Saturday, November 30, 2013
Would a Bad Torque Convertor Cause Vibration

A torque converter is a round object between the engine and transmission of automatic vehicles. It serves several purposes, such as giving an engine the ability to idle as well as increasing an engines torque. When a torque converter goes bad, there are a number of things that happen.
Noise
Noise coming from a vehicle transmission could be due to problems with the torque converter. A torque converter has needle bearings inside. When these bearings wear out, they can cause transmission noise unless the transmission is in neutral in which case the noise temporarily stops.
Vibration
Lockup torque converters were added to many newer-model vehicles to help with fuel economy. However, vibration problems can happen when these torque converters go bad. The vibration felt is known as "lockup shudder" and may occur due to a bad engine or transmission as well.
Overheating
Torque converters have a one-way clutch that can jam and prevent the converter from circulating fluid correctly. This can cause a vehicle to lose power at higher speeds such as those reached when traveling on the interstate. It can also cause an engine to overheat at cruising speeds.
How to Change the Shocks of a 1998 Toyota Tacoma 4 Wheel Drive

The 1998 Toyota Tacoma 4-wheel drive pickup comes equipped with four shock absorbers. The front shocks are part of a coil spring/shock absorber assembly. Separating the shock absorber from the coil spring requires special tools and is potentially dangerous. It is wise to replace the coil and shock as a single unit to avoid having to disassemble the unit. The rear shocks and coil springs are separate units, and you can replace the shocks without removing the springs.
Instructions
Front Shocks
- 1
Loosen the front wheel lug nuts with a lug wrench. Raise the front of the truck and support each front wheel with a jack stand. Remove the lug nuts and both front wheels from the truck.
2With a socket wrench, remove the nut and bolt from the lower end of the shock, where it attaches to the lower control arm. If the bolt is extremely tight, attach a cheater bar to the socket wrench to gain more mechanical advantage.
3Remove the three nuts from the top of the shock/coil assembly. These are the nuts around the top edge of the assembly. Do not remove the center nut.
4Pull the shock/coil assembly down off the vehicle.
5Place the new shock/coil assembly bolts up into the holes in the mounting bracket and replace the nuts without tightening them.
6Replace the bolt and nut on the lower end of the shock, where it connects to the lower control arm. Tighten the nut to 101 foot-pounds of torque.
7Tighten the three upper nuts to 47 foot-pounds of torque. Repeat the procedure on the opposite shock/coil assembly.
8Replace the wheels and lug nuts. Lower the truck and tighten the lug nuts.
Rear Shocks
- 9
Loosen the lug nuts on the rear wheels and raise the rear of the vehicle by placing a floor jack under the rear axle. There should be no weight on either wheel assembly.
10With a socket wrench, remove the mounting bolt from the upper end of the shock absorber, where it attaches to the frame.
11Remove the mounting bolt from the lower end of the shock absorber, where it attaches to the spring seat bracket. Pull the old shock off of the truck.
12Place the new shock absorber into position. Replace the lower mounting bolt and tighten it to 53 foot-pounds of torque.
13Replace the upper mounting bolt and tighten it to 53 foot-pounds of torque. Follow the same procedure to replace the opposite shock absorber.
14Replace the rear wheels and lug nuts. Lower the vehicle and tighten the lug nuts.
How to Remove a Cavalier Catalytic Converter
Removal of a catalytic converter is not a task for a novice. It requires the skill of a certified mechanic who is a trained and experienced welder as well as technician. Removing the catalytic converter requires dealing with highly flammable gasoline and a cutting torch that can cause severe burns and damage the eyes retina by way of welding flash. For a certified technician this is a relatively simple procedure involving dropping the gas tank, cutting the old converter out and welding in a new one. For the novice, this is an extremely dangerous procedure that should not be attempted.
Instructions
- 1
Remove the fuel filter housing located in the trunk under the carpet. Disconnect both wires going to the filter housing. Remove the filter with the housing and set aside.
2Remove as much fuel from the fuel tank as possible. If the vehicle has a drain plug, place a drip pan under the vehicle and remove the plug. Allow all the fuel to drain out of the tank. This does not make the tank completely safe, Gas fumes are the most explosive part of dealing with fuel. Draining the fuel makes the procedure safer but not completely safe.
3Remove the drip pan from under the car and discard the fuel in an OSHA approved container. Do not dump on the ground. Fines for this kind of disposal are large and are to be avoided. Replace the drain plug in the fuel tank and find the bolts holding the retaining straps on either side of the tank. Make sure you wear safety glasses throughout this procedure to prevent getting residual gas in your eyes. If you get gas in your eyes, flush with water for five minutes and seek medical help.
4Once you have located the bolts holding the retaining straps, use an open end box end wrench or ratchet and socket set to loosen the bolts. (if your vehicle needs to be raised to get under it, use a hydraulic jack and jack stands or a hydraulic car lift). Place a hydraulic jack rated the the gross weight of you vehicle in the center of the fuel tank.
5Remove the mount bolts and let the fuel tank rest on the jack. Slowly lower the tank and pull out from under the car with the hydraulic jack. Make sure the fuel tank is in an open air area of the shop so that the fumes can dissipate.
6Raise the vehicle and use a hydraulic jack and jack stands or a car lift (preferred), to raise the vehicle high enough that the welder can stand under the car. Measure the length of exhaust pipe coming out each end of the converter. Mark the exhaust line in the vehicle to match the measurement of the new converter.
How to Replace the Headlamps on a Honda Civic
Replacing a headlamp on a Honda Civic is necessary if the lenses become foggy, cracked or damaged. Effective headlamps are crucial for highway safety not only to yourself but to other drivers. Replacement can be done at home and generally within less than 30 minutes. There are two different types of Honda Civic headlamps to choose from: an all-in-one headlamp that comes as a whole unit with light bulb included, and a halogen type for light bulb replacement only.
Instructions
- 1
Secure your car by pulling up the emergency brake. Do not work on a downward slope for added safety.
2Open the hood of the car by releasing the hood latch located on the drivers side under the left side of the dash near the steering wheel. Secure the hood with the hood bar to prevent it from falling on you while you are working.
3Identify the metal band that is holding your headlamp into position and loosen the screws with your Phillips screwdriver. Place the screws into a small cup to prevent losing them.
4Remove the metal band and set to the side. Disconnect the light bulb plugs attached to the light bulbs within the headlamp.
5Pull back the rubber covering on the headlamp and remove the headlamp from the car.
6Reconnect the light bulb plugs to the new all-in-one headlamp and place into the open slot of your car. Reattach the rubber covering and the metal band. Reinsert the screws and turn on your lights to test them before closing the hood.
Friday, November 29, 2013
Can a 4 Cylinder Car Jump Start an 8 Cylinder Car

The battery in your 8-cylinder Cadillac is dead. A motoring Good Samaritan rolls up and offers you a jump start with his 4-cylinder Japanese import. What are the chances that the 4-cylinder car can start the Cadillac with 8-cylinders?
Background
Jump starting is not about cylinders; it is about power--power expressed in terms of voltage and the amount necessary to crank the engine of a disabled car.
Voltage and Power

