Friday, January 31, 2014
My 2003 Chevy Trailblazer Wont Start

The 2003 Chevy Trailblazer is mid-sized SUV. If your Trailblazer will not start, you could be looking at a problem with the battery or the fuel level in your SUV. When the battery charge is too low, the engine will not be able to start. The engine runs on gas so you need a sufficient fuel level to get the motor running. You can troubleshoot the problems with your Trailblazer with little knowledge of the subject before you go see a mechanic.
Instructions
- 1
Open the hood to your Trailblazer and locate the battery next to the engine.
2Take a socket wrench and loosen the battery terminals. Look the battery terminals over for any corrosion. Use a wire brush and soda to get rid of the corrosion.
3Replace the battery terminals on the battery and then try to restart the Trailblazer.
4Use another car and a pair of jumper cables to "jump" your Trailblazer. Leave the SUV running for 5 minutes to charge the battery before cutting it off.
5Try to restart the SUV. If the SUV does not restart, replace your battery.
6Check the fuel level in your Trailblazer. Put gas into the gas tank and try to restart the car. Your car may have a broken fuel gauge. Adding gas will allow the car to start properly.
How to Remove S 10 Headliners

Removal of a Chevy S-10 headliner may be required for a variety of reasons. Fortunately, the procedure is quick and not particularly difficult. Care should be taken, however, if the headliner is to be retained, because headliners are nothing more than shaped foam boards that have felt material glued to one side. Breaking them is easy to do, and they may not be repaired once broken.
Instructions
- 1
Loosen the two front trim posts of the S-10s interior; they are difficult to remove entirely. Remove the rear two trim posts.
2Position the seats all the way forward to give yourself room to work.
3Unscrew and remove the dome light from above the rear window of the truck. Remove the screws securing the sun visors and remove the visors.
4Pull the headliner down from the back of the cab of the truck. The front of the headliner will slide out from the front trim panels. Turn the headliner on its side and remove it through either side door.
Thursday, January 30, 2014
How to Change a Fan Belt on a 1994 Chevrolet Blazer
The fan belt on the 1994 Chevrolet Blazer not only turns the radiator fan, it also runs the alternator, water pump and other accessories located on the engine. This type of belt is called a serpentine belt because it resembles a snake by wrapping around so many pulleys on the engine. Over time, the belt can experience dry rot and cracking, despite being lined with steel braiding. Replace the belt, if it appears worn, to avoid getting stranded on the road.
Instructions
- 1
Map out the serpentine fan belt, noting how the belt wraps around each pulley. The serpentine fan belt is located between the engine belt and the radiator fan. Sketch out a diagram on a piece of paper. A diagram is also printed on the underside of the engine hood or on the fan shroud, but it may be missing.
2Locate the tensioner pulley. On the 3.8-liter engine, the pulley is located between the alternator and the power steering pump. On the 2.8-liter engine, the pulley is located between the alternator and the air conditioner pump. The pulley has a square hole in the center of it. The diagram on the underside of the hood also shows the location of the tensioner pulley.
3Place a 3/8-inch ratchet drive into the square hole and set the ratchet setting counterclockwise.
4Pull up on the handle to release pressure on the serpentine belt then slide the bottom of the belt off the tensioner pulley.
5Remove the belt from the rest of the pulleys then place the new belt onto the pulleys. Follow the belt routing diagram to ensure each pulley turns in the correct direction.
6Pull up on the handle of the ratchet and slide the belt under the pulley. When you release the ratchet, the tension pulley applies tension to the belt.
How to Clamp Exhaust Pipes Together
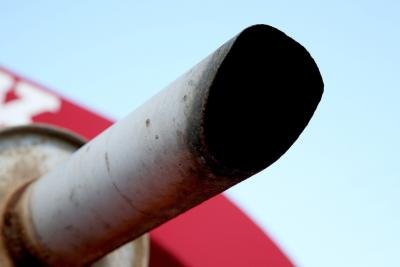
The exhaust system of your vehicle directs exhaust fumes from the engine away from the passenger compartment of the vehicle. Exhaust clamps not only hold the exhaust pipe together, but also ensure your safety by keeping dangerous carbon monoxide from entering your vehicle. When carbon monoxide accumulates in your vehicle, it displaces oxygen and in high concentrations can cause you to pass out and possibly die from asphyxiation. Theore, it is vital that you properly install the exhaust clamps to eliminate carbon monoxide from entering your vehicle.
Instructions
- 1
Put on your safety glasses and work gloves.
2Disassemble the exhaust clamp by loosening and then removing the hex nuts from the U-bolt.
3Place the saddle on the top of the exhaust pipe connection, slide the U-bolt into the saddle and thread one hex nut on each leg of the U-bolt. Do not tighten the hex nuts, as this will hinder your ability to perform the next step.
4Apply pressure to the exhaust pipe connection to ensure that the connection is fully seated.
5Select a socket from the socket set that matches the size of the hex nuts, and attach it to the 3/8-inch ratchet.
6Set the ratchet to tighten.
7Slide the socket onto one of the hex nuts and tighten the nut until it is tight.
8Repeat the process to tighten the other hex nut.
9Check the first hex nut that you tightened with the ratchet for tightness. If the nut is loose, re-tighten it. You should notice the exhaust pipe pulling in under the pressure of the exhaust clamp.
10Pull on the exhaust clamp to ensure that it is tight, and then perform the same steps on any other exhaust clamps you need to install.
Harley Davidson Motorcycle Tools

Brand new Harley Davidson motorcycles often come with a basic toolkit for minor roadside repairs. Used bikes may not include tools, and you may wish to build a small toolkit to keep on your bike. With hundreds of tools on the market, it is not easy to decide which ones you will need. The following suggestions may help you determine the most essential tools, and those that will only add unnecessary weight.
Basic Tool Kit
A basic tool kit, when purchased from a reputable company, will offer all the basics you need for roadside maintenance. Cruztools offers the Roadtech H3 Tool Kit for about $100. Beza offers the Windzone Tool Set for around $60. Harley Davidson has the Snap-On Tool Kit for around $200. Each kit is specifically designed for Harley Davidson bikes and includes wrenches, pliers, sockets, hex keys, torx keys and screwdrivers.
Spark Plugs
Malfunctioning spark plugs is one of the more common reasons for roadside maintenance. Have a spare set with you as a part of your tool kit. A spark plug gap feeler gauge is a helpful tool. Make sure you have the appropriate sized ratchet and socket to removing and reinstalling spark plugs.
Helpful Extras
A kit is not complete without a few basic necessities. Add a flashlight, tire gauge, tape, lube and cable ties if they are not already included in the kit you purchase. Carry a cell phone with you when riding your Harley for the times you need more than your tool kit to get back on the road.
Wednesday, January 29, 2014
How to Reset the Airbag in a PT Cruiser

When the Supplemental Restraint System (SRS) light illuminates on the PT Cruisers instrument cluster, it is because an error code is being sent to the On-Board Diagnostics computer from a sensor in the airbag system. Error codes are used to diagnose problems with the vehicle. Reset error codes using an OBD scan tool. This hand-held device can be purchased from most auto parts retailer. Ensure you reset the computer after finishing repairs on the airbag system, or risk damaging the vehicles computer.
Instructions
- 1
Locate the OBD port that is the same shape as the OBD scan tools connector end. This port can be found on the drivers side dash near the steering column.
2Plug the scan tool into this port. Put the key into the ignition and turn it to the "Run" position, but dont start the engine.
3Wait for the scan tool to interface with the computer. Locate the "Delete Codes" command and select it. Wait for the scan tool to erase all codes.
4Unplug the scan tool and start the engine. Verify the SRS light has turned off on the instrument panel.
How to Replace the Oxygen Sensor on a 2001 Toyota Tundra
The oxygen sensor in your 2001 Toyota Tundra may one day go bad and need replacement. The oxygen (O2) sensor is responsible for regulating the oxygen and fuel ratio in your vehicle, contributing to the efficiency of gas usage. If the oxygen sensor goes bad, your Tundra may run poorly and get poor gas mileage. Knowing how to replace it yourself can save you money.
Instructions
Instructions
- 1
Locate the oxygen sensor on the pre-catalytic converter. This is located near the right-front wheel well of your Tundra.
2Detach the large air intake pipe that is connected to the air box going to the rear turbo. Also remove the two smaller air pipes connected to the air box running to the blow off. This will give you access to reach the sensor. Soak the oxygen sensor in penetrating oil (WD-40 or similar) to loosen it for easier removal.
3Use the 7/8-inch wrench to remove the old oxygen sensor. Find the stock sensor wire near the engine lift loop by the firewall. Splice the stock sensor wire and connect it with the wires to the new oxygen sensor using crimp connectors.
4Apply some of the anti-seize paste to the threads of the new sensor. Be caul not to get any of the paste on the sensor itself or it will ruin it. This will make the oxygen sensor easier to remove the next time.
5Screw the new sensor in by hand. Fully tighten it with the wrench so it can not be loosened by hand. Reattach the air pipes again.
Tuesday, January 28, 2014
How to Reset the Code on an Infiniti

