies; you can reach a bulb only by removing the corresponding taillight assembly from the truck. There are two bolts that hold each taillight assembly in place, and there are two stubborn pins on the back of the assembly that snap into clips on the outboard edge of the taillight. The entire process will take about 10 minutes; it requires only basic hand tools to complete.
Instructions
- 1
Open the tailgate of your Tacoma and locate the two 10mm bolts that secure the taillight assembly through the side of the cargo bed. There are several bolts in there; you want to unscrew the ones that dont have a washer under them.
2Remove the retaining bolts with a 10mm socket and ratchet, then grasp the taillight assembly with both hands and pull it straight back. It will not come off easily, but it will come off.
3Locate the three bulb sockets on the back of the taillight assembly; the center one is the taillight/brake-light bulb. Turn the socket counterclockwise then pull it straight out of the assembly. Pull the bulb out of the socket and discard it.
4Push a new bulb into the socket. Make sure it is secure. Install the socket into the rear of the taillight assembly. Turn it clockwise to lock it in place, then slide the assembly back onto the rear of the truck, pushing it in until the retaining pins on the assembly snap in to the body and the screw holes align with the holes in the truck body.
5Install the two retaining bolts and tighten them with a socket and ratchet. Do not over-tighten the bolts or you will crack the plastic taillight assembly. Close the tailgate.
What Causes Fish Eyes in Car Paint

The term "fish eye" refers to a tiny crater that can form on a cars paint job during or after the car is repainted. Several substances can cause fish eye, but the main way to avoid these craters from forming on your cars finish is to be sure to clean your car thoroughly before painting it. Protect the car during the painting process, and ensure that nothing gets onto the paint. There are also additives for car paint, but these can cause other problems.
Skin Oil
Reduce the risk of contaminating your cars paint job with skin oil by washing your hands or wearing latex gloves. Even brushing up against the cars paint with your arm can transfer enough skin oil to cause fish eyes to form when you spray the next layer of paint onto the car.
Tool Oil
Oil and lubricants from sanders or other tools you use on your car between layers of paint poses the same risk as skin oils. Clean your car thoroughly between coats of paint and maintain your power tools regularly to ensure they do not leak fluids onto your fresh paint.
Engine and Road Fluids
Just as with other types of oily liquids, engine fluids and oil from roads can cause fish eyes to form on your cars paint if you do not remove the fluids properly before painting your car. Clean your car thoroughly before painting it and do not run the engine until you have completed all of the painting.
Silicone
Silicone is found in car waxes and some cleaning products. Silicone is a slippery fluid that mimics oil if it gets onto your paint job before you paint the next layer. You can remove silicone with the same products that clean other oily substances from the car.
How Exhaust Baffles Work
Exhaust Baffle
The exhaust baffle is a chamber inside a muffler or resonator that is designed to muffle or silence the otherwise loud exhaust system. Ingeniously, the muffler uses the baffle chamber to increase the amount of internal sound inside the chamber so by the time it exits the muffler, the sound cancels itself out. Exhaust is spent fuel and air of an internal combustion engine and is extremely loud coming from the cylinders of the engine. An exhaust system controls the sound through a manifold and a series of pipes, a catalytic converter (on vehicles) and the muffler. In some applications, resonators are present in the exhaust pipes that act as a second (or more) muffler on the system. Inside the muffler or resonator is a sealed chamber with two or more perforated tubes. The inlet perforated tube allows the exhaust to emit into the baffle chamber, bounce off the interior walls and enter into the outlet perforated tube where it is then directed by back pressure through the tailpipe of the muffler. The perforated tubes in the baffle chamber create a nondirectional interference with the flow of the back pressured exhaust and assist in silencing the exhaust.
Perforated Tubes
There are adjustable or do-it-yourself baffle kits that can be manipulated and inserted into the exhaust system muffler (most common on motorcycle mufflers) to change the pitch of an exhaust to either intensify or decrease the amount of sound the exhaust system emits. By doing so, these baffles can increase the horsepower of the engine (for racing), which subsequently decreases the fuel efficiency of the vehicle. Conversely, a quieter, more controlled sound can be achieved.
Wear and Tear
After time, wear and tear and exposure, exhaust systems deteriorate. Due to condensation of heating and cooling, muffler and internal baffles can fail internally. Even if the muffler is not leaking, a deteriorated perforated tube in the baffled chamber of a muffler can create an annoying rattle during normal operation of the vehicle. Damage to the tube in the baffled chamber would require the replacement of the muffler and or attaching new pipes to restore the system.
How to Install an Alternator on a Jetta TDI
The alternator in a Jetta TDI uses the energy created by the vehicles running engine to continuously recharge the battery. As the alternator starts to die, a red light shaped like a battery will glow on the instrument panel and the battery will have to pick up the slack and work harder. Replace the alternator in a timely fashion to prevent larger problems from occurring with the Jetta.
Instructions
- 1
Park the Jetta TDI on a flat, level surface and set the parking brake. Place wheel chocks around one of the wheels. Open the hood and support it in place with the hood prop. Disconnect the negative battery cable with an open-ended wrench.
2Remove the engine cover screws with a Phillips head screwdriver. Loosen the hose clamp on the end of the intake hose with a flat head screwdriver. Disconnect the intake hose and remove the engine cover from the vehicle.
3Release the tension on the alternator belt by using a socket wrench on the belt tensioner. Push the handle of the socket wrench behind the belt tensioner. Pull forward on the socket wrench so that it will act as a lever against the tensioner and move it forward. Remove the belt from the pulley.
4Unplug the electrical connections from the alternator. Remove the alternator mounting bolts with a socket wrench and a 13mm socket. Remove the alternator.
5Put the new alternator in position and secure the mounting bolts with a socket wrench. Push on the belt tensioner with a socket wrench and place the alternator belt on the pulley. Release the tension on the belt tensioner and let it settle in place.
6Replace the engine cover and tighten the screws with a Phillips head screwdriver. Seat the intake hose and tighten the hose clamp around the connection with a flat head screwdriver.
Wednesday, October 30, 2013
How to Free Seized Nuts Bolts

Old nuts and bolts are prone to rust and often become seized if an anti-seize compound was not used during the initial installation. The extent of this problem can range from mild annoyance to outright ordeal. Fortunately, there are several options available to release the seized hardware. Each requires different materials and hardware. Depending on the situation, all of the methods may not be viable. Start with the least intrusive and work up to the more involved steps.
Instructions
- 1
Add penetrating oil to the seized hardware and allow several hours for the oil to begin working before trying to loosen the nut. Several applications may be required before results are seen. If the bolt is small enough, submerging it in oil can be effective too.
2Use an acetylene torch to heat the hardware before attempting to loosen it. This makes the metal expand and can break the bond between the nut and bolt caused by corrosion.
3Use a nut splitter to break the nut off of the bolt. This tool uses a wrench to tighten a sharp blade against the side of the nut causing it to split.
4Drill the bolt out, but only as a last resort. Mark the center of the bolt and starting with the smallest drill bit possible, make a hole. Use progressively larger bits until the bolt falls apart.
How to Fix the Exhaust Manifold
When an engines spark plug ignites the air/fuel mixture within the cylinder, the mixture explodes and pushes the piston downward. Once the engine reaches its lowest point within the cylinder, the exhaust valve in the cylinder head opens. As the piston then travels upwards, it pushes the gases which remain from the explosion through the open exhaust valve and ultimately out of the engine. These noxious gases are commonly referred to as "exhaust," and can prove to be deadly if you are exposed to the gases for a long period of time. For this reason, the exhaust gases are routed through exhaust manifolds, which in turn carry the gases to the exhaust pipes. Between the exhaust manifold and the engine is a gasket designed to prevent the gases from escaping before they reach the exhaust manifold and entering the interior of the vehicle. If this gasket becomes damaged, it needs to be replaced.
Instructions
- 1
Ensure that the exhaust manifold is cool by allowing the engine to sit without running for at least two hours. Exhaust manifolds can get extremely hot as the exhaust gases flow through them, and can therefore pose a serious burn hazard.
2Remove the bolts that hold the manifold to the cylinder head with a wrench. Exhaust manifold designs differ, but most exhaust manifolds have one bolt on both sides of each pipe.
3Pull the exhaust manifold away from the cylinder head just enough to expose the manifolds gasket. A stubborn manifold can be freed from the cylinder head by tapping the manifold with a rubber mallet, sometimes referred to as a "dead blow" hammer. The mallets rubber composition prevents the hammer from denting the manifold. Note that the manifold need not be removed from the engine compartment, which would require the manifold to be disconnected from the exhaust pipe. The manifold must only be pulled away from the cylinder head to access the manifolds gasket.
4Remove the old exhaust manifold gasket. The gasket will either stick to the cylinder head or to the manifold itself. The gasket can usually be peeled away, but a stubborn or burnt gasket may have to be scraped away with either a flathead screwdriver or a gasket scraper.
5Place a new exhaust manifold gasket against the manifold, then press the manifold against the cylinder head. Hold the manifold against the cylinder head with one hand, then insert the manifolds retaining bolts through the manifold and into the cylinder head with the other hand. Do not apply gasket sealer onto this gasket.
6Tighten each of the manifolds retaining bolts in small increments with a wrench until each bolt is tight to complete the repair. Tightening the bolts in small increments is necessary to ensure that the gasket seats properly and does not warp.
Moped Tools