A battery stores power as the engine runs and sends a trickle charge to the battery. The power to start a car is delivered by the stored power. If the 4-cylinder car battery is good, it will work.
Safe Jump Start
The jumper cables must be placed correctly for a safe jump start with both car engines off and emergency brakes set. Connect the red/+ cable to the red terminal of the dead battery. Connect the other end of that cable to the red terminal of the good battery. Connect one end of the black/- cable to the good battery. Connect the other end of this cable to a piece of unpainted metal in the engine compartment of the car with the dead battery. Do not connect it to the black battery terminal. Start the car with the good battery and rev the engine. Attempt to start the car with the dead battery. If it starts, remove the cables in the reverse order they were placed.
What Starts the Dead Engine?
Once the jumper cables are correctly in place, the 8-cylinder car is started using the voltage supplied by the engine of the 4-cylinder car. Once the 8-cylinder car is running smoothly and jumper cables are removed drive the car with the dead battery to recharge it. You may want to take it to a place where battery service is offered and have it checked.
How to Make an Accel Spark
Spark plugs are essential for your engine to run properly. If you are having problems with your spark plugs, you dont necessarily have to replace them; you can replace the Accel spark plug wires. This costs less than replacing your spark plugs, but you have to size them properly to your spark plug. You dont have to be a mechanic to replace the wires. You can do it yourself.
Instructions
- 1
Use your spark plug boot to remove the spark plug from the engine. The spark plug is labeled and located on the side of the engine.
2Pull your wire through the looms until you have access to the distributor cap.
3Put a mark on the wire about 3 inches from the distributor cap with your permanent marker. Use your wire cutters to cut the wire.
4Use the wire cutters to strip the wires about five-eighths of an inch from the spark plug wire and your replacement wire. Use wire nuts to connect the replacement wire with the existing wire.
5Crimp the wire nut to make sure the wire nut stays secure. Push the new wire into the distributor cap to complete the installation.
How to Stop Rust Corrosion

Rust is the process of corrosion of iron and iron alloys. When rust accumulates on an object, such as your car, it causes more than aesthetic damage. Corrosive rust buildup can lead to the overall integrity failure of the item, which can force costly repairs and even physical injury. Luckily, with proper care and upkeep, you can stop corrosive rusting.
Instructions
- 1
Clean your items frequently according to the methods best suited to the item. For example, wash and dry your car thoroughly whenever dirt and debris builds up on the car and undercarriage. By simply washing away dirt and debris, you help prevent the onset of corrosion.
2Apply a finishing product that is specifically designed for rust prevention. Depending on the item you want to prevent from rusting, you should be able to find a wax, oil, finisher or spray that you can use during or after you clean your item as a rust inhibitor. These items, such as rust-prevention oils for golf clubs, are usually sold in hardware stores or specialty stores geared toward your item.
3Repair rust stains as soon as you see them developing on your item. This is especially important in large items, such as automobiles. Whenever you see rust or an area where the paint or steel has bubbled, repair the rust damage before it spreads. If it is a small area, you can scrape rust pieces away with a straightedge blade, warm water and soap. After ridding the item of the rust, apply a metal conditioner or primer before repainting or repairing the area to prevent the rust from forming again. You can make your own rust-inhibitor at home by combining 1/4-cup of anhydrous lanolin with 1 1/4 cups of paint thinner and stirring until blended. Using a paint brush or cloth, apply this cleaning solution directly to areas where you have removed rust. You can also soak small items such as screws or bolts in the solution for several minutes to remove rust.
2003 Ram 3500 Alignment Specifications
The Dodge Ram 3500 came in several two-wheel-drive and four-wheel-drive trims. All two-wheel-drive trims except for those with a 160-inch wheelbase shared the same alignment specs, as did all four-wheel-drive trims -- again, except for those with the 160-inch wheelbase. The rear alignment was not adjustable on any trim of the 2003 Ram 3500.
Caster
The caster angle on the front end of all two-wheel-drive 2003 Ram pickup trucks with a 160-inch wheelbase can range from plus-3.5 degrees to plus-5.0 degrees, with the ideal setting being +4.25 degrees. The caster angle on all other two-wheel-drive trims can range from +3.5 degrees to +4.5 degrees, with a preferred setting of +4.0 degrees and a cross tolerance of +0.4 degrees.
The caster angle on the front end of four-wheel-drive 2003 Ram pickup trucks with a 160-inch wheelbase can range from +4.0 degrees to +5.5 degrees, with the ideal setting being +4.75 degrees. The caster angle on the front end of all other four-wheel-drive trims can range from +3.75 degrees to +5.25 degrees, with a preferred setting of +4.0 degrees and a cross tolerance of +0.4 degrees.
Camber
The camber angle on all two-wheel-drive trims should fall between -0.5 degrees and +0.5 degrees, with zero being the ideal setting with a cross tolerance of +0.6 degrees.
The camber angle on all four-wheel-drive trims should fall between -0.25 degrees and +0.75 degrees, with +0.25 being the ideal setting with a cross tolerance of +0.5 degrees.
Toe-in
The toe-in on all two-wheel-drive trims can range from +0.1 degrees to +0.3 degrees. But +0.1 degrees is the ideal setting.
Thursday, November 28, 2013
Why Are Thermostats Necessary in Vehicles

Automotive cooling systems are complex beasts, not so much in form as in function. The cooling system is more than just a water hose to keep the engine cool, its a support system used to keep all of that hot, fast-moving metal working the way it should be.
Function and Design
A thermostat sits in the base of the hose that moves coolant from the engine to the radiator, and serves to restrict flow to the radiator when the engine is cold. Most thermostats use a wax-pellet design. Below a given temperature, the wax pellet remains a solid, keeping the thermostat valve shut and causing the coolant to recirculate inside of the engine instead of going to the radiator. Above its set temperature, the wax pellet melts and allows the valve to open.
Purpose
You dont technically "need" a thermostat; the engine will continue to run without it. A thermostats primary job is to get the engine up to temperature as quickly as possible and then limit flow to keep it at that temperature. Running without a thermostat will allow coolant to constantly circulate through the radiator, which can cause the engine to run far cooler than it should. While this might seem like a good thing at first glance, bear in mind that most engines are engineered to run best when theyre fairly hot.
How to Install a Horn Button on a Steering Column

Horn pads and horn buttons are commonly used while driving. To sound the cars horn, a driver must press the pad or button. Typically, the button is located on the face of the steering wheel, for easy access. The pad or button itself is wired directly to the horn, which is located in the front of the vehicle. While the horn system is relatively simplistic, it is not standard throughout all vehicles. The removal and installation process slightly differs, and more precise instructions can be found in a Haynes or Chilton manual for your model, make and year.
Instructions
- 1
Open your vehicles hood and locate the battery. Remove the negative cable from the negative terminal. Then, remove the positive cable from the positive terminal. Wait five minutes or more and allow power remaining inside your vehicle to drain out. This is a security precaution. You do not want your airbags accidentally deploying. It may not be necessary depending on your exact make and model, but it is always a good precaution when working on or near a vehicles dashboard.
2Climb into the drivers seat and look at your vehicles steering wheel and horn button. Examine the button very closely. Some horn pads can easily pried off, but you have to make sure the pad does not interlock with any components or paneling on the front of the steering wheel. Insert a tape wrapped screwdriver at the edge of the pad. Slowly pry the pad out of the steering wheels retaining clips. Exercise caution while doing this, as there is wiring connected to the back of the pad.
3Examine the horn button again, if it appears to interlock with other panels and buttons on the steering wheel. Dismantle and remove the panels to get to the button. In some models, like Ford pick-ups, you will have to start at the base of the column and remove other components like the airbag module. Once the obstructions are clear, the button can be easily lifted away from the steering wheel.
4Undo the wiring from the back of the button or pad. There will be a simple wiring connector. You should not have to worry about clipping and crimping any wires.
5Set the old button aside. Connect your vehicles wiring to the back of the new pad or button. Reassemble the steering wheel panels in the reverse of how you took them apart. If you steering wheel features a simple horn pad, connect the pad to the steering wheels retaining clips.
How to Decode 327 Chevrolet Engine Numbers