You can reset the code on your Infiniti right from your home garage, saving yourself time and money. If your Infiniti was manufactured in 1996 or later, you need to purchase an OBD II scan tool. If your Infiniti is an earlier model, you need to buy an OBD I scan tool. In either case, you can purchase one of these tools from your local auto parts retailer. The Infiniti comes equipped with an on-board diagnostics computer that stores trouble codes. The scan tool reads the trouble codes to help you troubleshoot the problem with your vehicle. Once the vehicle has been serviced or repaired, you or your mechanic may need to reset the code using the scan tool.
Instructions
- 1
Locate the OBD port on the drivers side dash underneath the steering column. Plug the OBD scan tool into this port. Dont force it in because you may bend the pins inside.
2Put the key into the ignition and turn it to the "on" position, taking care not to start the engine.
3Wait while the scan tool interfaces with the computer. Select "Delete Codes" or a similar command to erase the codes and reset the computer. Wait until the scan tool indicates that it has completed the task.
4Unplug the scan tool from the port and start the engine. Verify that all warning and service lights have shut off.
How Do I Remove an AMC 304 Dipstick Tube
Removing the dipstick tube from your AMC 304-cubic inch engine allows you to replace a defective tube or install a chrome or custom tube. The 304 engine was used in many AMC models but was primarily the same engine configuration in all of them. The dipstick tube is on the passengers side of the engine and pushes into the block just above the oil pan mounting rail.
Instructions
- 1
Locate the dipstick tube on the passengers side of the engine. The tube runs down to the engine block just above the oil pan.
2Pull the dipstick out of the tube and set it aside. It will be in the way, when you try to remove the tube, if you leave it in place.
3Place an oil drain pan under the engine, just below the tube. This will catch any drips from the engine while the tube is out of the engine block.
4Grasp the dipstick tube at the top with a pair of pliers. Do not crush the tube. Pull the tube up, while wiggling it back and forth, until it comes loose from the block. Lift the tube out of the engine compartment.
Monday, January 27, 2014
Why Are Catalytic Converters Necessary

If you have a social conscience (or just dont like paying huge fines and having your car impounded), then consider catalytic converters a necessity. Modern catalytic converters arent nearly as restrictive as older units and can help prevent dangerous pollutants from entering the air and groundwater.
The Law
The main reason why catalytic converters are necessary is that the law says so. Catalytic converters were originally a voluntary measure but became required equipment for all cars sold in America in mid-1986.
Carbon Monoxide
One of the main jobs of a catalytic converter is to convert the dangerous pollutant carbon monoxide into harmless carbon dioxide, which it does with nearly 99 percent efficiency.
Nitrogen Oxide
Considered a volatile organic compound (VOC), nitrogen oxide reacts with sunlight to form smog. Catalytic converters break this toxic chemical down into its component oxygen and nitrogen molecules, making for cleaner skies and longer lives.
Unburned Fuel
No engine burns all of the fuel that it ingests. Catalytic converters burn what little unburned gas the engine hasnt consumed to keep it from polluting groundwater upon exhalation.
Computer Issues
Removing a catalytic converter without installing a simulation sensor will cause a cars computer to malfunction, which will drop engine power by changing fuel and spark parameters until the catalytic converter is replaced.
My Hood Wont Latch

Most automobiles contain a drivers side cable that causes the latch on the hood to open when you pull it. If your hood does not latch, you might have a broken latch cable or an issue with the assembly of the latch. But if the problem is less complex, such as a latch mechanism that is simply stuck in the open position, you can fix it easily enough.
Instructions
- 1
Prop your vehicles hood open.
2Spray the hood latch with WD-40. Give the solution about five minutes to absorb into the mechanism.
3Moisten the latch cables with the WD-40. If they are inside a rubber compartment, such as a rubber guide, insert the can of WD-40 at the tip of the opening and shoot the lubricant onto the cables. Otherwise, spray the lubricant directly onto the cables.
4Grab the latch with your hands and push it until it closes. Move the latch back and forth until it opens and closes with ease. The hood should now latch when you attempt to close it.
Sunday, January 26, 2014
What Does a Rocker Arm Do in a Car Engine
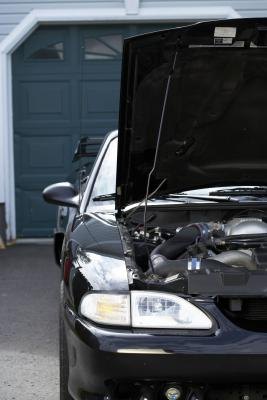
The rocker arm of an internal combustion engine changes radial movement into linear movement; this kind of device is properly called a reciprocating lever. It takes the spinning motion of the overhead camshaft and turns it into the up-and-down movement that opens and closes the valves. Because they are typically made of steel, rocker arms have a great deal of strength for their weight, and can theore exert a great deal of leverage.
Cam Lobe
The camshaft is not a true spherical rod; it has bulges on it called lobes. The lobes project outward from one side of the shaft, while the back of the shaft -- opposite the lobe -- does not have a projection. As the shaft rotates, the side with the lobe lifts the outside end of the rocker arm, and then the side without the projection allows it to fall back. The cams movement is transferred to the rocker arm by a device called a cam follower, of which there are different types that vary by manufacturer and by vehicle age. As the cam shaft spins, the part of the rocker arm acted upon by the cam follower is lifted and lowered, lifted and lowered.
Valve
Just as the outside end -- the cam end -- of the rocker arm moves up and down, so does its opposite side. As the cam lobe comes round it lifts the outside of the rocker arm, which rocks, and the inner end pushes down on the valve stem, opening it against its spring. As the lobe rotates away from the rocker arm the outside drops, the inner end lifts and the valves spring closes it. In this way, the opening and closing of the valve is kept in sync with the rotation of the cam shaft, and thus with the movement of the pistons. Collectively, the cam lobe, follower, rocker arm, valve and valve spring are known as the valve train.
Ratio
Rocker arms have ratios -- the ratio is a measure of the arms leverage, which in turn determines how powerful the force is that it can transfer to the valve stem. The ratio is determined by the length of the arm, both between its center of rotation and the point it contacts the cam lobe, and between its center of rotation and the top of the valve stem. A typical automotive rocker arm has a 1:1.5 ratio, meaning that it moves the valve one and a half times further than the peak of the cam lobe projects up from the camshaft.
Problems
A tapping noise from the top end of the engine can indicate that insufficient lubrication oil is being delivered to the rocker arm. Most of the oil delivered to the top end of the engine is there to keep the camshaft area lubricated; much less is used for the rocker arms. Top end tapping is typically an early warning that an issue is developing with either the mechanical parts or with the lubrication system; prompt service is strongly recommended.
How to Use a Timing Light on a 91 Jeep
Ignition timing is vital to optimum engine performance. Over-advanced ignition timing causes premature ignition. Premature ignition is also known as "ping" or "spark knock" and can damage internal engine components. Pistons may become pitted or fractured by premature ignition. Retarded timing will pollute the engine crankcase with wasted fuel and may over-heat the engine. Fuel economy suffers in either instance and engine longevity is diminished. Timing lights provide an accurate indication allowing precise adjustment.
Instructions
Timing Checks and Adjustments
- 1
Park the Jeep on level ground. Place it in park if it has an automatic transmission or neutral if it has a manual transmissions. Set the parking brake and block the wheels from movement with chocks or similar devices. Open the hood and attach the timing light leads, or wires according to the light manufacturers instructions. Consult the emission control information label for specifications. It is affixed to the firewall on the passenger side. Attempt no adjustment if none is recommended.
2Highlight the timing mark on the crank pulley with white chalk. Locate and clean the numbered scale attached to the engine timing cover, just above the crank pulley. Make any disconnections specified on the emission control information label and start the engine. Allow the engine to reach operating temperature and normal idle speed.
3Assure idle speed is in range of specifications before adjusting ignition timing. Aim the timing light at the scale above the crank pulley, taking care to avoid moving parts.The crank pulley mark will appear stationary due to the stroboscopic effect created by the timing light. Observe the pulleys mark position on the scale and compare it to the value specified on the emission control information label. No adjustment is necessary if the mark and specification match.
4Make any needed adjustment by slightly loosening the distributor hold-down screw. Turn the distributor until the crank pulley mark aligns with the scales specified position. Use the timing light to observe position adjustment. Tighten the hold-down screw and turn off the engine. Restore any connections and remove the timing light. Test-drive the Jeep to evaluate any changes made.
Saturday, January 25, 2014
Tools For Rebuilding a Driveshaft