Moped is the term for a type of low-powered, economical motorcycle. Moped is short for motor-pedal because all mopeds used to come equipped with pedals similar to a bicycle. Now the term is frequently applied to scooters even without pedals. There are various tools available made for moped maintenance and repair.
Tire Irons
Getting a flat or needing a new tire is inevitable. At some point, any moped owner will need a tire iron to change tires. Tire irons are generally made of steel and designed specifically so the bike doesnt get damaged during the changing process.
Flywheel Puller
These are used to replace the points and condenser on moped engines. A flywheel puller will allow you to remove the magneto flywheel without causing damage to the engine case or crank shaft. Its best to use a puller designed for your brand of moped.
Tire Pressure Gauge
If you dont properly maintain your tire pressure, you can experience a range of problems, including poor fuel consumption, tire failure, loss of control and faster tire wear. You can keep track of, and maintain, proper tire pressure with a tire pressure gauge.
Spark Plug Wrench
Over time, spark plugs will need to be replaced. You can use a spark plug wrench to remove your mopeds worn-out spark plugs and install new ones. Spark plug wrenches are generally made of steel.
Allen Wrenches
Allen wrenches are sometimes called Allen keys, hex keys or hex wrenches. They are used to drive screws and bolts with a hexagonal head socket. Allen screws and bolts are common on mopeds, and frequently youll find an Allen wrench set in moped tool kits.
How to Look Up Parts by VIN

Every manufactured vehicle has a vehicle identification number (VIN), which provides the owner with information regarding the vehicles origins and source engine components. In the mid-1950s, as mass auto production escalated with demand, Detroit auto manufacturers began stamping their vehicles to identify them. Early identification numbers varied by manufacturer, but in 1977 an ISO (International Organization of Standardization) for the VIN came into effect, which the U.S. National Highway Traffic Safety Administration adopted in the early 1980s as a requirement for all licensed vehicles. For the car-repair enthusiast, interpreting the VIN properly will ensure the right parts for the vehicle.
Instructions
Looking up parts by VIN
- 1
Locate your vehicle identification number. The most common location for the VIN is on the door frame or post of the front driver-side door, or on the dashboard close to the windshield. The VIN can be in other places though, such as the machine pad on the engine, or stamped on the steering wheel or column. The VIN is also listed on vehicle documents such as the title certificate, registration, warranty or maintenance books.
2Decipher your VIN. The first character in a VIN denotes the country of origin, the second character is the manufacturer and the third character identifies the vehicle type (or division). The fourth through eighth characters are very important from a parts perspective as they identify model attributes such as body style, engine type and model series. The ninth digit is the check digit (mathematically determined to verify VIN accuracy), and the 10th and 11th characters identify the model year and manufacturing plant. The last six digits are the unique identifiers for each vehicle.
3Apply the VIN information to a part source. This process has benefited greatly from the digital age, and many parts retailers and manufacturers list their supply catalogs online. On their websites you will also have the ability to search their databases by VIN. If sourcing through the computer doesnt sound appealing, both dealership service centers and retail parts outlets have the ability to find the parts you need through your VIN.
Tuesday, October 29, 2013
How to Install Oxygen Sensors on a 1998 Mercury Mountaineer
The oxygen sensors in the exhaust system of your 1998 Mercury Mountaineer help the fuel system regulate the amount of fuel burned by the engine. If the oxygen sensors fail, you may notice a drastic decrease in the fuel mileage of your truck. The 1998 Mountaineer is equipped with four oxygen sensors. There is a sensor on each side of both catalytic converters. Buy replacement sensors from an auto parts retailer.
Instructions
- 1
Lift the truck with a jack to support it with jack stands. Locate the oxygen sensors on each side of the dual catalytic converters in the exhaust system.
2Disconnect the wiring harness at the top of the oxygen sensor. You can pull the connector apart by hand. Remove the oxygen sensor with an oxygen sensor socket and ratchet.
3Thread the new sensor into place by hand to prevent cross threading. Torque the sensor to 30 pound-feet with your torque wrench. Connect the wiring harness by pressing the electrical connection together.
4Repeat the process for the remaining sensors you want to change. Raise the truck slightly and remove the jack stands. Lower the truck to the ground.
What is a Driveshaft
A driveshaft is one of the most basic parts of an automobile. No matter the age of your vehicle, if it is not a front-wheel drive, it probably has at least one driveshaft.
Driveshaft Basics
The ultimate purpose of the driveshaft is to transmit power from the engine to the wheels. It is part of a system called the drive train. Power goes from the engine to the transmission.
Rear Wheel Drive
In both rear wheel drive and 4-wheel drive vehicles, the driveshaft is connected to the transmission and carries power to the rear differential, where it is transferred to the rear axle to which the wheels are attached.
Four Wheel Drive
In a 4-wheel drive vehicle you have the rear drive shaft and also a transfer case and front driveshaft. Both driveshafts are connected to the transfer case. The transfer case gets its power from the transmission. The front driveshaft connects to the front differential, putting power to the front wheels when needed.
Oil Gauge Problems

Oil pressure gauges are prone to common problems resulting from regular wear and tear. Its important to make sure the gauge is working. Oil pressure that is too high or low can lead to leaks and engine problems.
Gauge Doesnt Move
Its normal for the oil pressure gauge to remain still while the engine is idling. Try revving the engine. If the gauge doesnt move, it needs to be replaced.
Gauge Fluctuates
While it is common for the gauge to move, it should not fluctuate wildly. If it does this, the gauge has likely gone bad. The 2CarPros website states this is the result of a broken oil pressure sender.
Gauge Too Low
The gauge should give higher readings when gas is applied and the car is moving. It is usually a sign of problems when the gauge stays low.
Gauge Too High
The calibration of oil pressure gauges can be incorrect. The gauge should not show high pressure when the engine is idling or shut off.
How to Stop Engine Coolant From Leaking
Leaks in a cars cooling system can have dangerous consequences for a car and can leave you stranded. In most cases coolant leaks can be visually diagnosed by opening the hood of the car and visually inspecting the cars hoses and cooling system. If you are lucky it will be possible to do a quick and temporary fix that will allow you to get your car to mechanic for a professional repair job. The essential thing to remember is not to drive car when the coolant level is dangerously low.
Instructions
- 1
Inspect the coolant level on a regular basis. The most obvious signs of a coolant leak is low levels of coolant in the coolant reservoir. Other signs include colored puddles under the car, and burning smell when the coolant drips on a hot engine. The worse case scenario is white smoke coming out of the exhaust system. This indicates that you have a head gasket problem.
2Examine all of the hoses on the radiator and coolant reservoir. If the hose has a pinhole sized leak it is sometimes possible to see the coolant dripping from the hose. Other signs of bad hoses included blisters and bulges, soft spots, hardening, and cracks. Perform a quick fix by cleaning the hose with a rag and wrapping the damaged area tightly with duct tape. This is only a temporary fix. Replace all damaged hoses with new hoses.
3Check the coolant reservoir for cracks and holes. Coolant reservoirs are made from plastic and can be easily cracked. If the coolant reservoir has a crack allow the car to cool down. Remove the reservoir. Thoroughly wash and clean it. Patch the crack with a plastic welding material or epoxy. Allow the patching material to dry and replace the coolant reservoir.
4Inspect the radiator for signs of coolant leaking. The radiator itself is prone to damage from stones and road debris and from general aging. Pinhole sized leaks in the radiator can be temporarily repaired with a radiator sealant product such as Alum-A-Seal or Bars Leak. These products and similar products are available at auto parts stores. Allow the engine to cool down. Remove the radiator cap and empty the contents of the sealant into the radiator. Run the engine for fifteen to twenty minutes. Radiator sealant works well for pinhole sized leaks and smaller holes as well, however, this is a temporary fix. Take the care to the mechanic and have the radiator professionally repaired.
5Take a close look at the water pump. The gasket and O-seal on the water pump are another possible source of coolant leakage. Look for signs of discoloration and liquid coolant on the outside of the water pump. Replace the water pump if it is the source of the problem.
6Take your car to the mechanic if you are unable to diagnose the problem. If the coolant reservoir is continually reading at a low level and you cannot locate the source of the problem, then there is an internal leak somewhere in the cooling system that requires professional attention.
How to Test a Car Battery Charger