General Motors assigns a casting number to each Chevrolet engine. In 1962, the company began manufacturing the 327 cubic inch displacement, or CID, small block engine. These casting numbers contain seven digits and provide vehicle specific information, such as engine horsepower. Finding out what the casting numbers mean can save you a lot of time, especially if you need to have your engine repaired or replaced.
Instructions
- 1
View the Quick Stop Speed Shop manual (see Resources). The manual includes information on Chevrolet engine casting numbers. Locate the "CID" column and scroll down to find "327." The other columns provide information such as the model year, casting number, type of vehicle and special notes.
2Go to the Chevy-Camaro website (see Resources). This website provides engine casting number information for Chevrolet vehicles. Select "327" from the "Select Block Casting Group" drop-down menu. The results include casting numbers, horsepower and notes specifying relevant vehicle types.
3Review the Chevelle manual (see Resources). This manual provides casting numbers and related information for various Chevrolet engines. The first section includes details for small block engines. Scroll down the page or use the PDF "Search" to locate "327" and relevant information, such as horsepower and vehicle type.
1997 Dodge Caravan Belt Tensioner Removal

Removing the belt tensioner on a Dodge Caravan may become necessary if the spring or other components inside the tensioner are worn or failing. The tensioner is not serviceable; replacing a defective unit is the only option. The tensioner keeps the serpentine belt tight. If the tensioner fails, the belt may come off the pulleys, damaging the belt, pulleys or accessories. Replacement tensioners are readily available from the Dodge dealer or larger auto parts stores.
Instructions
- 1
Open the hood, and locate the negative battery cable. Follow it to the end, where it meets the battery. Remove the retaining bolt with a wrench, and remove the bolt and cable from the battery. Set it aside.
2Locate the tensioner on the passengers side of the engine, and place a socket on the bolt in the center of the tensioner pulley. Insert a breaker bar into the socket, and rotate the tensioner counterclockwise, loosening the belt.
3Remove the belt from the tensioner, and lay it aside. Rotate the tensioner back to the home position. Remove the breaker bar and socket from the axis bolt. Locate the bolt at the end of the tensioner arm.
4Place a socket and ratchet on the tensioner retaining bolt, and turn it counterclockwise, loosening the bolt. Remove the bolt and tensioner as a unit, pulling them up and out of the engine compartment.
Wednesday, November 27, 2013
How to Dispose of Oil in Palo Alto California

Recycling in Palo Alto is an easy process, since the city provides several public recycling centers open seven days a week, except for national holidays. Auto parts stores also accept used oil, which can be recycled, cleaned and used again. According to Earth 911, 74 percent of used motor oil finds its way to manufacturing plants, incinerators or power plants to create products or energy, while 14 percent is cleaned and combined with new oil for lubricating motor vehicles.
Instructions
- 1
Collect the oil you use for cooking in a container instead of sending it down the drain, straining any bits of food out. Grease and oil can plug up city sewer pipes and make treating effluent more difficult. If you change your own vehicles oil, save it in a watertight container. Do not use foiled containers like shortening cans since they can leak.
2Limit the amount of oil to 15 gallons or 125 pounds or less per trip to the recycler. You can make as many trips to the Palo Alto Recycling Center a day as you wish, but the state of California restricts the amount of hazardous waste people can transport without a special permit. The recycling center will turn you away if you bring too much oil without the hazardous waste hauler permit.
3Take the used motor oil to the city of Palo Altos recycling center located at 2380 Embarcadero Road between 8 a.m. and 5 p.m. The city also accepts oil filters. Bring your drivers license along or vehicle registration. The city only takes oil from residents.
4Bring the used oil to an auto parts store if the recycling center is not convenient for you to reach. These stores typically accept used batteries, motor oil and filters. The retailers use recycling companies to haul the products away for reuse.
1993 Geo Metro Timing Belt Installation
The Suzuki Cultus is a supermini manufactured by Suzuki since 1983. It is marketed under a variety of names, including the Geo Metro in the United States. The 1993 model belongs to the second-generation of this vehicle, and the United States version features a three-cylinder 1.0-liter engine with a single overhead camshaft. This engine design uses a timing belt to keep the camshaft synchronized with the crankshaft. You will need to replace the timing belt in a 1993 Geo Metro at 60,000 mile intervals.
Instructions
- 1
Remove the cable from the negative battery terminal with a socket wrench to ensure the engine doesnt start. Raise the vehicle with a jack and support it on jack stands. Disconnect the bolts for the crankshaft pulley and remove the crankshaft pulley.
2Disconnect the cover for the timing belt with a socket wrench. Turn the crankshaft clockwise to align the timing marks on the camshaft and crankshaft gears. Disconnect the plate, spring and spring damper for the timing belt tensioner. Remove the timing belt tensioner and the timing belt.
3Place the bolt for the timing belt tensioner plate into the hole on the timing belt tensioner. Install the timing belt tensioner, and connect the spring and spring damper. Tighten the bolt on the timing belt tensioner by hand.
4Turn the crankshaft clockwise if necessary to realign the timing marks on the crankshaft and camshaft gears. Install the new timing belt onto the crankshaft and camshaft gears so that the arrow on the timing belt points in the clockwise direction.
5Turn the crankshaft clockwise by two complete turns to remove the slack on the timing belt. Ensure that you align the timing marks on the crankshaft and camshaft gears. Tighten the stud on the timing belt tensioner to 8 foot-pounds with a torque wrench. Tighten the bolt on the timing belt tensioner to 20 foot-pounds.
6Replace the timing belt cover and tighten its bolts to 8 foot-pounds with a torque wrench. Place the key way of the crankshaft pulley into the key on the timing belt pulley and install the crankshaft pulley. Tighten the bolts on the crankshaft pulley to 8 foot-pounds. Lower the vehicle and connect the cable for the negative battery terminal with a socket wrench.
How to Remove the Catalytic Converter on a 1998 Subaru Outback
The 1998 Subaru Outback uses two catalytic converters in the exhaust system, one in the front and one in the rear. Theyre attached, so removing them can be done as one unit or by separating them. Both catalytic converters also have oxygen sensors in them; be sure to disconnect the electrical connectors for them or remove the oxygen sensors from the converter entirely before removing the converter from the car.
Instructions
- 1
Raise the front of the car with a jack. Support the car with a set of jack stands, positioning them under the frame rails.
2Locate the catalytic converters at the front of the exhaust system. There are three heat shields surrounding the converters; removing the nuts and bolts that secure them to the exhaust is necessary. Use a socket and ratchet to remove the hardware, then remove all three of the heat shields from the car. Set them aside.
3Locate the oxygen sensor in the front catalytic converter. Disconnect the electrical connector from the wiring harness by pressing the locking tab in on the plug, then separate the two connectors. Move to the rear converter and disconnect the electrical harness the same way.
4Move back to the front catalytic converter and find the two mounting bolts in the front mounting flange. Remove the bolts with a socket and ratchet. Now move to the rear converter and remove the two mounting bolts in the rear flange. Lower the assembly down and remove it from under the car.
5Remove the mounting bolts in the flange that connect the front and rear converters together, then separate the two converters. You can separate them under the car and remove one at a time; but it is easier to pull both as a unit, replace the one you need to replace, and reinstall them as an assembly.
How to Pull Computer Codes for a Toyota Previa