The driveshaft transfers power from the transmission to the differential in the back of rear- and four-wheel-drive vehicles. Rotation of the driveshaft allows for changes in suspension height. Located at the end of each driveshaft are flexible couplings, commonly erred to as U-joints. When rebuilding the drive shaft, you will generally need six tools: a U-joint pressing tool, socket set, vise, snap-ring pliers, brass punch and dial indicator.
U-Joint Pressing Tool
A pressing tool allows for easy removal of the U-joints, ensuring that other parts of the drive shaft do not become damaged. You can also find complete pressing kits. Generally, they include receiver tubes that catch the U-joint upon removal. When removing the U-joints, check for signs of damage or corrosion. Replace damaged U-joints to restore proper performance of your driveshaft. Failing to replace worn and damaged parts can cause the drive shaft to separate from the vehicle. Driveshaft separation from the car may cause an inability to control the vehicle, potentially resulting in an accident or damage to the vehicle.
Socket Set
Use a socket set to remove bolts on the driveshaft. Having a full range of sockets available will ensure that you have the right size socket for the job.
Vise
A vise allows you to secure parts while removing and installing the driveshaft, preventing you from dropping and damaging parts. It will also make removal and installation easier by securing oily parts.
Snap Ring Pliers
Snap ring pliers allow you to remove the clips on the cap of the driveshaft. Using the proper tools can prevent injury and damage to parts.
Brass punch
Use a brass punch to remove the bearing caps. Gently tapping on the bearing caps with a brass punch and hammer can help dislodge the snap rings. Because brass is a soft material, the use of a brass punch will prevent sparking and damage to the bearing caps.
Dial Indicator
Use a dial indicator to measure driveshaft runout. Check the manufacturers recommendations to find the acceptable driveshaft runout for your vehicle. A runout amount higher than the manufacturers recommendations will indicate that the driveshaft requires replacement. Check the driveshaft periodically to ensure safety while operating the vehicle. Early warning signs that the driveshaft may require replacement include a noticeable vibration in the steering wheel during driving and grinding or knocking sounds while turning.
How to Repair Rust Damage to Cylinders
Cylinders are part of a car engine. Pistons slide up and down inside the cylinders, so clean cylinders help your car engine run smoothly. A car is also more powerful with more cylinders in the engine. Rust builds on the walls of a cylinder over time, especially if the engine has been removed from your car. Rust causes the pistons to grind against the cylinder walls, damaging the efficiency of your car engine. The method you should use to repair your cylinders depends on the amount of rust on the cylinder walls.
Instructions
- 1
Rub the rust on your cylinder with steel wool, if there is only a small amount of rust on the walls. Scrub the cylinder walls with your steel wool, occasionally washing the wool in warm water to get rid of any excess rust.
2Fix your flex hone drill attachment to the end of your power drill. A flex hone attachment consists of a wheel covered in metal balls, and you can use it to remove a large amount of rust. You can buy one at an auto parts store.
3Put on your protective goggles. Turn on your power drill and gently run the flex hone over the rust on your cylinder walls. The flex hone will scrape off the rust and clean your cylinders. Oil your flex hone regularly to prevent damage to the metal balls. When you have removed all the rust, clean the walls of your cylinders using a rag.
Friday, January 24, 2014
How to Repair a Side View Mirror on a Pontiac G6
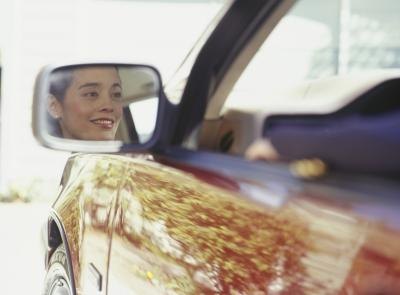
The Pontiac G6 is a standard midsized four-door sedan that uses standard plastic enclosures to mount the side view mirrors onto the door frames. This is the same process that GM has used since transitioning from metal mirrors that bolt onto the side of the door. Since the mirror inside of the enclosure attaches with a few metal clips, removing the side view mirror from the enclosure is a relatively simple process to complete.
Instructions
- 1
Push one side of the mirror into the enclosure to push the other end of the mirror out. If you are repairing the driver mirror, push the right side of the mirror into the enclosure. If you are repairing the passenger mirror, push the left side of the mirror into the enclosure.
2Slide your hand behind the mirrors edge and pull out on the mirror to force the metal clips to pop off the plastic ball on which the mirror pivots.
3Place the new mirror inside of the enclosure and press the tabs around the plastic pivot ball by pushing on the center of the mirror with the ball of your fist.
Why Is Road Salt Bad for Cars