Car batteries work when the chemical reactions in the battery cause electrons to gather at the negative terminal. Turning the key into the "on" position connects a circuit between the negative and positive terminal, causing the electrons to rush from the negative terminal to the positive, providing the spark necessary to power the starter engine and turn the car over. When a car battery dies, it means there is a shortage of electrons gathering at the negative terminal. Car battery chargers work by reversing the flow of electrons from the positive terminal to the negative terminal, eventually causing enough electrons to gather at the negative terminal for a quick current to run from the negative terminal to the positive terminal when the circuit is connected. Testing the effectiveness of a car battery charger requires a field experiment whereby you connect the charger to a dead or dying battery and turning it on.
Instructions
- 1
Clean the terminals of your battery sufficiently with a clean cloth.
2Connect the alligator clips of your charger to the terminals of your battery. Connect the negative (black) alligator clip of your charger to the negative terminal of your battery before connecting the positive (red) alligator clip.
3Plug your battery charger into a wall socket if it is DC/outlet powered, or turn it on if it is AC battery powered.
4Wait two to three minutes or the specified amount of time indicated in the operators manual that came with your specific battery charger. For most car battery chargers, two to three minutes is sufficient to check whether the charger itself is functional, as it will likely charge the battery enough to turn your car over.
Monday, October 28, 2013
How to Replace Fuel Injectors in 1ZZ FE
The 1ZZ-FE is a four-cylinder 1.8-liter engine that is most common on Toyota vehicles made from 1999 to 2005. This engine uses sequential fuel injection, which requires the fuel injectors to deliver fuel to the engine under high pressure. The fuel injectors for a 1ZZ-FE engine are on top of the engine, and are accessible from the engine compartment. The replacement of the fuel injectors in this engine requires the removal of additional engine components.
Instructions
- 1
Remove the fuel pump fuse from the fuse box under the dashboard. Start the engine and allow the engine to stall. Crank the engine to ensure the fuel lines are empty and replace the fuel pump fuse. Disconnect the cable from the negative battery terminal to prevent the battery from generating sparks during the fuel injector replacement.
2Disconnect the cover for the No. 2 cylinder head with a socket wrench. Detach the vacuum hose and fuel tube from the fuel pipe. Disconnect the electrical connectors from the fuel injectors.
3Disconnect the fuel pipe from the fuel injectors and detach the fuel injectors from the engine. Remove the spacers from the cylinder head and pull the fuel injectors away from the fuel pipe. Discard the O-ring and grommet for the fuel injectors.
4Coat the new O-rings and grommets with light machine oil before installing them onto the new fuel injectors. Coat the mounting surfaces on the fuel pipe with light machine oil. Install the new fuel injectors into the fuel pipe by twisting them into place so that the electrical connectors face away from the fuel pipe. Coat the injector bores in the cylinder head with light machine oil.
5Install the spacers and connect the fuel pipe to the cylinder heads. Tighten the mounting bolts for the fuel pipe to 14 foot-pounds with a torque wrench. Attach the fuel line and the PCV hose to the fuel pipe. Connect the cover for the No. 2 cylinder head and tighten its mounting bolts to 7 foot-pounds. Connect the cable for the negative battery terminal with a socket wrench.
Types of Welding Gases
Welding is the process of heating metal to create a permanent joint between the pieces. The three most common welding techniques are MIG (Metal Inert Gas) welding, arc welding and TIG (Tungsten Inert Gas) welding. Each welding technique uses inert gases to shield the welding flame from contacting reactive gases, thereby creating a cleaner and stronger weld. Arc welding utilizes a solid substance called flux that burns and gives off the inert gas. MIG and TIG welding requires gas to be fed from a compressed air bottle through the welding gun in order to protect the welding flame.
Inert Gases
The most common inert gases used in welding include argon and helium. Because argon is noncorrosive, nontoxic and nonflammable, it serves as an ideal inert shielding gas most frequently used in MIG and TIG welding applications. Helium is more commonly used in arc welding processes because it creates a hotter weld necessary for metals such as copper.
Carbon Dioxide
Carbon dioxide is also used in some welding applications, and even though it is nonflammable and inert under most conditions, it may cause a chemical reaction with some metals while welding. Carbon dioxide is most commonly used as a shielding gas in arc welding.
Welding and Cutting Gas Fuels
In addition to shield gases, welding techniques can also utilize gases as a fuel source for cutting and heating metals. Acetylene, propylene and propane are all flammable gases that are used to fuel welding torches. Additionally, because acetylene gas can be mixed with oxygen to create an oxy-acetylene torch that provides its own fuel and oxygen source, it can be used for underwater welding applications.
OEM Chevy Silverado Replacement Parts

Whether you need to replace a part under the hood or inside the car, you can buy a part that the company original produced or an original equipment manufacturer (OEM) part. You can find Chevrolet Silverado OEM parts in automotive retail stores. Some retailers may not keep OEM parts in stock, so you may have to place an order. Most of the Silverado parts are replaceable from engines, transmissions and cooling systems.
Automatic Transmission
OEM automatic transmissions are available for replacement parts in the Chevrolet Silverado. You can purchase a transmission for a two-wheel drive and four-wheel drive system. Allison 1000 Series and 3500 Series transmissions with either six-speed or four-speed are accessible.
Cooling Systems
OEM parts available for the cooling system include cooling fans, the entire cooling system, radiator and water pump. Fan shroud are available for the 4.3-liter, 4.8-liter, 5.3-liter and 6.2-liter Silverado. In addition, OEM fan blades and fan motors are available for replacement.
Air Intake
Air intake OEM replacement parts are available for the Silverado. Air cleaners are available for diesel- or gas-powered vehicles. Other components that are OEM replacement parts include drain tubes, mount brackets, rear ducts, air mass sensors and outlet ducts.
Front Bumper
You can change the Silverados front bumper and its components. Whether you need a complete bumper, air defector, a lower grille or license brackets, all of the intricate parts of the bumper have OEM replacement parts.
How to Install an S10 Catalytic Converter
The catalytic converters on the Chevy S10 has undergone many changes throughout the years. The older style S10s had the converter installed downstream in the exhaust system and were clamp-connected to the exhaust pipes. The newer S10s have the converters integrated with the front Y-exhaust pipe. In any case, if you have to replace one, the direct-fit option is going to be a much wiser choice as it will save you time and money than trying to cut and weld in the cheaper universal converter choices.
Instructions
- 1
Place the tools and converter in the tool tray and lift the S10 on a vehicle lift safely and securely. Put on the safety glasses inspect the catalytic converter. The inspection of the converter should have already been performed before obtaining the new replacement on the tool cart, but it would be recommended to ensure you have the right replacement part before cutting the old one down.
2Locate the oxygen sensor port(s) in the catalytic converter. If its an older S10, there will be one port located on the inlet pipe of the converter. If its a newer S10, there will be three ports located on each side of the Y-pipe inlets and one more on the rear converter of the pipe. Spray lubricant on the threads of the sensors and allow it to soak in. Unplug the oxygen sensor wire(s) using the screwdriver to help you press in on the clip lock on the plugs. Remove the oxygen sensor(s) using the oxygen sensor socket and the ratchet. Mark the sensors to identify their position if you have the three sensor portholes.
3Put on the cutting glasses and gloves and light the torch. Start at the front of the converter. If its a three-point flange, cut out the nut and bolts. If its the Y-pipe converter, heat up the nuts on the studs (one at a time) with the torch and have your pneumatic gun, long extension, swivel and socket ready to extract the nut once properly heated. This will avoid snapping a manifold stud. Remove all three nuts per side (six in all) in this fashion.
4Cut the three bolts and nuts out of the rear flange (two bolts on the Y-pipe). Be aware that certain year S10s may have welded studs in the rear flange. You can try to reuse these or you could cut them out and replace them with nuts and bolts. Theyll be stubborn to cut out, but unless theyre really clean, it would make an easier fix to replace them. Shut off the torch and switch back to the safety glasses after the converter connections are disconnected.
5Carefully remove the converter. Disengage any rubber hangers from the welded hangers on the converter. Be careful not to burn yourself as the shell of the converter will be hot and can still burn through safety gloves.
6Install the new converter and attach it to the front of the S10 first with the replacement gaskets. It will take some wrangling if its the Y-pipe converter to fit it up. Place the welded hanger in the converter through the rubber hanger to help hold it in place. Place the nuts on the studs to hold the converter. For the three-bolt flange type converter, simply insert the gasket in between the flanges and place the bolts and flat washers on one side of the flange and the lock washers and nuts on the other side.
7Connect the rear converter flange with hardware and the gasket in the same manner -- bolts and flat washers on one side of the flange and lock washers and nuts on the other side. Tighten the flange connections using the gun, with swivel, socket, and any necessary length extension on the nut while holding the bolt head with a box end wrench. Tighten each nut and bolt slightly and alternate between each one to draw them in evenly and then tighten them snug at the end.
8Place a light amount of anti-seize lubricant on the threads of the oxygen sensor(s) and thread them into the portholes by hand. Tighten the sensor(s) snugly with the ratchet and oxygen sensor socket, but be careful not to overtighten and strip the threads of the sensor(s). Plug the sensor(s) wire back into the plug connection.
9Remove the tool tray and debris from under the S10, lower the truck on the lift and start it up before swinging the lift arms free. Make sure there are no exhaust leaks coming from any of the flange connections or oxygen sensor port(s).
Sunday, October 27, 2013
NA Rotary Engine Factory Specs