You can pull the computer codes from your Toyota Previa right from your home garage, saving yourself time and money. To read the codes you will need to buy an OBD code scanner. These handheld computerized devices are available at most auto parts stores. The scanner reads computer codes which are stored in the vehicles On-Board Diagnostics (OBD) computer. Each code tells you information about the Toyota to help you troubleshoot the problems.
Instructions
- 1
Find a port on the drivers side of the vehicle near the steering column. This port looks the same as the connective end on the OBD code scanner. Plug the OBD code scanner into the port.
2Put the key into the ignition and turn it to the "II" position, taking care not to start the engine. This should power on your scanner. If not, find an "on/off" switch on the scanner and press it on.
3Select the "Retrieve Codes" command on the scanner. Wait for the scanner to show you the trouble codes and write them down on a piece of paper. Look up these alphanumeric codes in the scanners manual.
4Unplug the OBD code scanner from the port. Take the Previa to be serviced or repaired based on the trouble codes you retrieved.
Tuesday, November 26, 2013
How to Fix a Hole in an Engine Oil Pan
Driving your vehicle exposes it to risks, no matter what preventive efforts you take. The undercarriage of your vehicle suffers impacts from rocks and road debris kicked up by your tires. The majority of those impacts go unnoticed, but some damage might occur. A sharp rock at the right angle will puncture a hole in your oil pan. A damaged oil pan must be replaced to avoid further damage to your vehicle, but that might not be an immediate option. Repairing a hole in an oil pan should only be a temporary solution.
Instructions
- 1
Position the oil bucket beneath the drain plug, and remove the plug. Drain any remaining engine oil. Remove the oil pan if possible by removing the bolts surrounding the pan and lowering it down.
2Spray engine degreaser over the area surrounding the hole, and scrub it clean with shop rags. Spray it clean with water to remove any remaining oil.
3Sand the area around the hole and as much into the hole as you can using 40-grit sandpaper. Rough up the surface so the bonding agent will adhere.
4Cut a small portion of epoxy putty adhesive. Use a sufficient amount to cover the hole thoroughly. Knead the material until the color is a dull gray, and roll it out into a tube-like shape. The width of the tube shape should be just larger than the hole.
5Push the material into the hole as if you were feeding thread into the eye of a needle. You will have to force it in, as the size of the tube should be a little bigger than the hole. Use your thumb to push down the edges of the material around the hole so there are no gaps and only a small bump remains where the hole was.
6Allow the material to dry in accordance with the packaging. The dry time is usually 24 hours for the material to be able to handle pressure.
7Replace the drain pan if it was removed. Replace the oil pan gasket, and install the pan and gasket onto the vehicle, tightening the bolts in accordance with factory recommendations.
8Replace the drain plug, and torque it to factory specifications. Fill the vehicle with the proper levels of oil, and start the vehicle. Allow the vehicle to run for approximately 15 minutes while the engine warms up. Monitor the patched area for leaks. Locate any leaks and repair in a similar manner.
Explanation of Floating Flywheels

A floating flywheel, also known as a dual mass flywheel or DMFW, is a double weight that sits on your cars crankshaft, next to the pistons. It prevents the force of the pistons from jarring the engine and damaging it. It is mostly found in diesel engines.
Function
When you drive your car, the movement of the pistons produces a force that can cause the engine and the crankshaft to vibrate. This force is called torque. The flywheel reduces torque by weighing down the crankshaft, preventing vibration. The floating flywheel, unlike the standard flywheel, also contains springs that further defuse torque.
Benefits
Vibration of a cars engine and crankshaft can cause damage to the transmission. Specifically, it can damage the gears in the transmission. By preventing vibration, the floating flywheel protects the transmission and its gears.
Types
Aside from the floating flywheel, used in diesel engines, there is also a standard flywheel. The standard flywheel is simply one weight placed on the crankshaft. The floating flywheel is two weights, joined by interlocking springs. However, only diesel engines require that level of protection.
How to Use the Ammco 1030 Tire Balancer

Today there are many types of computer spin balancers to choose from, from complicated to simple. But the most important factor in balancer operation is the person using the machine. If you dont know the proper technique for a computer spin balancer, you could end up making a balance worse instead of better. The Ammco 1030 balancer was designed in 1986 and is still a good choice if you find one used in the marketplace. The major difference between the Ammco 1030 and other models of its time is that the tire is mounted on the machine in a horizontal fashion.
Instructions
- 1
Lift the hood of the tire balancer into the upright position.
2Lift the tire up onto the shaft of the machine and secure with a center cone and the large wing nut. There are several center cones designed to fit securely into the center of the rim located on the right side of the machine.
3Study the workings and functions of the balancer. You will notice that the balancer had three major measurements to input into the machine. You will need to input the diameter, distance and width of the tire. You will see that the measurements are easy to identify. Diameter is the rim size. You can locate this measurement by looking at the tire size on the sidewall of the tire. It is the last number on the tire size, i.e. 14, 15, 16, 17, 18, 19 inch, and so forth. Turn the diameter dial to this number.
4Adjust the distance measurement by pulling the distance meter from the machine and entering the number on the distance dial. This is considered the backside distance from the rear of the tire to the front of the machine.
5Input the tire width measurement with the width measuring tool. This tool will be hanging on the right side of the balancer and it looks like a big plastic "C" clamp with numbers on it. You measure with this tool by placing the ends of it on the bead areas of the rim on each side. Input this number by adjusting the dial for the width measurement.
6Lower the hood of the balancer and press the start button. The start button is clearly labeled to the left of the measurement buttons. The tire will stop spinning once the machine has calculated the amount of weight needed to balance the tire. There is a stop button that you can use if you need to stop the balancer from spinning the tire in case of an emergency or any other reason. The amount of weight needed to balance the tire will be displayed to the left of the start button.
7Locate the correct wheel weight that the machine had calculated and install the weight by hammering it onto the wheel. The location for installing the weight will be marked on the front of the machine. When the tire is turned to the correct spot for weight installation the machine will buzz and you will see all the bars of light illuminated below the calculated weight.
8Lower the hood and press start. When the calculation reads zero, the tire is balanced.
How to Start an Engine After a Rebuild