While driving on slippery roads, drivers usually arent thinking about the decreasing value of their vehicle. Although road salt helps to increase the traction an automobile gets on wintry or wet roads, it can cause significant problems for a vehicle. However, car owners can use a variety of methods to decrease the effects road salt has on their car.
Paint Erosion
One common problem caused by road salt is car paint erosion. Although this may not happen over night, continued interaction with road salt can destroy the paint on a car over time. Modern automotive paint is better than it was decades ago; and improved primers and corrosion-resistant coatings decrease the impact road salt has on vehicles. Even with better paint, owners and their vehicles fall victim to the winter road warrior otherwise known as road salt. After a few winters, drivers may find they need a new paint job.
Corrosion
Another more serious problem caused by road salt is rusting. Although the paint serves as a protective layer for the metal of a vehicle, other areas of exposed metal, such as underneath the car, become victims of road salt. Over time, road salt can even eat through the vehicles paint and get to the metal underneath. Even though rust is not usually a safety factor, it can be quite expensive to fix. Once rust forms, it usually spreads. Because of this, its best to deal with rust before it occurs.
Structural Damage
What makes structural damage so severe and dangerous is that it occurs out of sight. Sometimes, the paint of a vehicle appears normal, but road salt has begun to eat away at the undercarriage of the vehicle. The undercarriage is at the highest risk level for road salt damage because it is constantly exposed to road salt -- being so close to the road -- and it does not feature a protective layer of paint, unless specially added. Structural damage, such as severe rusting, can be very expensive to fix and can cause safety hazards.
Prevention
The best way to prevent road salt damage is to wash the vehicle frequently. Washing a vehicle can remove salt from out-of-sight places. The undercarriage is especially important to wash because of frequent salt build-up. Parking a vehicle in a warm place, where the ice melts, can accelerate the damage caused by salt. To help prevent damage from road salt, a driver should wash her car about once a week. Waxing the car before winter comes will add a layer of protection as well.
Thursday, January 23, 2014
How to Repair the Radio on a 1994 3000GT
The main stereo on a 1994 Mitsubishi 3000GT coupe includes an integrated CD player, as well as in internal amplifier. This radio unit sits in the center of the dashboard and connects to a number of cables, including the speaker outputs, radio antenna and system wiring harness. The radio itself is held in place with a number of screws that connect to steel brackets. In order to access the radio retaining screws, the plastic outer bezel must be caully removed from the center of the dashboard.
Instructions
Removal
- 1
Locate your radios security code. This code is normally on a card in your owners manual. If you cant find it, youll need to get a new code from a Mitsubishi dealership near you.
2Open the hood and disconnect the 3000GTs negative battery cable from the battery with a battery terminal wrench.
3Sit in the passenger side seat. Insert a flat-head screwdriver in between the radio panel bezel and the radio. Pry around radio panel bezel until it pops loose, then remove it.
4Remove the screws on both sides of the radio holding the radio unit to the retaining brackets with a screwdriver.
5Pull the radio out of the vehicle and disconnect the electrical connectors on the back of the radio, then remove it from the vehicle.
Installation:
- 6
Reinstall the radios electrical connectors and make sure they are firmly connected.
7Put the radio back into the radio cage and reinstall the radio screws.
8Set the radio bezel into position and press down on it so it clicks into position.
9Reconnect the radios battery, then turn on the ignition. Press the power button on the radio, then use numbers one through four on the radio face to enter your security code.
10Press the PROG button when youve entered your security code. The radio should beep once and then operate normally.
How to Change Six Liter Power Stroke Injectors
The Power Stroke is a turbocharged diesel engine that Ford began making in 1994. The 6.0-liter version of this engine entered production in 2003, and it was the primary engine in Ford Super Duty trucks until 2008. The engine uses fuel injection to deliver specific amounts of fuel to each cylinder in a precise sequence. The fuel injectors in a 6.0-liter Power Stroke engine are part of the oil rail assembly, which you must remove to access the injectors.
Instructions
- 1
Disconnect the valve cover with a socket wrench. Unplug the electrical connector from the fuel injector.
2Remove the crankcase-to-head tube assembly with a socket wrench. Disconnect the bolts that attach the oil rail to the engine and remove the oil rail. Extract the fuel injector electrical connector from the rocker arm carrier with a suitable pry tool.
3Insert shop rags into the oil drain holes in the crankcase. Remove the bolt for the fuel injector with a socket wrench and disconnect the hold-down clamp from the fuel injector. Remove the fuel injectors from the oil rail assembly with a Snap-On SDMT440 Torx or similar tool. This is necessary to avoid damaging the plastic portion of the fuel injector. Pull the shop rags from the oil drain holes.
4Mount new copper washers and O-rings to the new fuel injectors and coat the fuel injectors liberally with engine oil. Install the fuel injectors on the oil fuel rail and connect the hold-down clamps. Tighten the mounting bolt for the fuel injector to 24 foot-pounds, using a torque wrench.
5Install the electrical connector for the fuel injector to the rocker arm carrier with a pry tool. Apply engine oil to the fuel injector to lubricate its top O-rings.
6Mount the oil rail on top of its carrier. Insert a guide bolt on each end of the straight side of the oil rail, then insert a third guide bolt in the middle of the oil rails wavy side. Press the oil rail into position so that its mounting feet are flush against the oil rails mounting surface.
7Install mounting bolts in the six remaining holes of the oil rail and replace the three guide bolts with mounting bolts. Tighten all of the mounting bolts to 10 foot-pounds, using a torque wrench.
8Install the crankcase-to-head tube assembly. Tighten the bolts for the crankcase-to-head assembly to 60 foot-pounds, using a torque wrench. Plug the electrical connectors into the fuel injectors. Replace the valve cover with a socket wrench.
Wednesday, January 22, 2014
How to Replace a Drive Belt on a 1998 Cavalier
The engine accessories on the 1998 Chevrolet Cavalier are driven by a single accessory belt. The belt is designed to operate the power steering pump, alternator, air conditioner and the water pump by traveling around all of the accessory pulleys at the same time. The ribs on the inside of the accessory belt travel inside of the grooves of each accessory pulley. This allows the belt to turn the accessory pulleys easier. Change the belt out if there are any visible signs of wear, fraying or cracking.
Instructions
- 1
Inspect the top of the plastic shield that covers the radiator for the accessory belt routing diagram. Install the new belt by following the routing directions from this diagram.
2Locate the self-adjusting belt tensioner on the front left-hand side of the motor. The tensioner has an idler pulley attached to the end of the tensioner arm. Rotate the entire tensioner device from the metric bolt in the middle of the tensioner pulley.
3Rotate the tensioner device in a clockwise motion with a breaker bar and a socket. Pull the belt off of the top of the tensioner pulley. Release the tension from the breaker bar, and let the tensioner retract until it stops.
4Remove the single belt out from around all of the accessory pulleys. Pull the belt over each fan blade and out of the engine well.
5Slide the new belt over each fan blade and into each of the accessory pulley as directed by the belt routing diagram.
6Rotate the tensioner in a clockwise motion with the breaker bar and socket again. Pull the belt over the top of the tensioner pulley, and release the tension from the breaker bar until the tensioner stops retracting against the belt. Remove the breaker bar from the tensioner pulley.
7Crank the motor up and let it run for around 15 seconds to seat the ribs of the belt to the grooves of each pulley. Turn the motor off.
How to Remove a Battery in a Chrysler 300M

Car batteries provide the electric current to start the engine and power the electrical appliances in the car. The battery in a Chrysler 300M is located under the right, front fender, in front of the wheel. The car battery must be replaced, periodically, to ensure the electrical systems continue to operate properly. The owner can remove the battery, but he must take special precautions, to ensure it is done correctly and safely.
Instructions
- 1
Put on protective gloves, and open the hood. Disconnect the negative battery cable from the negative battery cable booster post. Use a socket wrench to unscrew the retaining bolt, and secure it, away from the post. Loosen the air intake duct hose clamp, using a socket wrench, and pull it away from the housing. Unhook the latches attaching the air filter cover to its housing, using your hands. Lift the cover and air filter out of the vehicle. Lift the air filter housing upwards and away from the inner wall, and place it outside the car.
2Unscrew the two bolts located under the air filter housing, which hold the battery hold-down clamp, using a socket wrench. Remove the clamp.
3Raise the front, right side of the car, using a jack. Use jack stands underneath the front frame for support.
4Remove the front, right wheel. Unscrew the nuts, using a lug wrench. Take the wheel off the car.
5Remove the five screws, securing the battery cover to the inner fender wall, and remove the cover. Slide the battery towards the rear of the vehicle, so the battery terminals become accessible. Loosen the negative battery cable retaining bolt with a socket wrench. Repeat this process on the positive cable bolt. Pull the clamps off the battery terminals.
6Remove the battery from the 300M.
Tuesday, January 21, 2014
How to Get 1994 Mercury Sable Engine Codes
You can get the engine codes from your 1994 Mercury Sable right from home using an OBD I scan tool. This tool can be found at any auto parts retailer. When you see the "Check Engine" light illuminate on your instrument cluster, this is an indication that an error code has been sent to the vehicles On-Board Diagnostics computer. Never ignore a "Check Engine" light, or you may risk further damage to your vehicle. This same scan tool can also be used to reset the computer, and turn off the warning light after you have retrieved the codes and made the repairs.
Instructions
- 1
Plug the OBD I scan tool into the diagnostic port under the steering column just to the left side of the fuse panel. Check to see that the connection is tight and secure, but dont force the cable into the port, or you may risk damaging the pins.
2Put the key into the ignition, and turn it to the "On" position. Wait for the scan tool to interface with the computer, and then display "OK" on the face of the tool.
3Turn off the ignition, and unplug the tool.
4Locate the "menu" on the OBD I scan tool, and scroll through it to find the "Stored Engine Codes" command. Select this, and write down the codes that the tool stored. Look up the codes on the scan tools manual.
Repairing Installing Pontiac Sunfire Fuel Injectors
The Pontiac Sunfire is a compact car, manufactured by Pontiac from 1995 to 2005. This vehicle uses Pontiacs J platform, and has a four-cylinder 2.2-liter engine with sequential fuel injection. Each cylinder has its own fuel injector, which delivers pressurized fuel to the cylinder in a precise sequence. The fuel injectors are generally not serviceable, so the repair procedure consists of replacing the faulty injectors.
Instructions
- 1
Disconnect the cable from the negative battery terminal with a socket wrench to avoid the discharge of fuel while installing the fuel injectors. Open the filler cap on the fuel tank to relieve the pressure in the fuel tank.
2Wrap a shop towel around the fuel pressure port on the fuel rail to soak up fuel leaks. Connect a fuel pressure gauge to the fuel pressure port and place the free end of the pressure gauges bleed hose into a gasoline container. Open the valve on the pressure gauge to relieve the pressure in the fuel system. Disconnect the fuel pressure gauge from the fuel pressure port.
3Disconnect the outlet resonator of the air cleaner with a socket wrench. Detach the fuel lines from the fuel rail and unplug the electrical connectors for the fuel injectors. Disconnect the mounting bolts for the fuel rail and remove the fuel rail from the cylinder heads.
4Release the retainer clip on the fuel injectors and remove the fuel injectors from the fuel rail. Remove the O-rings from the fuel injector and discard them.
5Mount the new O-rings to the fuel injectors and attach the fuel injector clips. Install the fuel injectors into their corresponding sockets on the fuel rail so the electrical connectors face upward.
6Align the fuel injectors with their respective cylinder head ports and install the fuel rail to the cylinder heads. Tighten the retainers for the fuel rail to 89 inch-pounds with a torque wrench.
7Attach the electrical connectors to the fuel injectors. Connect the fuel lines to the fuel rail and connect the vacuum hose to the fuel pressure regulator. Install the outlet resonator for the air cleaner with a socket wrench.
8Connect the cable to the negative battery terminal. Turn the ignition on for two seconds to pressurize the fuel system. Turn the ignition off and check for fuel leaks.
Monday, January 20, 2014
How to Replace an LT1 Exhaust System
The LT1 is an engine designed and built by General Motors. It was fitted into several of GMs production vehicles. Due to its power output, the motor was used extensively on GMs high-performance sports cars. The exhaust system mated to the LT1 is suitable for the engine, but many LT1 owners want a freer flowing exhaust system to increase horsepower even more. To do this, youll need to replace the LT1s exhaust system.
Instructions
- 1
Raise the vehicle onto jack stands. Lift up on the front and rear jack points located on the front and rear crossmember. Place a jack stand underneath each of the pinch welds in each corner of the vehicle and lower the vehicle onto the jack stands. Youll need to work on one end of the car at a time (raise the front of the car on jack stands, then raise the rear).
2Place another set of jack stands underneath the exhaust system directly under the exhaust piping.
3Remove the bolts that connect the exhaust piping to the manifold at the engine.
4Remove the electrical leads running to the O2 sensors on the exhaust piping.
5Slide the exhaust piping off the rubber hangers on the underside of the vehicle.
6Install the new exhaust. Installation is the reverse of removal. Make sure that the exhaust piping sits securely onto the rubber hangers on the underside of the vehicle before bolting the piping to the manifold and reconnecting the O2 sensor wiring for the new exhaust.
How to Repair a Keyless Entry Fob