The rotary engine is a highly unusual and very rare power plant. Its sole application in road legal passenger vehicles is found in Mazdas RX-8 sports car. The compact dimensions and low weight of the engine allow Mazda to keep the RX-8s center of gravity near the ground and weight quite low, making it one of the best handling cars on the road today.
Basic Specs
Rotary engines have radically different designs than conventional motors and use a "rotor" (hence the name) instead of cylinders. The rotor is a triangular, lightweight piece mounted on a circular lobe. The rotor compresses the gas/air mixture simply by rotating on the lobe and therefore does not need pistons, camshafts or rods. Concepts such as bore and stroke do not apply to rotary engines. The capacity of a rotary is defined by the maximum volume it can compress and ignite per cycle, which for Maxdas rotary is 1.3 liters.
The compression ratio is 10:1, with multi-port electronic fuel injection igniting the mixture during the compression stroke. The rotor is housed in an aluminum chamber with chrome-steel liners. Exhaust gasses flow into stainless steel headers, which then connect to a low back pressure main muffler. Transmission options for the engine are a six speed manual or six speed automatic
Power and Torque
In addition to its light weight and compact dimensions, a chief advantage of the rotary engine is its ability to reach very high engine speeds. The Mazda rotarys redline is a stratospheric 9,000 rpm when mated to a manual transmission, and 7,500 rpm when combined with the automatic, as the later transmission is unable to cope with higher speed and torque. Due to the restriction in engine speeds, the maximum power also varies based on the choice of transmission. While the engine makes 232 horsepower at 8,500 rpm with a manual transmission, with the automatic it produces 212 horsepower at 7,500. This difference is solely the result of engine speed restrictions, as evidenced by the fact the the motor produces an identical peak torque of 159 pound-feet at 5,500 rpm regardless of transmission type.
Performance
This fast-spinning engine propels the RX-8 from zero to 60 miles per hour in six seconds flat when paired with the manual and six and a half seconds with the automatic transmission. Fuel economy is relatively poor in either case however, especially considering the 3,000-pound weight of the whole car, which is very light for a four-seater. Both the manual and automatic vehicles achieve 16 miles per gallon in the city. While the manual version gets 22 mpg on the highway; the automatic can squeeze one more mile from each gallon, due to its longer final gear ratio. Although both transmissions feature six forward speeds, the manuals final ratio is 0.79 while the automatics tops at 0.58.
Excess fuel consumption is practically unavoidable with rotarys and is the main reason these engines are not more commonly used in modern automobiles. The unique design not only allows a significant amount of unburnt fuel to escape the combustion process, but also results in a good deal of energy being wasted as heat.
How to Find an F150 Airbag Control Module
A Ford F150s air bag control module is in the trucks Supplemental Restraint Systems central computer. The module governs all the air bags within the truck, and it also interacts with the system for signs of problems. If a problem is sensed with any of the air bags, the SRS warning light will activate on the F150s dashboard. Locating the module is fairly simple; however, the SRS system is complex and most repairs should be deferred to a trained professional.
Instructions
- 1
Ensure the Ford F150 is completely off. Pop the hood and remove the negative cable from the negative post on the F150s battery. Wait five minutes, so that any remaining power within the truck drains out. This is an absolutely necessary precaution. Anytime you work in the vicinity of the dashboard or any air bag components, the SRS system must be disabled. This will keep the air bags from accidental deployment.
2Open the passenger-side door and locate the right kick panel. It will be the the right side of the passengers side leg-space.
3Loosen the right kick panel. Depending on the model and year of F150 truck, you should be able to pry it off with a trim tab or a flat head screwdriver wrapped in tape. There may be retaining clips behind the panel. In order to avoid any damage to the panel, lever it off slowly. If you meet any signs of resistance, stop and investigate the obstruction.
4Remove the right kick panel. The air bag control modue will be behind it.
How to Release the Hood on a 2001 Dodge Intrepid If the Cable Is Broken
Dealing with a broken hood latch cable can be extremely frustrating, especially if you need to access the engine compartment to jump start the vehicle, add fluids or perform a repair. The hood latch cable runs from the hood latch down the inside of the fender, and through the firewall to the hood latch release lever. In order to replace the cable, youll first need to gain access to the engine compartment. In this situation, you can manually actuate the hood latch mechanism from underneath the vehicle.
Instructions
- 1
Shut off the engine and pull the parking brake lever to engage the brake. Place wheel chocks behind the rear wheels.
2Raise the drivers side of the vehicle near the wheel with a jack, and then place a jack stand underneath the frame. Raise the passenger side of the vehicle near the wheel and place a jack stand underneath the frame. Check both stands to make sure they are secure.
3Move underneath the vehicle on a mechanics creeper and locate the hood latch with a work light. Its above the front radiator fans, on top of the radiator core support.
4Locate the hood latch cable where it terminates at the cable release lever. There is a small crimped steel ball on the end of the cable that threads through the cable release lever.
5Pry on the release lever with a large flat-head screwdriver in the direction of the cable to open the hood. This forces the lever toward the cable, the same way it would move if it was being pulled by the cable.
How to Remove a CV Carburetor

The CV, for constant velocity, carburetor was standard equipment on Harley-Davidson motorcycles until 2007, when Harley began delivering all bikes with electronic fuel injection. It has also been standard on Kawasakis and BMWs. It is often called a Keihin carb because it was originally manufactured by that Japanese carburetor maker, although it is a British invention. The CV has a vacuum-operated slide that changes the size of the venturi, the big air hole, in the carburetor to make a constant air velocity. In general, it comes off all bikes as it comes off a carbureted Harley.
Instructions
- 1
Start the motorcycle with the petcock closed and run the motorcycle until the carburetor runs out of fuel. Unclip the choke knob from its attachment just in front of the riders left thigh under the fuel tank.
2Loosen one or more air cleaner cover bolts on the middle-right side of the motorcycle with a Torx or Allen socket, depending on your motorcycle, and a socket wrench. Disconnect the breather tubes that plug into the top of the air cleaner by hand.
3Unbolt and remove the air cleaner with a Torx or Allen socket, depending on your motorcycle, and a socket wrench. Remove the air cleaner.
4Loosen the hose clamp that attaches the fuel line to the carburetor with a flat-head screwdriver. Pull the fuel line from the carburetor by hand.
5Mark the throttle and idle cables for later assembly with masking tape and a pen and unscrew the cables from the throttle cam.
6Unbolt and remove the air cleaner backing plate with a Torx or Allen socket, depending on your motorcycle, and a socket wrench. Remove the air cleaner backing plate by hand.
7Grab the CV carburetor with both hands and gently pull it from the rubber boot that attaches the carburetor to the intake manifold. Remove the carburetor and the choke assembly from the right side of the motorcycle as a unit.
Saturday, October 26, 2013
How to Use Hose Clamps

A hose clamps design allows it to secure a hose over a fitting, thereby preventing any fluid flowing through the hose from leaking at the connection. Common uses for hose clamps include securing hoses in automotive systems and for clamping lines in household plumbing systems. Hose clamps also work well in other situations where a user desires a strong band clamp, like applications where a zip tie or duct tape might be used.
Instructions
- 1
Expand the hose clamp by turning the screw counterclockwise. Make it large enough to slide over the hose.
2Slide the hose clamp over the hose.
3Slide the hose over the fitting that you want it to attach to.
4Slide the hose clamp over the joint between the fitting and the hose.
5Turn the screw clockwise to contract the hose clamp around the hose to the required tension.
Isuzu Rodeo Lug Torque Specifications
Isuzu introduced the Rodeo SUV in 1990 as a 1991 model and continued selling it until phasing it out in 2004 and replacing it with the Ascender. Isuzu updated and revised the Rodeo several times during the vehicles tenure, and the smaller, two-door Rodeo Sport was available from 1998 to 2003. The torque specs for the Rodeos lug nuts varied from year to year, but in most years all trims shared the same lug-nut specs.
General Torque Information
Torque is the amount of force applied to twist or turn an object at its center. Torque specs are usually given as foot-pounds or inch-pounds, with one foot-pound equaling the force of one pound applied at the end of a foot-long lever to turn an object. It is important to make sure that the threads of the bolt and the lug nut are clean before tightening the lug nuts, as an dirt or build-up on the threads can cause increased fiction and affect the amount of torque needed to properly tighten the bolts. It is common to lightly lubricate a bolt or lug nut with clean motor oil before tightening it. Most mechanics recommend using a torque wrench when tightening bolts, as it is nearly impossible to accurately gauge torque by hand.
The 1991 to 1995 Isuzu Rodeo
For all trims of the 1991 to 1995 Isuzu Rodeo, except for those with aluminum wheels, tighten the lug nuts to 66 foot-pounds of torque. For those with aluminum wheels, tighten the lug nuts to 87 foot-pounds of torque.
The 1996 to 1997 Isuzu Rodeo
The torque specs for the lug nuts were the same for all trims of the 1996 to 1997 Isuzu Rodeo. The lug nuts should be tightened to 66 foot-pounds of torque.
The 1998 to 2004 Isuzu Rodeo and the 1998 to 2003 Rodeo Sport
The torque specs were the same for all trims of the 1998 to 2004 Isuzu Rodeo and the 1998 to 2003 Isuzu Rodeo Sport. The lug nuts should be tightened to 87 foot-pounds.
How to Put a Fuel Pump on a 1994 Dodge Shadow
The Dodge Shadow was a compact car manufactured by Chrysler Corporation from 1987 to 1994. The 1994 version had a 4-cylinder 2.2-liter engine with throttle body injection. This early form of fuel injection used a relatively low fuel pressure of 15 pounds per square inch. The fuel pump in the 1994 Dodge Shadow is attached to the fuel tank, so the majority of the work in the installation of a fuel pump involves the removal of the fuel tank.
Instructions
- 1
Remove the filler cap for the fuel tank to relieve the pressure in the fuel system. Disconnect the cable for the negative battery terminal with a socket wrench to avoid unintentionally starting the engine.
2Loosen the lug nuts on the right rear wheel with a socket wrench. Raise and support the the vehicle on jack stands. Remove the cap from the drain tube on the rear of the fuel tank and connect a siphon hose to the drain tube. Drain the fuel from the fuel tank into a gasoline container. Remove the filler tube for the fuel tank with a socket wrench. Remove the right rear wheel.
3Detach the electrical wiring for the fuel pump and fuel sending unit. Disconnect the fuel lines for the fuel tank and support the fuel tank with a transmission jack. Loosen the mounting straps for the fuel tank and lower the fuel tank slightly with the transmission jack. Disconnect the hose on the pressure relief valve and remove the filler tube from the fuel tank. Remove the mounting straps for the fuel tank and lower the fuel tank with the transmission jack.
4Release the quick-connect fittings for the fuel lines of the fuel sender unit and disconnect the fuel lines. Remove the mounting bolts for the fuel sender unit with a socket wrench and pull the fuel sender unit from the fuel tank. Detach the electrical wiring from the fuel pump.
5Remove the nut for the lower support bracket of the fuel pump. Disconnect the lower support bracket and gasket for the fuel pump. Release the clamp for the inlet hose of the fuel pump and detach the hose. Detach the fuel pump from the fuel sender unit.
6Install the new fuel pump by reversing Steps 2 to 5. Fill the fuel tank and connect the cable to the batterys negative terminal with a socket wrench. Start the engine and check for fuel leaks.
How to Trick Out Your 883 Sportster