During the engine-rebuilding process, its paramount to use lots of assembly lube on things such as the camshaft and lifters. However, one place you dont want oil is between the machined surfaces of the connecting rod and cap. Oil there causes erroneous torque readings of the rod bolt. When the trapped oil burns away, connecting rod bolts loosen up and cause catastrophic failure. Lubrication is still the most crucial issue when starting an engine after rebuilding it. Lubricate the engine by priming it before starting. Also be sure the engine is ready to run for 30 minutes.
Instructions
- 1
Connect a mechanical oil pressure gauge to the engine, even if its just used in a temporary situation. The mechanical oil pressure gauge can be connected to the tapped threaded hole where the engines electronic sending unit is installed. The mechanical gauge is much more accurate than an electronic sending unit for an electronic gauge or an oil light and should be used when starting a rebuilt engine.
2Unplug the distributor located on the top side of a V-8 engine or on the side of an inline engine, so the engine will not start while rotating the crankshaft. Loosen but dont remove the number one spark plug from the cylinder.The number one spark plug varies with different manufacturers; consult the engine service manual for the specific engine to locate the number one spark plug. Find the 0-degree line marked on the crankshaft balancer. The balancer is connected to the front of the crankshaft and is behind the engines bottom pulleys. Bump the starter in short bursts by just cranking the engine for a split second. Listen for compression noises near the number one spark plug. After hearing compression leak from the loose spark plug, align the 0-degree line on the crankshaft balancer with the timing tab on the timing chain cover by bumping or rotating the engine in the same direction as the starter turns it.
3Remove the distributor cap from the distributor. Make a mark on the distributor housing that aligns with the rotor cap pointer. The pointer should be pointed at the number one spark plug tower in the cap. If not, be sure the engine did not pass the compression stroke and the distributor was installed correctly. Make another mark on the distributor base flange housing and a corresponding one on the intake manifold.
4Loosen and slide the distributor hold-down clamp back. Lift the distributor out of the intake. Shine a flashlight down into the distributor hole. Notice the flat groove in the oil pump shaft. A Chevy engine was used as example here; check your specific engine for oil priming instructions.
5Remove the valve covers from the engine. Pour a half quart of oil over the lifters just prior to starting the engine.
6Insert an oil pump priming rod into a 1/2-inch drill motor. Slide the flat blade of the priming tool into the pump rod groove, which is located inside the distributor hole. Rotate the drill motor in a clockwise rotation, start the drill and prime the oil pump. Monitor the oil pressure gauge to be sure that oil pressure is building and reaches at least 30 psi. Prime the engine for 10 minutes. Note if oil also reaches the rocker arms on all cylinders.
7Reinstall the distributor by aligning the rotor button pointer with the corresponding mark on the housing and realign the other mark on the housing with the intake manifold. With the timing marks aligned, the rotor should be aimed at the number one spark plug tower in the distributor cap on the compression stroke. Tighten the number one spark plug. Reconnect the distributor plug. Reinstall the valve covers.
8Turn the key on for 20 seconds and then off for 20 seconds. This cycles the fuel pump to send fuel to the engine so there will be sufficient fuel to start the engine without excess cranking. Excess cranking on a newly rebuilt engine can cause damage to the engine. Cycle the key several times to allow fuel into the fuel injection system; then start the engine. If the engine is equipped with a mechanical fuel pump, spray a small burst of starting fluid into the carburetor so the engine does not crank needlessly to pump fuel into the carburetor. Starting fluid will help avoid unnecessary engine cranking.
Monday, November 25, 2013
1990 Chevy Van Wiper Motor Location
You rely on the windshield wipers of your 1990 Chevrolet van to keep your field of vision clear when you are on the road in poor weather conditions. If the wipers fail and you confirm that the relay is intact, the wiper motor might be to blame. Buy a replacement wiper motor from an auto parts retailer, and change it at home.
Instructions
- 1
Park the van, and engage the parking brake. Raise the hood, then rest it on the support rod.
2Use a Phillips screwdriver to remove the screws from the cowl mounted just under the wiper arms, inside the engine compartment. Lift the wiper arms up away from the windshield glass. Push the retaining clip at the base of the wiper arm, and lift it off the mounting post.
3Remove the cowl from the engine compartment. The wiper motor is just below the cowl mounting area, beside the heater duct.
Cam Sprocket Multi lock Tools

Cam sprocket multi-lock tools hold the cam timing in place while the engine is being overhauled or the timing belt is changed. Most multi-lock tools are a simple design but made to exact specifications to grip the cam and lock into sprocket teeth. The cam is a rotating piece of a machine, a shaft or wheel, designed to strike a lever.
Gates 91009 Multi-Lock Tool
A multi-lock tool locks twin camshafts in place, while the timing belt is replaced or the engine is being repaired, to prevent piston-to-valve or valve-to-valve contact. The 91009 multi-lock tool is manufactured by Gates Corporation and is available from many nationwide auto parts retailers.
Gates 91008 Cam Gear Sprocket Tool
A cam gear sprocket tool holds the camshaft in position while the timing belt or other gear is removed from the shaft. The tool simplifies engine-timing procedures, especially when re-aligning the cam-timing position. The 91008 sprocket tool is also made by Gates.
Baum Multi-Lock II Tool
The Baum multi-lock II camshaft locking tool locks sprockets into the correct engine timing position while a timing belt is being replaced or the tension adjusted. This tool is especially handy for keeping cam timing set on four-cam vehicles while changing belts. A pitch adjustment feature accommodates varying tooth pitches and sprocket diameters. The design provides maximum horizontal and lateral off-set adjustment. A ratchet lock handle provides powerful lever action in small spaces. This tool is available online or from specialty automotive parts retailers.
AST 4500 Multi-lock II Tool
The AST 4500 multi-lock II camshaft locking tool is an adjustable tool that locks the cam sprockets in place, preserving their timing during a timing belt change or engine overhaul. The tool can accommodate a variety of sprocket diameters and tooth pitches, as well as flanged sprockets. The 4500 multi-lock also locks between cam and diesel injection pump sprockets on certain diesel engines. Assenmacher Specialty Tools (AST) is based in Colorado, and its catalog is available online.
Mini Cooper Windows Wont Close

Problems with the windows on Mini Coopers are not uncommon. Several issues have been reported with the motors on the window burning out and leaving the window stranded in whatever position it was last in. There are a number of solutions to the problem which you can try yourself before taking the car to the dealer which may be useful, particularly if it is not under warranty. You can recognize a problem when the window stops dipping when you open the door.
Instructions
Reset the Window Position Sensor
- 1
Put in the key and turn the ignition on but leave the engine off.
2Hold the window button in the up position for 10 or more seconds.
3Open the door to make sure the window closes correctly and test the window for normal operations. Dipping of the window is the small drop down when you open the door and the small jump up when you close it again. If the window still does not work then move on to check the fuse.
Check the Fuse
- 4
Open the fuse box. You can find it using the Minis owners manual.
5Remove the fuse for the windows.
6Check the fuse and replace if needed.
7Test the windows for proper operation. If they are still not working then check the motor connection.
Check the Window Motor Connection
- 8
Turn the engine off and remove the key.
9Close the door while sitting in the drivers seat.
10Tap on the door firmly with a closed fist just above the speaker.
11Test the windows for proper operation. If this does not work then take the Mini to a repair shop to have the motor replaced or replace the motor yourself.
How to Remove Pits From Aluminum Auto Trim
Aluminum trim on cars can endure for a long time, giving your car a shiny and smooth line of metal. However, aluminum trim can oxidize and develop pits over time, and its important that you repair these pits as soon as possible to prevent them from spreading. All that you need is some sandpaper and a good polisher, and you should be ready to go.
Instructions
- 1
Remove the aluminum trim from your car. Make sure that youre careful with it and that you set it down in an area thats open and clear.
2Sand off the anodized coating on the aluminum trim. Not all trim will have this coating, and if it doesnt then you can proceed directly to the next step.
3Polish the aluminum trim. Apply the aluminum polish to the aluminum trim in a thin layer. If the pits are deeper, then you should polish them out with an automatic grinder. If the pits arent as deep, then you can polish them out by hand using a smooth cloth. Rub in smooth strokes pushing down hard enough to keep pressure but not hard enough to bend the trim. Continue polishing until youve rubbed out the pits.
4Apply a new coating of sealant over the aluminum trim. This is optional, but it will help protect the aluminum from the elements.
Sunday, November 24, 2013
How to Get Air Out of a Hydraulic System