Keyless entry is one of those things that is taken for granted, until it doesnt work. Those tiny key fobs are complex electronic devices. Theyre dropped. They get wet. Theyre even scratched by the very keys they hold. When they stop working, its inconvenient. Replacing the key fob can be very expensive. Most cars require their own model key fob that must be purchased from the dealer. Repairing a key fob can save a lot of money.
Instructions
- 1
Open the key fob. Look carefully at the seam between the two halves of the key fob. There will be a slight indentation. Slip a screw driver into this notch and gently pry the two sides apart.
2Pull out the battery. Remote keyless entry fobs use a button type battery. Take the battery to a jeweler or battery store and have it checked. In many cases, simply replacing the battery will repair the remote.
3Clean the interior mechanism. Kept in a pocket or purse, many key fobs accumulate dust, dirt and lint. Gently blow any debris from the interior of the key fob.
4Glue any loose pieces of the plastic cover. Use a cyanoacrylate glue such as crazy glue or super glue. These bond the plastic instantly. Wipe any glue that may have spread to the edges. Allow the glue to completely dry before fitting both sides of the key fob together.
Sunday, January 19, 2014
How to Calculate Engine Power in the Metric System

Nearly every car commercial boasts about the car engines horsepower. But for people outside the U.S., or with a scientific background but not a car background, it may be unclear how much power a horsepower truly is. One horsepower is defined as 33,000 lb*ft/min (pounds times feet divided by minutes). So, converting horsepower into the metric system is simply a matter of converting the separate units of force, distance and time to arrive at a value in Nm/s (Newtons times meters divided by seconds), also known as Watts.
Instructions
- 1
Convert pounds to Newtons using the conversion factor 4.448 N/lb. If we take the original figure of 33,000 lb*ft/min and multiply by 4.448 N/lb, we get 146,784 N*ft/min.
2Convert feet to meters using the conversion factor 0.3048 m/ft. If we multiply this by 146,784 N*ft/min (our figure from step 1), we get 44,740 N*m/min.
3Convert minutes to seconds using the obvious conversion factor 60 s/min. Because minutes is in the denominator of our figure, we must divide the figure by this conversion factor to get the minutes to cancel out. 44,740 N*m/min divided by 60 s/min yields 745.7 N*m/s, or 745.7 W.
4Calculate the metric power of an engine from its horsepower rating using this figure. Since we know that 1 horsepower = 745.7 W, we can simply multiply the horsepower of an engine by 745.7 to arrive at a value in Watts. For example, a 300 horsepower engine puts out 300 * 745.7 = 223,700 W, or 223.7 kW.
How to Replace an Alternator in a 1992 SC400

The alternator is the part of the car the keeps your battery charged. Without an alternator, your battery would quickly lose its charge, rendering your car useless. If your battery is no longer holding a charge and you need a jump every time you start your car, it is time to change your alternator. Replacing an alternator is a relatively simple procedure that will save you some money if you choose to do it yourself. Replacing the alternator on your 1992 SC400 Lexus is a straightforward process that you can perform at home.
Instructions
- 1
Park your car on a level surface and pop open the hood. Disconnect the batterys negative terminal before you begin to work on the alternator.
2Loosen and remove the two mounting bolts that hold the alternator in place. Rotate the alternator toward the v-belt to create enough slack to remove it. Remove the v-belt and check it for wear. If it has considerable wear, now would be a good time to replace it.
3Remove the electrical wires connected to the back of the alternator and mark the alternator with a pen or marker to map exactly where each wire needs to be re-connected on the new alternator.
4Remove the alternator and compare it to your new alternator verify that everything is the same. Replace the new alternator in the reverse order that you took the old one out. Check the belt tension, when replacing the v-belt on the alternator. A little under an inch of deflection is what youre looking for---it is always better to have a slightly loose belt than a belt that is too tight.
5Take your car for a test drive of at least 15 miles, and then allow it to rest. Check it a few hours later or the next day to make sure your battery is now holding a charge and you no longer need to jump start your car.
Saturday, January 18, 2014
How to Install a Fuel Injector on a Concorde
The Chrysler Concorde was a full-size sedan that Chrysler produced from 1993 to 2004. It was available with a 2.7-liter or a 3.5-liter engine, both with multi-point fuel injection. This design uses an electronically-controlled fuel injector to send fuel to each cylinder at the correct point in the cylinders combustion cycle. The procedure for installing a fuel injector is similar for both of the Concordes engines.
Instructions
- 1
Disconnect the fuel pump relay from the power distribution center in the engine compartment. Start the engine and allow it to stall. Continue to crank the engine until it no longer starts. Turn the ignition off, and replace the fuel pump relay.
2Remove the cable from the negative battery terminal with a socket wrench to prevent the battery from producing sparks. Disconnect the plenum for the intake manifold, and cover the opening to the intake manifold with a clean shop cloth. Put a shop cloth under the quick-connect fittings on the fuel line, and squeeze the quick-connect fittings together. Detach the fuel line from the fuel rail.
3Disconnect the electrical connectors from the fuel injectors. Remove the mounting bolts for the fuel rail with a socket wrench, and remove the fuel rail from the engine. Release the retainer clips on the fuel injectors, and detach the fuel injectors from the fuel rail.
4Coat the O-rings on the new fuel injectors with engine oil, and install the fuel injectors to the fuel rail. Secure the fuel injectors with the retaining clips. Press the fuel rail into place on the cylinder head, ensuring that the fuel rail is fully seated.
5Tighten the mounting bolts for the fuel rail to 100 inch-pounds with a torque wrench if you have a 2.7-liter engine. Tighten the mounting bolts to 21 foot-pounds if you have a 3.5-liter engine.
6Remove the shop cloth from the opening of the intake manifold, and connect the plenum for the intake manifold with a socket wrench. Coat the quick-connect fittings on the fuel line with engine oil and connect the fuel line to the fuel rail. Attach the cable to the negative battery terminal.
How to Pull a Code on a 1993 Mustang