Part of the Harley mystique has always been the personalization of the bikes by their riders. Long ago, cheap, used police and Army surplus bikes were stripped down and souped up by men who had to make or modify many of their parts. Now the personalization of Harleys is one of the motor companys most important revenue streams. Harley invites numerous simple modifications to their motorcycles in hopes of selling you the pieces you need. So, anyone can make three quick changes. Exchange the standard seat for one you like better. Install new mufflers to make your bike a little faster. And, install a sissy bar so she wont fall off the back.
Instructions
- 1
Remove the Allen or Phillips head screw and washer that fastens the tab on the back of your seat to the rear fender with a Phillips head screw driver or an Allen key. Remove the seat by pulling the seat up and back.
2Install a new seat by pushing the new seat down and forward. Refasten the seat tab to the fender with the key or screwdriver.
3Remove the trim bolts on the sides of each rear fender holding the nut inside the fender still with an open end wrench and turning the exposed bolt head with a socket wrench and socket. Apply thread locker (a kind of glue for bolts and screws) to the docking bolts included with a sissy bar mount.
4Replace the bolts you just removed with the sissy bar mount docking bolts. Loosely screw the original hex bolts and washers inside the fender to the ends of the docking bolts.
5Push the notches on the two sissy bar mounting plates onto the docking bolts. Tighten the nuts on the docking bolts with an open end wrench.
6Stick the sissy bar sides into the openings on the mounting plates. Secure the sissy bar to the mounting plates with the Phillips head or Allen screws included with your sissy bar kit.
7Loosen the heat shields on your exhaust pipes by opening the worm clamps with a flathead screwdriver.
8Loosen the 4 bolts that hold your exhaust pipes to the exhaust manifold with a socket wrench and socket.
9Remove the bracket that fastens your exhaust pipe to the belt drive cover with an open end wrench. Loosen the clamp that connects the mufflers to the header pipes using a screw driver.
10Unfasten the mufflers from the exhaust bracket by removing the four exhaust bracket bolts with an open end wrench. Pull the mufflers off the exhaust pipes.
11Replace the old mufflers with the new mufflers. Clamp the new mufflers to the old pipes.
12Reconnect the exhaust to the exhaust bracket and the belt drive cover. Re-tighten the exhaust manifold flange bolts and retighten the heat shields.
Friday, October 25, 2013
How to Remove the Taillight for a 1997 Chevy S 10
Removing the taillights from your 1997 Chevy S-10 pickup to replace the bulbs or complete assemblies takes just a few minutes. The taillights on the S-10 use standard 3157 dual-filament bulbs available from any auto parts store. The taillight housing also contains a 921 bulb that illuminates when you shift the truck into reverse. If the entire assembly requires replacement, salvage yards, the dealer or some auto parts stores can provide a new assembly.
Instructions
- 1
Open the tailgate of your S-10, and allow it to rest on the support cables. Locate the two retaining bolts on the inside edge of the tailgate opening, near the latch.
2Remove the two retaining bolts with a 10-millimeter socket and ratchet. Set the bolts aside so you can reuse them later.
3Grasp the taillight assembly from the rear, then pull it straight back from the bedside, removing the assembly from the truck until you can access the wiring on the back.
4Grasp the bulb sockets, rotate them counterclockwise and remove them from the rear of the taillight assembly. Remove the taillight assembly from the truck.
How to Repair a Broken Car Key

Depending on the extent of damage to your car key, there is a chance that it is fixable. If the actual metal piece of the key itself is broken your key cannot be fixed. If the key fob to your car is broken you can have it looked at and repaired by your vehicles dealership if the problem isnt too severe. To find out if your key is fixable, contact your vehicles dealership.
Instructions
- 1
Call your vehicles dealership. Give the dealership the make, model and year of your vehicle and tell them your key is broken and in need of repair.
2Explain the issue in full detail to the mechanic at the dealership. The more information you are able to give the mechanic the better. The mechanic might have some do-it-yourself solutions for you to try on your key depending on what you tell her about the problem your key is having.
3Try all of the solutions given to you by the mechanic. If one works you wont need to take your key to the dealership for repair. If nothing works, schedule an appointment to have your key looked at.
4Take your key to the dealership. From this point, the dealership mechanics will dictate your course of action. Your key may simply need a new battery and youll be able to return home immediately. If your problem is more severe and your keys wont be repaired the same day you might be without a car, or your dealer might issue a loaner vehicle to you. It all depends on your keys issue and your dealerships policies.
How to Repair Paint Damage From Acid Rain

Acid rain is caused when pollutants such as nitrogen oxide and sulfur dioxide combine in the atmosphere and come down with the rain. If you wash your car after it is rained on by acid rain, there will typically be no harm done to your cars paint finish. If you are not able to wash it immediately, there might be damage to your paint. The damage will look like dried water droplets, or a white ring with a clear center. There are different ways to repair the paint, depending on the extent of the damage.
Instructions
- 1
Inspect the extent of the damage to your vehicles paint. There are three different levels of damage. The first level is the least severe and will need very little repair. This is where the damage is only to the surface of the clearcoat of the car. If the damage goes into the clearcoat, it is considered level 2 damage. Damage through the clearcoat and basecoat is considered level 3 damage.
2Wash off the car. Regardless off how much damage there is, washing the car is necessary to get any residue off from the acid rain and to clean off the area you are about to repair. Once the car has been washed, dry it thoroughly and then apply wax to the area you are going to repair.
3Repair the car paint according to the amount of damage that has occurred. For damage just to the surface, use wet sandpaper and gently sand the damaged area.
4Repaint a clearcoat for damage that has occurred to the clearcoat after you have sanded the area. Allow time to dry and apply two to three coats as needed.
5Repaint the basecoat and clearcoat once sanding is completed if the damage is into the basecoat. Allow one to two hours between coats and apply two to three basecoats as well as two to three coats of clearcoat.
6Buff the area with a wool buffing pad and a buffer.
How to Check the Oil on a Craftsman Air Compressor

If you own a home and like to do your own maintenance or are fond of projects, youre sure to realize the many benefits of owning an air compressor. You can attach air compressors to nail guns, sand blasters, caulk guns, spray guns and even air ratchets. The power provided by an air compressor increases your work productivity and efficiency while decreasing the time required on a project. Check the oil levels on your Craftsman air compressor prior to each use.
Instructions
- 1
Turn your air compressor off. Unplug the machine from the power supply unit and allow it to cool down, if necessary.
2Locate the crankcase on your air compressor and identify the oil tank.
3Remove the oil fill plug (sometimes referred to as the dipstick) from the oil fill hole. The oil should be leveled with the oil fill hole. If the oil is 3/8-inch or more below the fill hole, add oil to the tank.
Thursday, October 24, 2013
How to Size an Exhaust System

Prior to building exhaust components, you must first correctly size the individual components, such as the headers and the muffler, for optimal performance. Piping shape and diameter determines exhaust flow and velocity. In terms of diameter, overly small piping will constrict flow and reduce top-end engine power. Small piping does increase exhaust velocity. Excessively large piping allows maximum flow but reduces velocity, which greatly reduces torque without substantially increasing engine power. Exhaust shape and diameter also determine the amount of backpressure, which occurs when exhaust returns into the engine, reducing power and efficiency. Sizing an exhaust system varies by application.
Instructions
Exhaust Header Design
- 1
Locate your vehicles engine information in the owner manual or through the manufacturer. The number of cylinders, engine type, capacity and the engines maximum revolutions per minute (RPM) are extremely important to sizing your exhaust system.
2Write down the engine specifications, which will help formulate the optimal size and diameter of your headers. For example, Custom-Car suggests a 1600cc, 4-cylinder engine with a 5,500 RPM redline requires a primary pipe approximately 1.5 inches in diameter and between 34 and 36 inches in length.
3Open the hood and locate the exhaust headers. The headers are bolted to the engines cylinder ports and lead underneath the vehicle to the front pipe and muffler.
4Measure the headers piping length and diameter as a starting point for building your own.
5Consult a performance exhaust builder in your area for more information on optimal headers sizing, which will vary by car and engine.
6Determine a range of piping diameters and lengths based on the stock size of the headers. Later fabricate a version of each new size. If possible, test each on a dynamometer to find which design creates the best power output.
Muffler Design
- 7
Lift the front of the vehicle with a hydraulic jack, place jack stands beneath it, and locate the muffler assembly. It is the large canister just before the tailpipe. Write down the muffler length and diameter.
8Shop online for a performance muffler assembly specific to your vehicle. Purchase a muffler with a piping length and diameter that optimizes engine performance. Muffler brands provide technical data that states power readings comparing the stock assembly to the specific aftermarket assembly to highlight the power gains.
9Minimize backpressure by selecting a muffler assembly with a flow capacity that corresponds to the flow capability of the engine. Refer to the manufacturer or a trusted mechanic for information on your engines specific flow capability.
10Decide how loud you want the exhaust to be. A free flowing muffler is louder than that with multiple chambers. Sound clips of specific muffler sounds may be provided on the companys website.
11Consult a trusted mechanic before purchasing a muffler. Ask questions about the muffler design and how the internals will affect engine performance and sound.
How to Find the O2 Sensors on a 2008 Softail Deluxe
Your 2008 Harley Softail Deluxe has both a primary and secondary O2 sensor. The primary O2 sensor is located under its own plastic cover, mounted to the front of the engine. The secondary O2 sensor is plugged into the wiring harness, located to the right of the oil tank on the right side of the bike. Accessing your motorcycles O2 sensors may be necessary in order to perform various electrical or engine modifications.
Instructions
- 1
Remove the two bolts at the rear of the seat. Slide the seat back, and remove it from the bike. Underneath the seat is the battery, as well as various parts of the engine wiring system. Use a Phillips-head screwdriver to disconnect the negative battery cable to prevent an accidental short circuit.
2Remove the plastic primary O2 sensor cover, mounted to the front of the engine. This is secured by a plastic clip that can be undone by hand. Underneath the plastic cover is a black wired plug, which is the primary O2 sensor.
3Search along the right side of the motorcycle for the secondary O2 sensor. It is located just to the right of the oil tank, mounted just above the exhaust pipes. The secondary O2 sensor looks exactly like the primary sensor, and is connected into the engine wiring harness, tucked within the chassis frame.
How to Repair a Sway Bar
A sway bar links opposing suspension components to counteract a cars tendency to pitch in tight turns. Most often, sway bars need to be repaired because the linkages between the bar and the suspension become worn or broken. Fortunately, the parts are relatively inexpensive and the repairs are simple for anyone with a floor jack and some free time.
Instructions
- 1
Find the broken link. Use the floor jack to lift the car so the wheel near the broken link is just off the ground. Remove the lug nuts and set the wheel aside.
2Remove the broken linkage with the necessary wrenches. Typically there will be some stress in the sway bar that can be relieved by placing a second jack under the suspension arm and compressing the suspension just enough so you can remove the sway bar linkage.
3Assemble the new linkage in place of the old one. Because different makes and models will vary, follow whatever directions are included with the sway bar repair kit youve purchased to ensure correct installation.
4Replace the bushings at the contact point between the sway bar and the vehicles chassis. Depending on the repair kit that you bought, you may have to purchase new bushings separately.
5Remove the bottle chack from the suspension. Reattach the wheel and lower the vehicle.
6Repeat the process to replace the linkage on the other end of the sway bar. If one linkage has broken it is likely that the other one is also nearing the end of its service life. By replacing the linkages at both ends, you are also ensuring that they will be balanced.
How to Replace a Fog Light Bulb on a 1998 Jeep Wrangler