Air causes the pressure in a hydraulic system to drop. This causes a variety of problems, depending on the type of hydraulic system. When air enters a vehicle brake system, you will need to apply more pressure to the brake pedal to stop the vehicle. In contrast, a hydraulic jack will not lift any weight when air displaces fluid in the hydraulic cylinder. Bleeding the system removes air from the system and allows the system to function properly.
Instructions
- 1
Fill the fluid reservoir to the full line with hydraulic fluid. Remove the fill screw if you are removing air from a hydraulic jack to add fluid directly to the hydraulic cylinder.
2Pressurize the hydraulic system by extending the hydraulic cylinder. For example, press and hold the brake pedal of a vehicle if removing air from a brake system.
3Open the bleeder valve located near the hydraulic cylinder with an adjustable wrench. Close the bleeder valve when no air flows from the valve. Repeat the procedure three to four times to remove all air from the system.
4Fill the hydraulic system with hydraulic fluid after removing all air from the system. Install the fill screw if you removed it to fill the hydraulic system.
5Test the system to ensure proper operation. Repeat the bleeder process if the system does not function correctly.
Can You Pass Inspection With a Broken Fog Light
In general, if your car needs to pass a state inspection, all parts must be in working order. There are some exceptions to that rule. If you are unsure, check your states inspection code.
Broken Lights
In most states requiring a vehicle inspection, including Maryland, Virginia and Pennsylvania among others, all factory original parts of the car, including fog lights, must be in working order. However, in New York State, a broken fog light will not cause a vehicle to be rejected.
Safety Check
If fog lights are required to be in working order, broken plastic or glass on the fog light will definitely get you a fail, as will improper bulbs. Most inspectors are looking for safety concerns when they check the fog lights. A small crack or sealant issue may cause the glass to cloud, which can change the light, causing a safety issue. Cracks and missing chunks also divert or brighten the light. At the same time, a wrong bulb could create the same effect.
Other Options
If your after-market fog lights are broken, you may remove the lights as they are not required in most jurisdictions. Make sure you do not leave hanging wires or switches.
Installation Instructions for a 1998 Honda Passport Window Switch
The 1998 Honda Passport did not come standard with electric windows, but some models included an optional feature. Models equipped with electric windows have a window switch attached to the door armrest. In time, this switch may fail, as do many electronic parts. When that happens, replace the window switch to restore your ability to raise and lower the windows.
Instructions
- 1
Turn the bolt or nut on the Passports negative battery cable counterclockwise to loosen it. Pull the cable from the battery to disconnect it.
2Open the door. The drivers side door contains the master window switch, but there are also window switches on the other doors. The procedure to replace the switches is the same.
3Cover the tip of a flathead screwdriver with masking tape. Insert the tip under the front edge of the window switch. Pry up to pop the front section of the window switch out of the door armrest. Move around the switchs perimeter, gently prying up to free the switch.
4Pull the switch away from the door armrest. Examine the rear. Youll find an electrical plug attached to the back. Push the plugs tab to unlock it, and then unplug it from the switch. Set the old switch to the side.
5Grab the new window switch. Plug the electrical plug into its rear. Set it into the door armrest mount.
6Push the edges of the switch down firmly to secure it to the door panel armrest. Place the negative battery cable back onto the battery post and tighten its nut or bolt.
How to Repair a GMC Power Mirror

A broken side mirror on a car or truck is among the most common of auto body problems. The plastic or mirror on the power mirror can get smashed or cracked and need repair. Replacing the broken power mirror with a new mirror will improve your visibility as you drive. A replacement power mirror is easy to install. The process shouldnt take more than two hours. Purchase a replacement GMC side mirror at an auto parts store or from a General Motors dealer.
Instructions
- 1
Open the GMC car or truck door. Locate the screws that hold the GMC door panel in place. Unscrew the screws with a screwdriver and remove the door panel. Pop the mirror trim out of place with a flathead screwdriver.
2Unscrew the screws that hold the side mirror in the door. Set the screws aside. Unhook the cable in the mirror from the cable in the door. The cables should easily slide apart at the plastic electric harness that holds the two cables together. Slide the mirror from the door.
3Slide the wire cable of the new side mirror through the hole in the car door. Use a screwdriver and the old screws you set aside to secure the mirror to the door. Connect the cable of the new mirror into the cable in the door at the plastic electric harness. Screw the door panel back into place. Pop the window trim into the door.
Saturday, November 23, 2013
How to Get a New Vin Plate for a Car

The vehicle identification number (VIN) is like a Social Security number for cars. All VINs for cars manufactured since 1981 have 17 digits and they are usually found etched into a metal plate on the engine block, the firewall or the inside of the door frame. If your VIN plate has been destroyed, you can apply to have a new one created for the vehicle as long as you have proof of need for the replacement. If for some reason your VIN on the vehicle and the VIN on your title do not match, you will need to get a new title, not a new VIN.
Instructions
- 1
Locate and record your vehicles VIN. Consult the owners manual for your vehicle if you do not know where it is located. Record the make, model, year, color, and license plate number of your vehicle.
2Locate the vehicles title which lists the VIN of the car. If you are financing the vehicle, the finance company will have the title. Contact the company that issued your car loan to get a copy of the title.
3Contact your local State Department of Motor Vehicles (DMV) office for specific instructions on what is required to replace the VIN (see Resources). You will likely be required to have an inspection of the vehicle by a police officer or DMV official to verify that the VIN plate was destroyed. Take all the recorded information with you when you go to the DMV.
How to Repair a Water Damaged Vehicle
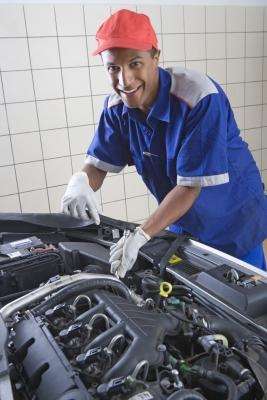
Floods, hurricanes and other disasters can result in cars partially or totally covered with water. In some cases, the price of restoring a drowned car to serviceable condition would eclipse the value of the car, so you or your insurance company should just scrap it. In other cases, it is possible to dry out a flooded vehicle, enabling it to provide many additional miles of safe, comfortable driving. Though drying out the interior upholstery and seats is a challenge, its more important to remove all the water-contaminated fuel, oil and fluids to ensure the systems they control or lubricate operate correctly and safely once the rest of the vehicle is rehabilitated.
Instructions
- 1
Drain the engine oil by removing the drain plug in the oil pan and allowing the oil to run into a drain pan. Change the engine oil filter, then replace the engine oil with fresh oil.
2Drain the engines cooling system by loosening the hose clamp on the lower radiator hose and disconnecting the hose allowing the coolant to drain into bucket. Reconnect the hose then refill with fresh antifreeze/water mixture.
3Drain the transmission oil by removing the bottom pan on the transmission by unbolting the bolts around the perimeter of the pan. Drain the fluid into an oil drain pan. Replace the transmission filter located under the transmission pan, reattach the pan then refill the transmission with the specified amount of transmission fluid.
4Drain the brake fluid from the brakes, master cylinder and brake lines. Use a wrench to open the bleeder valves located on each wheel the pump the brakes until all the fluid is expelled. Add new brake fluid to the master cylinder, then bleed each brake individually to remove all the air from the brake system. Capture as much used and purged brake fluid in plastic containers, then clean up the fluid that dripped onto the tire, wheel supports or floor.
5Remove all the gasoline from the fuel tank either using a siphon hose or by removing the gas tank and dumping out the gasoline into a bucket. Refill the gasoline tank and add gas-line antifreeze to absorb any residual moisture in the system.
6Drain the power-steering reservoir by removing one of the hydraulic hoses, then rotating the steering wheel back and forth until all the fluid is pumped out. Capture the used oil in an oil drain pan. Refill the power steering reservoir with power steering fluid.
How to Replace a Front Motor Mount on a Honda Odyssey