You can pull a trouble code from your 93 Ford Mustang right from your home garage using an OBD I code reader. The Mustang comes equipped with an on-board diagnostics computer that receives and stores trouble codes sent to it from various sensors positioned throughout the vehicle. When one of these sensors detects a malfunction, it sends an alphanumeric code to the computer. The computer, in turn, will illuminate a warning or service light on the instrument panel to alert you. You can purchase an OBD I code reader from any auto parts retailer.
Instructions
- 1
Locate the diagnostic port on the drivers side dash under the steering column. It is the same size and shape as the connector on the code reader. Plug the code reader into this port. Rotate it a bit to make it fit if necessary.
2Put the key into the ignition and turn it to the "on" position but dont crank the engine. This should power on most code readers. If not, locate the "on/off" switch on the code reader and turn it "on."
3Wait while the OBD I code reader retrieves all the trouble codes. Write them down on a piece of paper and look up their meanings in the code readers manual.
4Turn off the code reader, if necessary, and unplug the reader from the port. Turn off the vehicle.
Friday, January 17, 2014
Problem With Tundra Marker Lights Not Turning Off

The 2004 Toyota Tundra has had a number of recalls. One such recall is for the Tundra marker lights. A marker light is a blinking light that is produced to indicate the direction the driver is taking; its also known as a turn signal or indicator light. If your Tundras marker lights are constantly blinking, you may have a faulty blinker fuse or light bulb.
Instructions
- 1
Insert the key into the ignition and turn it clockwise to the "On" position, but do not start the engine.
2Test the blinker system by inspecting the fuse panel. Look under the cars dashboard, which is located just below the drivers knee. Youll see the fuse box. Locate the tap on the fuse box cover and lift it up to snap the cover off. Remove the cover. On the underside of the cover is a chart that explains each fuse control.
3Inspect the blinker flasher. Connect a jumper wire to two slots at the top of the fuse panel. Switch the blinker lever to the "Off" position. If the blinkers are still going, you may have a faulty fuse that will need to be replaced.
4Turn off the Tundra and remove the key. Remove the marker light covers and replace the bulbs. Unscrew the cover and twist off the bulb. Insert another bulb into the housing and screw it in tightly. Insert the key into the ignition. If the lights continue to blink, youll have to turn to a mechanic to repair the fuse box.
How to Measure Chevy Bolt Patterns
The Chevrolet Motor Company introduced its first vehicle to consumers in 1912. Later merged with General Motors, Chevrolet produces many wheel styles and sizes for its vehicles. Determining the wheel bolt pattern size for your vehicle will enable you to purchase the correct equipment or aftermarket replacements.
Instructions
- 1
Remove one of your vehicles wheel covers (if equipped) to gain access to the lug studs. Certain original factory wheel covers use faux plastic lug nut covers that secure the hub cap to the rim; you must use an appropriate size lug wrench to loosen the plastic lug nut covers in order to separate the hubcap from the rim. Certain wheel cover styles may require you to pry along the outside parameter, between the rim and hub cap, for proper removal.
2Count the number of lug bolts that secure the wheel to the vehicle.
3Measure the distance between the middle of one lug stud to the middle point of the stud directly across when dealing with four-, six- and eight-lug applications. For five-lug vehicles, measure from the outside edge of one stud to the middle point of the farthest stud across.
4Note the measurement in both metric (millimeters) and American standard (inches). A wheel with five lug studs and a measurement of 4.5 inches translates as a 5-by-4.5-inch or 5-by-114.3-inch bolt pattern when converted to millimeters.
5Reinstall the wheel cover after obtaining the correct measurements, if necessary.
Thursday, January 16, 2014
How to Change the Headlights of a 1996 Toyota Camry

The 1996 Toyota Camry has four headlights. One low beam and one high beam sit side-by-side on both sides of the car. The low beams are positioned in the outer corners of the headlight assembly while the high beam sit in the inner corners. The low and high beams have different part numbers (despite looking identical), since they perform different functions. Make sure to insert the correct bulbs in the correct positions.
Instructions
- 1
Apply the parking brake on the Toyota Camry, ensure the headlight switch is off and open the hood.
2Reach behind the headlight lens assembly and locate the separate wire harness plugs for the low and high beams.
3Disconnect the wire harness plug from the socket base of the headlight being replaced. The plugs have a locking clip that snaps over a small tab on the headlight sockets. Lift the clip up and pull the plug from the headlight socket.
4Turn the headlight retainer ring counterclockwise 1/3 of a turn and extract the headlight and ring from the back of the headlight lens assembly. Discard the faulty headlight.
5Put on a pair of latex gloves to avoid accidentally touching the glass bulb of the headlight. Halogen headlights use an internal gas to burn brighter, and skin oils will damage the glass.
6Insert the collar of the headlight socket into the retainer ring and align the tabs on the socket to the notches in the headlight lens assembly.
7Turn the ring and socket clockwise 1/3 turn until they lock in place.
8Connect the wire harness plug to the headlight socket until it clicks into the locked position.
9Test the headlight(s) for proper operation.
How to Intall Shocks on a Sportster

Sportster shocks are usually 13.5 inches long. Installing shorter shock absorbers will slightly affect the part of motorcycle frame geometry called "trail." Trail is the ratio of the distance from the axle to the ground on the back of the bike and the distance from the center of the steering neck to the ground on the front of the bike. Radical trail is one reason why the most extreme looking custom bikes usually dont handle well. You should be aware of frame geometry if you replace your Sportster shocks with longer or shorter ones. Installing new shocks is a very simple job.
Instructions
- 1
Remove any accessories, like saddlebags, that limit access to the shock absorbers. Raise the Sportster on a motorcycle jack just high enough so the bike is upright and not leaning left on the support stand.
2Remove the lower shock mounting screw, washer and nut from the old, right shock absorber. Remove recent Harley shocks with an Allen wrench and older or non-Harley shocks with socket wrench and hex socket. Save the hardware for reuse.
3Remove the upper shock mounting screw, washer and nut from the old, right shock absorber and save the hardware. Remove the left shock absorber the same way you removed the right one.
4Paint the mounting screw threads with thread locker and bolt the new shock absorbers to the Sportster using the original hardware. Tighten the mounting bolts to 50 ft.-lbs. of torque with an Allen or hex socket and a torque wrench.
5Lower and remove the jack. Sit on the bike, bounce up and down and check for binding.
6Reinstall any accessories.
Wednesday, January 15, 2014
How to Get the Smoker Smell Out of My Car