The fog lights on your 1998 Jeep Wrangler are not merely an aesthetic addition to your vehicle; the lights serve to provide additional visibility in low-light, humid and foggy weather conditions. Your fog light bulb needs to be replaced if it is dim, flickers or has ceased to work completely. You can replace the fog light bulb, and maintain the safety of your Jeep, using a simple Philips screwdriver.
Instructions
- 1
Disconnect the negative battery terminal cable from the Jeep Wranglers battery.
2Disconnect the electrical plug that connects to the back of the fog light bulb by pinching the release tab and pulling back on the plug.
3Turn the bulb counter-clockwise to remove it from the fog light housing assembly. Remove the bulb carefully to avoid breaking it inside of the fog light.
4Insert the new fog light bulb and gently turn it clockwise until it does not turn anymore. Connect the power plug to the back of the bulb, pushing in until the tab on the connector snaps into place.
5Reconnect the negative battery terminal cable.
6Turn on the vehicles lights to verify the fog light works.
Wednesday, October 23, 2013
How to Remove a Fairing FLHTR

The procedure for removing both the inner and outer fairings on any Big Twin, Large Forked, Heavy, Touring Harley, which is what FLHT means, is both complicated and straightforward. The outer fairing and windshield come off first. The ignition must be partially removed. Obvious sections of the electrical harness must be unplugged. The hand controls must be removed from behind the fairing. Then you can finally pry the bat wing off the front of your motorcycle.
Instructions
Remove Outer Fairing and Windshield
- 1
Hang towels over the front fender to protect the paint and chrome. Straddle the front fender and loosen the outer fairing screws just below the windshield with a Torx head socket and ratchet.
2Step to the riders side of the fairing and pull out the two inner fairing screws over the wind deflectors with a Torx head socket and ratchet.
3Turn the handlebars completely right. Loosen and pull out the outer fairing screw under the right fairing cap with a Torx head socket, socket extension and a ratchet.
4Turn the handlebars completely left. Loosen and pull out the outer fairing screw under the left fairing cap with a Torx head socket, socket extension and a ratchet.
5Push the outer fairing forward. Squeeze the two tabs outside the headlight housing and disconnect wiring harness plug connector behind the headlight.
6Pull the outer fairing and the headlight off the motorcycle by hand without knocking the windshield off the motorcycle.
7Set the outer fairing down and pluck the windshield off the front of the bike. Remove and save all pieces.
8Lift the fairing with the headlamp assembly off the motorcycle. Lift the windshield off the bike.
Remove Ignition
- 9
Disconnect the male and female parts of the directional signal and passing lamp connectors. Loosen the passing lamp brackets from the fork brackets with a Torx head socket a ratcheting socket wrench.
10Remove the passing lamp from the forks.
11Insert the motorcycle key in the motorcycle ignition. Turn the key to "unlock" and set the ignition knob to "access."
12Push the catch tab on the bottom left of the ignition knob with a flathead screwdriver. Push down and turn the key from 5 oclock to 3 oclock. Pull the knob off the ignition.
13Remove the switch nut from the nut stud with a ratcheting socket wrench, socket extension and hex socket.
Remove Hand Controls
- 14
Remove the chrome trim from the inner fairing by hand and set aside
15Pull up the rubber boot that covers the clutch cable adjuster assembly on the left side of the bike. Turn the long clutch cable adjuster jam nut and the clutch cable adjuster nut in opposite directions with two open end wrenches.
16Completely loosen the clutch cable by turning the clutch cable adjuster nut with your fingers.
17Remove the pivot pin retaining ring from the pivot pin on the bottom of the clutch hand control assembly with a flathead screwdriver. Pull the pivot pin out of the top of the assembly with needle nose pliers.
18Unfasten the clutch hand control assembly with a Torx head socket and ratchet. Remove the clutch hand control from the clutch hand control assembly.
19Lift the clutch control pin from the clutch cable. Push the clutch cable and through the weatherized hole in the inner fairing.
20Stick a 5/32 inch thick cardboard insert between the front brake hand control and the front brake hand control bracket to protect the rubber boot and plunger on the front brake hand control stoplight switch and plunger.
21Loosen the switch housing and master cylinder screws with a Torx head driver and ratcheting socket wrench. Remove the switch housing and master cylinder.
22Slip the throttle off the handlebars with the help of a flathead screwdriver. Unhook the two throttle cables from the cable housing.
23Push the two throttle cables through the weatherized hole in the inner fairing.
Remove Inner Fairing
- 24
Disconnect the cigarette lighter contacts.
25Disconnect the right and left speaker adapters from the inner fairing with a Torx head socket, a socket extension and a ratcheting socket wrench.
26Unplug the fuel gauge and voltmeter male and female wiring harness plugs. Loosen the four screws that hold the inner fairing to the fairing bracket with a Torx head driver, a socket extension and a ratcheting socket wrench.
27Pull the inner fairing and fairing bracket apart with your hands to separate them both from the mounting pins.
28Lift the fairing bracket and inner fairing straight up. Pull the fairing bracket and inner fairing apart and remove the inner fairing.
Rotary Lift Installation Specs