Excessive shaking during acceleration or when driving up hills can point to a broken front motor mount on the Honda Odyssey. The motor mount is located in the center of the engine compartment, between the lower part of the motor and radiator. Examine the mount from under the engine compartment. If the rubber is cracked, replace the motor mount before the vibrations cause any other parts on the Odyssey to fail.
Instructions
- 1
Drive both front wheels of the Odyssey onto ramps. Secure wheel chocks behind both rear wheels. (Alternatively, raise both front wheels with a jack and secure them on jack stands.) Open the hood of the Odyssey.
2Place a jack under the oil pan, with a scrap of wood between the jack and the oil pan. Raise the jack slightly until the wood touches the pan.
3Remove the four bolts below the front motor mount with a socket wrench. Remove the one nut above the front motor mount.
4Raise the jack under the oil pan until the top motor mount bolt is free from the motor. Secure a jack stand or additional wood under the motor as a safety precaution.
5Remove the motor mount by lifting and sliding sideways, up and out. Replace with a new front motor mount.
6Replace the four bolts under the front motor mount and secure to finger tightness. Remove the jack stand from under the motor. Lower the jack slowly, allowing the upper motor mount bolt to slide into the front mount bracket. Remove the jack and wood.
7Replace the upper motor mount bolt and tighten to 40 ft-lbs. (54 N-m). Tighten the four lower bolts to 28 ft-lbs. (38 N-m).
Friday, November 22, 2013
How to Fix a Small Tear in a Leather Truck Bed Cover

Most soft tonneau covers marketed as leather truck bed covers are actually made of vinyl. Even though vinyl is tougher than leather when exposed to the elements, these covers are not indestructible. Without careful maintenance, leather-look vinyl truck bed covers can become dry and prone to cracks and tears. When this happens, you can use a leather and vinyl repair kit to fix the damaged area if its small. While it wont look like new, you can make the problem area less noticeable and stop it from getting bigger.
Instructions
- 1
Clean the area around the tear thoroughly to remove dirt and oil that might prevent the vinyl from bonding properly with the repair material. Use soap and water first, then swab with alcohol.
2Remove any rough edges from the tear with a razor blade, scalpel or scissors. You want the torn edges to lie flat.
3Insert a piece of canvas backing from a vinyl and leather repair kit under the tear with tweezers. Some kits require you to apply glue between the vinyl and the canvas and press them together to seal them; with others, you apply heat with an iron or a special tool.
4Mix the pigments provided in the leather and vinyl touch-up kit to match the color of the truck bed cover as closely as possible. Mix the pigment with filler material from the repair kit.
5Fill the tear with filler material. Apply it in several thin layers rather than one thick layer. Press the embossing stamp which most closely resembles the grain of the bed cover to the final layer of filler material.
Installation Instructions for an Eagle Talon Water Pump
The Eagle Talon is a compact sport car also marketed as the Mitsubishi Eclipse and the Plymouth Laser. Chrysler and Mitsubishi manufactured the Talon in a joint venture from 1989 to 1999; the latest version included the 1995 through 1999 model years. A late model Eagle Talon has a four-cylinder 2.0-liter engine with the water pump on the front of the engine. The installation of the water pump in this vehicle also requires you to drain the radiator.
Instructions
- 1
Remove the cable on the negative battery terminal to prevent starting the engine during the procedure. Place the drain pan under the radiator drain, and remove the drain plug. Allow the coolant to drain into the container and store it for later use. Replace the drain plug.
2Disconnect the pivot bolt for the alternator brace with a socket wrench and remove the alternator brace from the water pump. Remove the retaining bolts for the rear cover of the timing belt and detach the rear cover from the engine. Disconnect the timing belt.
3Remove the mounting bolts for the water pump with a socket wrench. Detach the water pump from the engine. Discard the gaskets and O-rings for the water pump.
4Coat a new O-ring with water; mount it onto the water inlet pipe. Place a new gasket on the new water pump; install it to the engine block. Torque the mounting bolts for the water pump to between 8.7 and 11 foot-pounds with a torque wrench.
5Install the timing belt and the rear cover for the timing belt with a socket wrench. Connect the alternator brace and tighten the pivot bolt for the alternator brace to 17 foot-pounds.
6Fill the radiator with coolant. Reconnect the cable to the negative battery terminal. Start the engine and check for coolant leaks.
How to Replace the Fuel Pump in a 3000GT
The Mitsubishi 3000GT is a performance car and is also called the GTO. From 1991 through 1996, the 3000GT and the Dodge Stealth were manufactured identically. The fuel pump in a performance vehicle is directly involved in how well the engine runs. A clogged fuel pump will cause the engine to misfire, gas mileage to rise and performance to drop. Changing the fuel pump as soon as it begins to break down will prevent future problems.
Instructions
- 1
Park the Mitsubishi 3000GT on a flat, level surface, and set the parking brake. Open the hood, and disconnect the negative battery cable.
2Place the jack under the front of the car at the center of the frame. Lift the vehicle, and place jack stands under the front axles.
3Remove the cap to the fuel tank to release pressure on the fuel lines.
4Follow the fuel line coming out of the fuel tank to locate the fuel pump. Unplug the fuel pumps wiring harness. Place a drip pan under the fuel pump. Loosen the hose clamps with a slotted screwdriver, and disconnect the fuel lines. Point the fuel lines at the drip pan when they come loose to catch any spilled fuel, then dab the ends of the lines with a rag to clean up the remaining fuel.
5Remove the mounting bolts with a socket wrench. Remove the fuel pump.
6Attach the new fuel pump, and tighten the mounting bolts with a socket wrench. Attach the fuel lines to the fuel pump and tighten the hose clamps with a slotted screwdriver. Plug in the fuel pumps wiring harness.
7Remove the jack stands, and lower the car. Pump the gas pedal a few times to get fuel into the fuel lines.
How to Install a Radio in Mazda Millenia
Classified as a luxury car, the Mazda Millenia offered a number of radio choices. Some models came equipped with a cassette player, while others had a single- or multiple-disc CD player. If replacing or upgrading your Millenia radio, you will need a special removal tool. The radio is held in place by internal clips rather than screws. This tool can be purchased in most stores that sell car stereos or from a Mazda or Ford dealer. Many Ford and Mercury radios use the same tool.
Instructions
Removal
- 1
Open the hood and use and adjustable wrench to disconnect the negative battery cable.
2Use a small screwdriver to carefully remove the four small rubber hole covers from the sides of the radio.
3Insert the Mazda radio hook tools into the holes along the sides of the radio to release the inner spring clips. Push the tools in firmly until you hear a "click." Maintain pressure on the side tools and carefully pull the radio straight out of the dash.
4Disconnect the antenna and wiring harness from the back of the radio. Push on the springs on the sides of the radio to remove the radio hook tools.
Installation
- 5
Attach the wiring harness to the new radio. If you are replacing the radio with a Mazda factory model, you can reuse the existing wiring harness and antenna connection. If you are installing an aftermarket radio, you may need a Mazda radio installation kit. In that case, follow the instructions with the kit.
6Connect the wiring harness and antenna cable to the back of a new factory radio. Slide the radio into the dash. You should feel the clips engage the radio. Replace the four rubber hole covers.
7Follow the directions supplied with the kit if you are installing an aftermarket radio.
8Reconnect the negative battery cable and test the radio.
9Enter an anti-theft code if you have installed a factory radio. Consult your owners manual for the code, or contact a Mazda dealer
Types of Dents on Cars