If you or a family member smokes or if youve purchased a used car owned by a smoker, it is likely youll need to air out the car to remove the smoker smell. In some cases, simply airing out the car will not remove the deeply embedded smoke smell. Instead, youll have to use common household products to remove the smell from the upholstery and hard surfaces.
Instructions
- 1
Vacuum the car thoroughly with the upholstery attachment of your hose vacuum. Vacuum the seats, dashboard and trunk. Pull out the rugs and vacuum them. Vacuum the floors and under the seats. This will ensure youve removed all of the ash or any cigarette butts.
2Dampen a clean cloth with white vinegar and rub it over the dashboard and the hard surfaces inside the car. This will help neutralize the smell. It may leave a pungent vinegar odor that will dissipate.
3Sprinkle baking soda over all of the surfaces. Leave the baking soda on the surfaces for several hours to give it time to absorb the smoke smell. Vacuum up the baking soda when it has absorbed the smell.
4Pour white vinegar into a bowl and put it inside the car if the smell is remains noticeable. Roll up the windows and shut all of the doors. Leave the vinegar in the car overnight. The vinegar will help neutralize the smell.
5Place a bowl full of charcoal if the smell remains. Roll up the windows and shut the door. Leave the car alone for at least one day before removing the charcoal. The charcoal will neutralize the smell and absorb some of it.
How to Stop a Car From Backfiring
Backfiring is a common problem and can be a symptom of issues you need to address. The loud bursts of noise that come out of your exhaust pipe could be a sign that theres something seriously wrong with your car. Ruling out common causes of backfire can help you diagnose your problem. Unfortunately, there are many causes and solutions, and it could take several hours to fix the problem.
Instructions
- 1
Examine your carburetor. The carburetor is the device that regulates airflow into your engine. This facilitates the controlled gas explosions that keep your car cruising along. Balance and tune the carburetor to ensure the air and gas mixture is properly balanced. The backfire may be your cars way of telling you that its not getting enough air in its fuel mixture. You may also be able to prime the carburetor to fix it if it hasnt been used in quite some time.
2Check the distributor cap. If it is cracked or broken in any way, it can easily backfire. Be sure to look very closely. Even a hairline crack can cause a car to backfire.
3Evaluate your spark plugs. These provide the spark that ignites the air and gas mixture. If they are dirty, backfiring may be a symptom of an underpowered car. Remove the plugs with a wrench and make sure the pins are the right distance from the base of the plug. There may also be small bits of dirt in the plug that could cause a problem.
4Inspect the integrity of the gaskets in your engine. These gaskets keep the proper gases in and the unneeded gases out. If these are compromised, they could cause backfire.
Tuesday, January 14, 2014
How do I Decode a Jeep ID

Each Jeep vehicle has a unique vehicle identification number, or VIN, that describes details such as the type of restraint system and model year. VINs consist of 17 letters and numbers and are useful if you need to order parts or get an insurance quote. You can use a decoding template to learn what each character means.
Instructions
- 1
The first three characters represent the World Manufacture Identification, or WMI. For Jeeps, the first character is "1" for "United States," the second is "J" for "Jeep" and the third could be a letter or number indicating the type of vehicle. This third character will vary based on the type of Jeep.
2Character four represent the gross vehicle weight for some Jeeps and the engine type for others. Look at the Jeep Fan website to verify what applies to your specific vehicle.
3View characters five and six to find out the car line series. For instance, character five could be "J" for Cherokee four-wheel drive and character six could be "2" for "Base."
4Character seven represents the body style such as "7" for "two-door sport utility."
5Check character eight to find out the engine type for newer model Jeeps or trim package type for older Jeeps. Use the Jeep Fan website as a cross reference.
6Jeep assigns character nine as a check character to verify the authenticity of the VIN.
7Characters 10 and 11 identify the model year and assembly plant, respectively.
8Characters 12 through 17 represent the production sequence number.
How to Raise the Rev Limiter on My Harley Davidson

Although the parameter is commonly called the rev limiter, it is more accurately called the rpm limit, and it is a function of the electronic ignition. A stock Harley-Davidson has a limit of 5,500 revolutions per minute. Usually, on a Big Twin, about the time you hit 60 or 65 miles per hour in second gear, the engine will begin to sputter and miss. Crusty old bikers who remember mechanical points will mutter about "hitting the rev limiter," but there is no rev limiter. You change the rpm limit by installing an electronic ignition with a programmable rpm limit. Crane makes ignitions with rev limits that can be set as high as 9,900 rpm.
Instructions
Remove Old Ignition
- 1
Remove the seat by loosening the Allen or Phillips screw in the fender tab on the back of the seat with an Allen wrench or a Phillips screwdriver.
2Disconnect the negative battery terminal from the negative battery post with an open-end wrench.
3Disconnect the spark plug wires from the coil. Remove the two remaining wires, positive and negative, from the front of the coil with a small open-end wrench.
4Disconnect the plug -- called the VOES connector -- that attaches the wiring harness of the vacuum operated electrical switch to the front wiring harness.
5Drill out the two rivets on the "points cover" on the lower right side of the motorcycle with an electric drill. Remove the points cover.
6Loosen the two flat-head screws inside the points cover. Remove the inner cover and gasket.
7Disconnect the sensor plate cable plug with needle-nose pliers. Pull the sensor plate cable through the hole at the bottom of the timing cover.
8Draw a line from the V-notch on the sensor plate to the ignition housing, using a grease pencil.
9Remove the two sensor plate screws and washers with a flat-head screwdriver. Remove the sensor plate.
Install New Ignition
- 10
Install a Crane Hi-4 ignition or the equivalent in place of the sensor plate. Push the new ignition cable through the hole at the bottom of the timing cover.
11Align the V-notch on the Crane HI-4 ignition with the grease pencil mark on the ignition housing. Loosely attach the new ignition with the original sensor plate screws and the lock washers included with the ignition.
12Route the new ignition wiring harness along the frame rails to the coil. Secure the new harness to the frame with cable ties.
13Connect the black (positive) and white (negative) coil wires from the new ignition wiring harness to the positive and negative terminals on the coil, using a small open-end wrench. Reconnect the negative battery cable to the negative battery post with an open-end wrench.
14Replace the seat and fasten the seat tab to the rear fender with a Phillips screwdriver or an Allen wrench. Attach the green wire in the new ignition wiring harness to the VOES connector.
15Set the "mode select" dial on the new ignition to "6." Set the two rpm limiter switches to the desired setting. Set the "advance slope" dial to "6."
16Set the two rpm selector dials to the desired rpm limit, divided by 100. For example, you would achieve an rpm limit of 5,500 by setting both dials to "5." For an rpm limit of 6,800, you would set the first dial to "6" and the second dial to "8."
Static Timing New Ignition
- 17
Put the Harley in the top gear. Raise it on a motorcycle jack until the rear wheel is off the ground.
18Remove the front spark plug with a spark plug socket and a socket wrench. Peer into the spark plug hole.
19Rotate the rear wheel and the engine until the front cylinder is at the top of its stroke. Do not move the rear wheel.
20Remove the timing hole plug in the crankcase with a hex socket and socket wrench. Screw a timing view plug into the same hole in the crankcase.
21Confirm that a double line, which is the top dead center timing mark, is visible in the timing view plug.
22Turn on the ignition. Confirm that the LED on the new electronic ignition is illuminated.
23Rotate the new ignition module by hand until the LED goes out. Tighten the sensor plate screws with a flat-head screwdriver.
24Turn off the ignition. Reinstall the front spark plug.
25Lower the motorcycle jack and remove. Remove the timing view plug and reinstall the timing hole plug with a hex socket and a socket wrench.
26Reattach the points cover with the gasket included with the ignition kit. Secure the points cover to the ignition housing with the two self-threading screws included with the ignition, using a screwdriver.
Monday, January 13, 2014
How do I Change the Front Shock on 1999 Dodge Dakota

The front shocks on your 1999 Dodge Dakota should be replaced every 50,000 miles. The shocks attach to the axle and the frame of the vehicle. They are designed to dampen the bumps in the road to provide a smooth ride. Worn shocks can cause poor handling and increased tire wear. The front shocks for your Dodge Dakota can be purchased at auto parts stores and installed yourself with simple tools.
Instructions
- 1
Loosen the lug nuts off of each front tire with a tire iron wrench.
2Place a hydraulic jack under the axle near the tire. Lift the vehicle enough so the tire can be removed. Place a jack stand under the axle and lower the axle with the jack onto the jack stand. Repeat this step to the opposite end of the axle.
3Remove the lug nuts and pull the tires from the axle.
4Locate the mounting bolts that secure the shocks to the vehicle. Lubricate these bolts by spraying penetrating fluid onto them. Allow the fluid to lubricate the bolts for 10 minutes.
5Loosen and remove the bolts with a ratchet and socket. Remove the shock from the vehicle.
6Place the replacement shock into the brackets. Use the stock hardware to fasten the shock into position. Tighten the bolts with a ratchet and socket.
7Repeat steps 4 through 6 for shocks on the opposite side of the vehicle.
8Reinstall the tires and the lug nuts. Tighten the lug nuts with the tire iron wrench. Lift the vehicle and remove the jack stands before lowering it to the ground with the jack.
How to Disable the Airbag Warning Light in a PT Cruiser