Rotary is a brand of vehicle service lift produced by the Vehicle Service Group and distributed throughout the world. The lifts are available in several configurations, including small mid-rise lifts, two-post lifts and heavy duty four post truck lifts. Each lift has a set of requirements that must be met when it is installed. Because Rotary lifts often raise several tons into the air, these installation requirements are an important factor in keeping operators safe.
Concrete
Rotary lifts must be installed on a quality concrete floor that is free of cracks and defects. The minimum anchor depth for Rotary lifts is 3 1/4 inches. The total overall concrete thickness must be at least 4 1/4 inches for two-post lifts, or 5 inches for heavy-duty four-post lifts. The concrete must be rated to withstand 3,000 pounds per square inch. Rotary lift concrete anchors must be torqued to 150 foot-pounds.
Bay
Standard two-post Rotary lifts must be installed in a bay of at least 12 feet inch length and 24 feet in width. For heavy duty two-post lifts, this requirement increases to 12 feet by 26 feet. Low rise Rotary lifts must be installed in an 11-foot-by-24-foot bay, while four-post lifts require a 15-foot-by-23-foot bay size. The minimum ceiling height for a Rotary lift is 10 feet. Heavy duty four-post lifts require approximately 5 feet of additional ceiling clearance.
Electrical
Rotary lifts can be installed using several different electrical sources. The required electrical breaker size changes depending on the input voltage. For single-phase 100 volt installations, lightweight Rotary lifts require a 15 amp breaker, while larger lifts need a 25 amp breaker. Single-phase 220 volt installations must have either a 20 amp or 40 amp breaker, depending on the capacity of the lift. This breaker requirement drops to 20 amps if three-phase wiring is used. Installations using 400 volts and three-phase wiring require only a 10 amp breaker.
Hydraulic
Rotary lifts require Dextron III automatic transmission fluid, or a similar International Standard for Organization specification fluid for use in the hydraulic system. Standard two-post Rotary lift installations must have 19 quarts, or 17.98 liters, of fluid. The lightweight mid rise lift requires only 6.5 quarts, while the heavy duty Rotary lift must have 22 quarts.
How to Drive With a Bad O2 Sensor
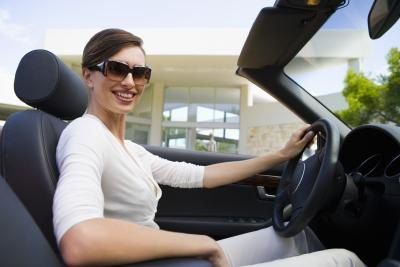
Automotive O2 sensors determine in real time if the air fuel ratio of your vehicles engine is lean or rich. They make electronic fuel injections and emission control possible. Sensors typically last from 30,000 miles to more than 100,000 miles. Driving with a bad O2 sensor is like avoiding going to the dentist. You will cause damage to your car, just as you would cause damage to your teeth by avoiding the dentist. The only issue is how much damage you are willing to endure before you replace your O2 sensor.
Instructions
- 1
Drive the speed limit at all times. Do not speed. Your gas mileage and catalytic converter are already in jeopardy due to the bad O2 sensor. The harder you drive, the more damage you will cause to your catalytic converter.
2Accelerate slowly. Slamming on the gas to achieve quick acceleration will exacerbate any damage being done to your vehicle.
3Brake often. Again, the slower you drive, the better. Leave at least three to five seconds of time between yourself and the vehicle in front of you.
4Plan out your trips before you leave your home. If you plan ahead of time, you will avoid backtracking and any unnecessary driving.
5Limit driving as much as possible. If you can wait to mail that letter to your grandma, wait. If you can walk to any spots you need to go to, do so. Walking is good exercise and it will limit wear and tear on your car.
Manual Transmission Removal for a Ford Explorer
Exercise caution and safety measures if you decide to remove the manual transmission from your Ford Explorer sport-utility vehicle. The task will require that you move one of the heaviest components of your vehicle as you remove other pieces of equipment. It will take several hours but you can save a substantial amount of money on repairs if you remove the transmission yourself.
Instructions
- 1
Open the hood and detach the battery cables.
2Remove the upper part of the gearshift, boot, console and lever with a socket wrench and Phillips screwdriver.
3Lift the front and rear of your Ford Explorer with a floor jack and position the four jack stands beneath the frame. Lower the frame onto the jack stands.
4Position a catch bucket beneath the transmission. Remove the drain plug with a wrench and drain the transmission fluid.
5Unplug all electrical connectors, sensors and wire harnesses from the transmission.
6Remove the starter motor from the engine with a socket wrench.
7Use a socket wrench and pry bar to detach the front drive shaft if your Explorer has a transfer case.
8Repeat this process with the rear drive shaft with the same tools.
9Detach the exhaust inlet crossover pipe and catalytic converter with the socket wrench. A breaker bar may be necessary to use on the exhaust pipe mounting bolts for leverage.
10Support the transfer case, if your Explorer is so equipped, with a transmission jack. Use the socket set to detach the transfer case and and remove it.
11Detach the clutch hydraulic line from the clutch slave cylinder with the disconnect tool.
12Hold up the transmission with a transmission jack and a safety strap.
13Loosen the two nuts that secure the transmission insulator to the cross-member with a socket wrench.
14Loosen the six bolts that secure the cross-member to the frame with a socket wrench.
15Remove the two nuts that secure the transmission insulator to the cross-member. Remove the cross-member.
16Loosen the nine bolts that secure the transmission to the engine.
17Remove the transmission from the vehicle.
Tuesday, October 22, 2013
How to Find an Auto Mechanic Thats Honest With Repairs

At some point nearly every car owner will need to have a car repaired, and the majority feel forced to rely on the mechanic to make an honest assessment of the work necessary to maintain or repair the car. Since most drivers do not have the knowledge or equipment required for anything but the simplest repairs, they need guidance on how to find an honest mechanic. A few simple steps can lead a car owner to that very person.
Instructions
- 1
Ask a specialist in diagnostics to assess repairs and maintenance for the car. A diagnostician has no reason to add nonexistent problems to a list of repairs, but he will want to include all the real problems to earn the customers future business. Compare what the diagnostician found to what other shops tell you.
2Ask friends, family or an insurance agent for recommendations. Make sure they have actual experience with a mechanics work.
3Call any potential repair shops to ask for a list of their trade association memberships and call those associations to confirm membership. Check a shops complaint history with your states consumer protection agency or the local Better Business Bureau. This history also may include the resolution of those complaints. Look not only for the mechanic with a low number of complaints but also for a mechanic with a good history of complaint resolution.
4Ask mechanics about their ability to work on your make and model and check their shops for certifications to work on that make and model. Also look at the cars on the work bays or on the lot. A number of cars of the same or similar make and model indicate an ability to work on your car.
5Determine the shops prices and the warranty on work done. Shops often post that information in plain view on the work floor.
6Talk to the mechanics in the shop. Their willingness to answer questions and the clarity of their answers are indicators of their honesty.
7Instruct the mechanic to diagnose the car and reject any mechanic whose estimate is grossly in excess of the diagnostic mechanics estimate. Review the proposals for a clause specifying the installation of new parts rather than used ones.
F150 Alignment Specifications
Produced by the Ford Motor Corporation, the Ford 150 is the most common variant of the Ford F-Series. This truck was named Car of the Year in the U.S. for 23 consecutive years and also best selling truck for 30 years. The second generation was launched in 1953 and 2009 saw the launch of the 12th generation of this truck. Like the old generations, the alignment specifications for all the two-wheel drives has been the same, while that for the four-wheel drives has also been the same -- except for the Raptor.
2010 F-150 Two-Wheel Drive
In the two-wheel drive, the ideal caster settings are +3.9 degrees for the front left wheel and +4.3 degrees for the front right wheel. There is an allowance for 1 degree in either direction for each wheel, with a cross tolerance of 0.75 degrees. The camber settings are -0.2 degrees for the front left wheel and -0.4 for the front right wheel. The range of variation is 0.75 degrees in either direction, or a cross tolerance of 0.75 degrees. The ideal settings for the toe-in is +0.2 degrees, but can range by 0.2 degrees in either direction.
2010 F-150 Four-Wheel Drive
In the four-wheel drive, the ideal caster settings are +3.8 degrees for the front left wheel, and +4.2 degrees for the front right wheel. There is an allowance for 1 degree in either direction for each wheel, with a cross tolerance of 0.75 degrees. The camber settings are -0.2 degrees for the front left wheel and -0.4 for the front right wheel. The range of variation is 0.75 degrees in either direction, or a cross tolerance of 0.75 degrees. The ideal settings for the toe-in is +0.2 degrees but can range by 0.2 degrees in either direction.
2010 F-150 Raptor
The caster setting for the front wheels is +3.7 degrees, with a one degree in either direction range or a cross tolerance of 0.75 degrees. Front end wheels camber settings for both wheels are -0.45 degrees, with a range of 0.75 degrees in either direction.
How to Replace the Weatherstripping in the Vent Glass on a 1957 Chevy

Weatherstripping in your 1957 Chevy protects the interior of the car by keeping out wind, rain and snow with a tight seal between windows and doors. Weatherstripping in vent glass can wear out and lose its ability to seal. Chevy owners who want to save money can do the job of replacing the weatherstripping with simple tools and supplies purchased from an auto parts store.
Instructions
- 1
Roll down and examine all windows to determine whether the weatherstripping is cracked or brittle. If so, the weatherstripping will have to be replaced.
2Use needle-nose pliers and a razor blade knife to remove the cracked, brittle weatherstripping. Cut underneath it with the razor blade and pull the weatherstripping out with the needle-nose pliers.
3Scrape off any old glue stuck to the door frame with the razor blade knife.
4Spread a thin layer of glue from the weatherstripping kit onto both the door frame and the weatherstripping. Allow the glue to dry to tacky. Slide the weatherstripping into the door frame with the pliers and press the surfaces together. Repeat the process for the other side.
5Repeat Steps 2-4 at any other windows for which weatherstripping needs to be replaced.
6Allow the glue to dry for 30 minutes, then carefully roll up the windows. Allow the windows to remain undisturbed for at least a day before rolling down the windows.
Lumina Parking Brake Adjustment Tips