When the airbag warning light or Supplemental Restraint System (SRS) light illuminates on the PT Cruisers instrument panel, it is because a trouble code is being sent to the On-Board Diagnostics (OBD) computer from a sensor in the SRS. Trouble codes are used to help you pinpoint and troubleshoot problems with your PT Cruiser. You can reset these trouble codes using an OBD scan tool after you have had the airbag system examined and repaired. This hand-held computerized device can be purchased from your dealership or any auto parts retailer.
Instructions
- 1
Locate the OBD port on the drivers side dashboard underneath the steering column.
2Insert the OBD scan tools connector into this port.
3Put the key into the ignition and turn it to the "Run" position. Dont allow the engine to start.
4Wait for the scan tool to interact with the OBD computer. When the codes display on the scan tool, find and select the "Delete Codes" command. The scan tool will return to the main menu or display "OK" when it has finished deleting the codes.
5Unplug the OBD scan tool and start the engine. Check to make sure that the SRS light has shut off on the instrument cluster.
Sunday, January 12, 2014
How to Reset the Airbags in a Nissan 350Z
Some models of the Nissan 350Z are equipped with driver and passenger side air bags that rely on sensors within the car to determine when they should be deployed. The internal computer system continuously tracks the state of the airbag sensors to make sure they are working properly. If the computer detects a potential problem with the airbag system, an airbag warning light is displayed. After the air bag system is inspected and it is determined it is functioning properly, the air bag system will need to be reset. In many cases, the light is on because the connection between the airbags and the computer has been interrupted and needs to be reestablished.
Instructions
- 1
Turn the ignition on. The airbag light will come on.
2Turn the ignition off as soon as the air bag light turns off.
3Repeat the above steps three additional times.
4Start the engine. The light will come on for about six seconds and then turn off, indicating the airbags have reset.
Tools to Remove a Front Axle on a Suzuki SV650S

The Suzuki SV650S is an extremely popular motorcycle and many do-it-yourself owners are interested in servicing their own bikes. As such, it sometimes is necessary to remove the front wheel and axle. This can be an easy undertaking with the right tools.
Removing Brake Caliper
The first step to removing the front axle is first to remove the brake caliper. This requires a metric socket set kit, in particular a 14-mm socket.
Axle Pinch Bolt
To loosen the axle pinch bolt on the front fork leg, a 12-mm metric socket is required. Once the pinch bolt is loosened, you can proceed to removing the axle.
Front Axle Removal
To remove the front axle, one first must loosen the front axle with a special tool (Suzuki code 0990Q-18710). This tool also is known as a hexagon bit 12-mm drive. After loosening, the wheel can be lifted off the ground and the front axle removed completely. A motorcycle jack, lift, stand or other device will be required to lift the motorcycle up off the front wheel.
Saturday, January 11, 2014
How to Replace the Car Keys for a 2007 Nissan Versa
The 2007 Nissan Versa came with two key options: A regular transponder-chipped key that opens the doors and starts the engine, or an Intelligent Key that allows you to open your car door or press the start button to turn the car on. Both types of keys can be replaced at a Nissan dealership. In addition, if you add extra car keys, you have to bring any keys you already have with you to be reprogrammed. Otherwise, the keys will not work again.
Instructions
- 1
Call your local Nissan dealer to make an appointment to come in with your vehicle or to find out if you can simply stop in during service department hours.
2Go to the Nissan USA website to locate a local dealer if you do not know the phone number. Under the "Shop & Locate" menu on the bottom of the page, choose the "Find a Dealer" option. Put in your zip code in the space provided and click the search option. Choose a dealer to call from the results page.
3Tell the service representative that you need to replace your keys. Go to the dealer with your keys at the appointed time, or drop by during business hours if you dont need an appointment.
4Tell the service department representative how many keys you want to purchase. You can add up to four Intelligent Keys or five chipped keys.
5Give all of your Versa keys to the service representative. Wait while the keys are set up for your car. Pay the service representative and make sure that all the keys work before you leave.
How to Replace the Battery in a Mazda Tribute 2005

Replacing the battery in a 2005 Mazda Tribute is a fairly standardized procedure. However, it may be helpful to use a computer memory saver device on vehicles made after the 2000 model year. These devices often save the preset stations and clock time, and they prevent the cars computer from being reset during the battery replacement. The 2005 Tribute features two engine choices: a 2.3-liter, four-cylinder motor or a 3.0-liter, six-cylinder engine.
Instructions
- 1
Place the 9-volt battery (if applicable) into the computer memory saver, and plug it into the cigarette lighter or power source for the 2005 Mazda Tribute. There are different types of memory saver devices for cars, and instructions vary.
2Turn off all power sources in the Tribute. Remove the key from the ignition. Open the hood.
3Locate the battery. In the 2005 Tribute, the battery is in the front of the engine compartment directly behind the drivers side headlight.
4Remove the nuts on the battery hold-down bracket located at the top of the Tributes battery by using the ratchet and a socket.
5Loosen the negative terminal clamp with the ratchet and a socket. The negative battery terminal clamp has a black wire running to the clamp and either the letters "NEG" or a minus sign stamped on the battery housing near the clamp. Use the channel locks on the terminal clamp once its loosened to wiggle the clamp back and forth and remove the clamp from the battery post. Repeat the procedure for the red-wire positive terminal clamp.
6Hoist the battery out of the engine compartment.
7Clean the battery terminals with the battery terminal cleaner and wire honing brush to remove any corrosion on the clamps.
8Insert the replacement battery into the tray. Align the posts with the appropriate side and clamp (negative post to negative cable and cl positive post to positive cable and clamp).
9Connect the red-wire positive terminal clamp to the positive battery post first. Tighten the clamp with the ratchet and a socket. Repeat for the negative battery terminal clamp and post.
10Spray the battery terminal clamps and post tops with battery corrosion protection solution.
11Remove all tools from the engine compartment. Close the hood.
12Unplug the computer memory saver from the power outlet. Disconnect the 9-volt battery from the memory saver (if applicable).
Friday, January 10, 2014
How to Replace a Toyota Oxygen Sensor
The oxygen (or O2) sensor on your Toyota helps balance the engines fuel-to-air ratio. A faulty O2 sensor can cause your engine light to come on. It might also prevent the vehicle from starting. Your Toyota is equipped with two O2 sensors. They are located underneath the vehicle on the exhaust pipe, with one on either side of the catalytic converter.
Instructions
- 1
Set the emergency brake.
2Jack up the front end of your Toyota. Put the jack stands in place.
3Slide under the vehicle with the socket set and locate the O2 sensor you will be replacing. Sensor 1 is located on the exhaust pipe, on the left hand side of the catalytic converter. Sensor 2 is located on the right hand side of the catalytic converter closest to the vehicles rear end.
4Loosen the two mounting bolts that hold the sensor to the exhaust pipe with your socket set.
5Unplug the sensor from its socket by squeezing in the two safety tabs on the sides of the socket and pulling the sensor free.
6Plug in the new O2 sensor. Re-mount it to the exhaust pipe with the mounting bolts.
7Remove the jack stands and lower your Toyota.
How to Open the Door to a 2002 Saturn With Locked Keys in the Car

Your 2002 Saturn is a nice car; unfortunately, you cant drive it at the moment because youve locked your keys inside it. The mechanics at a Florida Saturn dealership caution against attempting to retrieve them on your own. While you may have seen your parents use a wire or metal hanger at some point to unlock their own cars to retrieve locked-in keys, this technique may damage the inside of the door frame and is not highly recommended by Saturn. However, if you find yourself in this situation and need to retrieve your keys, exercise caution attempting to jimmy the lock of your 2002 Saturn with a wire hanger.
Instructions
- 1
Check all of your windows and doors to see if its your lucky day and one is down or unlocked. Your driver door might be locked, but one of the others might not have locked, making retrieving your keys very simple.
2Bend a wire hanger or similarly sized object to create a hook or triangle shaped handle.
3Push the hanger down in between the door frame and the window. As gently as possible, use the hanger to find the switch for the door lock. Late-model cars have more power equipment, so Saturn recommends exercising caution.
4Pull the hanger until you find the door lock and hear the locks click open.