You can adjust the parking brake on your Chevy Lumina right from your home garage, saving yourself time and money. The parking brake can be adjusted from inside the vehicles center console. You just need a couple of tools from your local auto parts retailer and about a half hour of time to get the job done. You will know its time to adjust the parking brake if your vehicle starts to move while parked on a downhill slope with the parking brake set.
Accessing the Parking Brake Cable
Release the parking brake lever. Locate the two screws on either side of the center console cover between the driver and front passengers seats. Pull up on the release lever and remove the screws on the console with a screwdriver. Pull straight up on the console cover to remove it.
Adjusting the Parking Brake Cable
Locate the two nuts on the parking brake cable. Turn the nuts in a clockwise direction with a wrench to tighten the cable. This adjusts the parking brake.
Finishing Up
Put the console cover back into place and tighten the screws with the screwdriver. Pull up on the parking brake lever. It should pull up a maximum of six clicks or less.
Monday, October 21, 2013
How to Restore a Vintage Steering Wheel
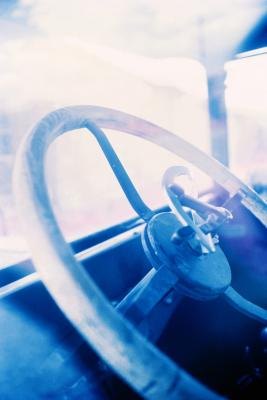
Restoring an old car involves cleaning and repairing every area of the vehicle, including the steering wheel. Vintage steering wheels feature a metal or plastic wheel with a plastic, vinyl or leather covering. Steering wheels go through a lot of wear and tear from routine use, which results in cracks, scratches and other damage to the outer covering. Restoring your old vintage steering wheel repairs those cracks, making the wheel look new again.
Instructions
- 1
Remove the steering wheel, and place on a flat surface covered with old newspaper. Open the epoxy, and mix the two parts, following the manufacturers recommendations. Dip the craft stick into the mixture, and smooth over any scratches, dings or chips on the wheel.
2Rub the epoxy areas with 100-grit sandpaper, once the epoxy cures for at least 24 hours. Smooth the edges of the epoxy, before moving to the 220-grit sandpaper. Use the higher grits until the epoxy sits flush and even with the steering wheel.
3Turn the steering wheel over in your hands, looking for any imperfections on the wheel. Cover those areas with a thin layer of auto primer. Once the primer dries, lightly sand the surface with 220-grit sandpaper, creating a smooth surface.
4Paint the repaired areas of the steering wheel with auto paint or epoxy paint. Lightly feather out the edges of the paint with your fingers, making the new paint blend with the original color of the cover on the steering wheel.
5Dip a piece of aluminum foil in distilled white vinegar, and rub it briskly across any chrome or metal decorations on the steering wheel. The combination removes any rust, pitting or other damage on the chrome and gives the steering wheel its naturally bright and shiny appearance.
How to Set a Fork Oil Level on a Harley Davidson FLHX

The correct procedure for setting the fork oil level on any FLH, including the FLHX, is arcane. You put the right amount of oil in and then, using a special tool that looks like a bicycle pump, you take just a little bit out. Worse, the tool is sold only by Harley-Davidson. When a clever service writer really wants to snooker you he will tell you something to the effect of your right fork taking 11.2 ounces of oil but your left only taking 11.1. The numbers he gives you are the product of the arcane official Harley procedure, not any mechanical difference between your forks.
Instructions
- 1
Measure 11.2 fluid ounces, which is 300 milliliters, of Harley Davidson fork oil or the equivalent into a measuring cup. Pour the fork oil into the top of a dry FLH fork from which you have removed both the fork cap bolt and the fork tube plug but not the fork spring.
2Push the fork tube into the slider several times to remove trapped air from the fork tube.
3Loosen the metal set ring on the front fork oil level gauge by loosening the thumbscrew. Measure 125 millimeters from the end of the oil level gauge tube with a metric ruler.
4Adjust the metal ring on the front fork oil level gauge so that the bottom of the ring is exactly 125 millimeters from the end of the gauge tube. Tighten the thumbscrew.
5Push the fork oil level gauge handle all the way into the gauge. Set the metal ring on top of the fork and insert the gauge tube into the fork.
6Pull the fork oil level gauge all the way up to suck out any excess oil in the fork tube. Expel the excess oil into a drain pan and repeat the process for the other fork tube.
How to Replace a Water Pump for a 1998 Chevrolet Monte Carlo
Its not difficult to replace the pump for a 1998 Chevrolet Monte Carlo. In fact, replacing a pump should a priority since a deteriorating pump is generally the root of poor fuel economy and lackluster vehicle performance. The Monte Carlos engine wont even operate if the pump isnt working. The pump located inside the 1998 Chevrolet Monte Carlo is accessed through a panel in the trunk.
Instructions
- 1
Use the socket wrench to remove and take out the fuel pump relay. Its attached on the engine compartments right side near the fuse panel. Turn on the engine. Let it run until it stops so that the fuel pressure will be relieved.
2Take out the trunk liner. Remove the cars spare tire. Youll now see the cars access panel which will allow you to access the pump. Take of the bolts which hold the pump in place. Take off the panel.
3Inspect the pump assembly. Clean out any dirt or debris from around it. Unsnap the fittings which keep the lines in their place. Disconnect the electrical connector. Unlatch and remove the large ring which holds the pump assembly.
4Take off the pump assembly. Replace it with the new one. Put the latch back into its original place. Carefully plug the electrical connector back in. Put the spare tire back in and reinstall the access panel.
How to Lower a Motorcycle With Shock Absorbers Without Springs

The shock absorber springs on a motorcycle have nothing to do with lowering the seat height, which is what riders are usually trying to accomplish by lowering the rear end. Some motorcycle shock absorbers have visible springs encasing the damper tubes, and some have only damper tubes. Whatever the brand, model or year of your motorcycle, it came with shock absorbers that are exactly the length your bikes manufacturer recommends. And, regardless of the bike, shock absorbers sold as "under standard length" in 1/2-inch increments are readily available. Just install a set of shock absorbers that are 1 inch under standard length.
Instructions
- 1
Raise the motorcycle to be fully upright and level by either placing the front wheel of the bike in a motorcycle chock, clamping the front wheel in a motorcycle vise on a motorcycle lift, or slightly raising the bike on a motorcycle jack.
2Remove the lower then the upper shock absorber mounting bolts on the right-side shock, using a standard or metric hex socket, Torx socket or Allen socket and a socket wrench. The socket you will use depends on the manufacturer, model and year of your motorcycle.
3Remove the right-side shock absorber. Unfasten the same four bolts on the left side of the motorcycle and remove the left shock absorber.
4Clean the bolts, nuts and washers you remove with a rag and light oil. Apply a few drops of thread locker to the old bolts.
5Replace the old shock absorbers with new, shorter shock absorbers on both sides of the motorcycle using the old bolts, washers and nuts.
6Remove the bike from the chock, motorcycle vise or motorcycle jack.
7Sit in the saddle. Bounce up and down. Ensure the shocks work properly.
Sunday, October 20, 2013
How to Set a Hydraulic Relief Valve

Hydraulic relief valves limit the maximum system pressure to protect system components. The valves also limit the maximum output force of the hydraulic system. Although they have a number of variations, all valves work by balancing the hydraulic force with an adjustable spring force. Heat is created whenever the relief valve opens in response to a predetermined pressure. A correctly adjusted relief valve will enable the system to operate as designed while controlling the amount of heat generated.
Instructions
- 1
Refer to the machine drawings to determine which circuit requires adjustment. Locate the relief valve for the circuit. Relief valves are always piped in parallel to the pump and are normally as close to the pump as possible.
2Locate and remove the hydraulic hose or hoses on the system side of the relief valve. Cap off the hose and valve with the correct JIC caps or plugs as required. Do not cap off the return or tank side of the relief valve. Capping off or plugging unused hoses and fittings prevents the loss of hydraulic fluid and the introduction of contaminates into the system. Using any other method of capping or plugging a hose other than with the proper JIC plug or cap is unsafe and should never be attempted. This deadheads the hydraulic circuit in order to isolate the system to just the pump and relief valve.
3Connect a 5,000 psi pressure gauge between the relief valve and the pump. Most equipment will have a port already installed for this purpose. If no port is already installed, then use the correct adapter to install the gauge.
4Loosen the pressure relief valve adjustment all the way out. The relief valve will normally have a locking hex nut and either an Allen head adjuster or hand wheel adjuster. Start the equipment and activate the hydraulic circuit. The pressure reading on the gauge should be close to zero.
5Adjust the relief valve by turning the adjuster clockwise until the reading on the gauge builds to the pressure indicated on the machine drawings. This is what is known as the valve "cracking" pressure, which is the pressure at which the relief valve starts to open. Tighten the adjuster lock nut securely, being careful not to disturb the valve setting.
6Shut down the machinery and allow the pressure to bleed off. Remove the JIC plugs and caps, and reconnect any hoses that were removed in Step 2. Start the machinery, and test the relief valve by actuating the circuit. The pressure reading on the circuit should not at any time rise above the pressure that was set on the relief valve.
Tips for Loud Exhausts

Your vehicles exhaust noise is determine by the engine size, engine type, exhaust piping, muffler and muffler location. The engines combustion gases are ported out the exhaust manifold through pipes into the catalytic converter (if installed), then through the muffler and finally escaping through the tailpipe. The largest contributor to your exhausts sound profile is the muffler. Mufflers that dampen the sound may have multiple chambers and baffles that reflect and absorb sound waves. Mufflers with straight-through designs allow much of the exhaust sound to pass through to the tailpipe.
Sound-Dampening the Cabin
Muffler sound, which is felt and heard in the cabin, can be controlled by installing sound-dampening material. Mats of sound-dampening material should be placed under the carpet, against metal surfaces and in the walls of the doors to reduce vibration.
Muffler Change
Exchanging a muffler for a different style will allow you to alter the exhaust sound profile. For increased sound and resonance, glass packs, straight pipes and mufflers without chambers should be installed. For reduced sound, consider mufflers with sound-dampening baffles and chambers. Increases in pipe size (which will increase the volume of noise) can also be considered when changing the muffler system. Pipe sizes different from stock size should be investigated to determine the effect on engine performance.
Exhaust Tips
Tips that are lined with fiberglass or sound-dampening layers of material are referred to as "resonated tips." Resonated exhaust tips are installed on the tailpipe and reduce the amount of noise the exhaust system produces at the tip.
Tip shapes and styles (such as flared, beveled, dual-walled, and diameter-changing tips) may also affect the loudness of the exhaust and the tone.
Sound-Dampening Exhaust Wrap
To dampen the vibration and resulting escape of sound waves from the exhaust system, consider installing high-temperature exhaust wrap on the exhaust pipes and muffler. The wrap may also be insulating, reducing the overall temperature transferred to the vehicle. Use caution when installing exhaust wrap as moisture collection may result in accelerated decay of the underlying metals.