No matter who caused the dent in your car or how it happened, fixing the dent is all that matters. Automotive retailers sell do-it-yourself dent repair kits that can repair minor dents, but for major ones, youll do better to hire a dent repair specialist with the knowledge and tools to address the issue properly. Knowing the type of dent can guide you in choosing the right approach for repair.
Car Door Dings
According to Chris Parsons, a dent repair specialist a ding is a small imperfection often made by another car door hitting your cars door. These types of dents tend to appear in the middle of your car door. They are relatively easy to repair as long as no paint damage has occurred, which otherwise requires the aid of a body shop. An auto repair kit purchased from an automotive retail store can usually rid your car of these types of dents, indicates the online automotive website My Honest Mechanic.
Round Dents
Small- and modest-size round dents sometimes result from a hailstone or a round object, such as a baseball or basketball, hitting the car and causing a dimple on the hood or roof. As with dings, dent repair specialists can usually remove round dents fairly easily provided no damage has occurred to the cars paint.
Crease-Type Dents
According to Parsons, crease-type dents are some of the most difficult to remove. These dents usually result from an auto accident. A crease-type dent usually scores and bends the cars metal along its body line. Repairing damaged metal and restoring the cars body to its original contour can be nearly impossible, Parsons explains. Each car has its own metal memory formed at the time of production by heating the metal at high temperatures and shaping it. Cars frequently lose their metal memory when they sustain a crease-type dent.
Thursday, November 21, 2013
How to Change the Headlights in a 1985 Firebird
The 1985 Pontiac Firebird comes equipped with motorized headlights. The headlight assemblies rise to reveal the hidden headlights when the headlight switch is on. When the switch is off, this mechanism keeps the headlights hidden. All Firebirds are equipped with a manual crank to allow access to the headlights when the vehicle is not in operation. This makes accessing the headlights for replacement easy.
Instructions
- 1
Pull the hood latch and lift the hood. Make sure the hood will stay open on its own. If the hydraulic shocks are weak, use a prop rod to keep the hood open during repairs.
2Locate the manual crank beside the headlight assembly. It will be a black cylinder with a rubber knob at the top.
3Turn the knob on the manual crank until the headlight assembly is fully open.
4Remove the perimeter screws from the metal retaining ring that holds the individual headlights securely in the housing.
5Remove the retaining ring and pull the headlight out of the housing. There should be enough slack in the wiring to gain access to the connector at the rear of the headlight.
6Unplug the connector and discard the defective headlight. Plug the connector into the new headlight and place it in the housing.
7Replace the metal retaining ring and install the perimeter screws to secure the headlight to the housing.
8Repeat this process for the remaining headlights. When finished, turn the manual crank in the opposite direction until the headlight assembly has returned to its normal resting position.
What are the Functions of a Speed Sensor

From the speedometer to the cruise control to the transmission, the data collected by speed sensors affects the operation of multiple systems functioning within your car. In fact, many systems rely on these sensors input to operate. Speed sensors measure the speed of the transmission/transaxle output of the wheel, then send a signal carrying this data to your cars operating systems.
VAPS
The variable-assisted power steering (VAPS) system in your vehicle utilizes speed sensors so you can navigate parking lots, school zones and other low-speed areas with ease. The VAPS system controls and adjusts the cars power steering pressures. The speed sensors send data on speeds to the VAPS that allows the system to control and adjust power steering pressures. This regulation of power steering pressures allows the system to help you decelerate easier, which in turns helps you drive in low-speed areas.
ABS
The speed sensors used by the anti-lock brake system (ABS) of your vehicle let the ABS know when a wheel locks up and when to discharge pressure from that wheel so you can continue to steer the car. Depending on the brand of vehicle you own, the ABS may utilize sensor from transmission/transaxle, wheel, or a combination of both sensors.
Speedometer
Unsurprisingly, speed sensors also help your cars speedometer operate. The instrument cluster (IC) and hybrid electric cluster (HEC) modules translate the data from the speed sensor into a reading on your speedometer.
Advanced Air Suspension System
If your vehicle employs an advanced air suspension system, the speed sensors may also help determine how high your car rides. The height of your car affects how your car handles at high speeds. The lower your car sits, the better it will handle when youre driving fast.
Transmission
Speed sensor input data to your transmission as well. The information they gather tells the transmission how to shift as you change speeds.
Cruise Control System
The information from the speed sensors allows the cruise control system of your car to maintain a steady speed, accelerate and decelerate without you having to touch the gas pedal or brake pedal.
EEC
The electronic engine control (EEC) system uses the signals from speed sensors to adjust engine functions due to fluctuations in speed. It also uses input from the sensors to begin diagnostic procedures.
Oil Seal Grease Seal Differences
Seals are used in many applications to prevent liquids from moving from one compartment to another. Even though an oil seal uses oil to accomplish this while a grease seal utilizes grease, both seals may be used in the same machine to protect different parts. Oil is a lubricant that makes an engine turn over and run smoothly, while grease is made from animal fats and minerals, making it a thicker lubricating substance than oil. It is common to confuse the two terms since many companies will refer to an oil seal as a grease seal, and vice versa.
Location
An oil seal is often located where raw oil is inserted into the machine for lubrication. This seal will keep the oil from blending into other liquids inside of the machine, and from coming into contact with water. A grease seal is often found away from any entry point in the machine, but rather at the base of an engine so the grease made by the oil does not leak out.
Material
Grease differs from oil in that it keeps a thick, liquid state while at room temperature. Because of this, grease seals are typically thicker and made from more durable materials like silicone and polytetrafluoroethylene (PTFE) to withstand the heavy flow. An oil seal only needs to fit securely to the machine part, since oil is a runny liquid at room temperature. The oil seal might be thinner and be made from elastics and acrylics.
Apperance
While both seals resemble one another at first glance, upon a closer look, the seals do differ slightly. Once again, grease is a thick, heavy sludge, made from the fats of animals and minerals. Because of this, a seal for grease might have a two-lip design, which is a double groove on the outside of the seal, to securely enclose the grease inside the machine part. Some seals have a spring set within the groove, or lip, to guarantee the seal does not slip off. Oil seals, on the other hand, usually just require a single lip design to keep the seal in place.
Wednesday, November 20, 2013
How to Replace Wiper Blades on the Chevy S10

Bad wiper blades not only diminish driving visibility during a storm, but also may cause your car to fail inspection. New wipers are affordable and easy to install. Wipers are widely available from automotive parts stores or discount retailers. The toughest choice is picking a brand of wiper suited to your needs.
Instructions
- 1
Find the right size wiper for your Chevy S10. The wipers should be 20 inches for both driver and passenger sides of the car. However, if you want to be absolutely certain, Rain-X has an online guide to wiper sizes.
2Visit the retailer of your choice to purchase the wipers.
3Lift the wiper blade off the windshield.
4Look for a button or mechanism at the center of the wiper and press it.
5Slide the wiper blade out of the J hook of wipers arm. The blade as a whole unit should slide out.
6Slide the new wiper blade into the J hook, until you hear the button click.
7Tug the wiper blade gently to secure it in the J hook.
8Remove any plastic covering from the wiper blades rubber edge.
9Rest the new wiper blade against the windshield. Begin to reinstall the other new wiper, if necessary.
How to Ground Headlights
A headlight is normally grounded to the chassis of a vehicle in order to allow electricity to complete a circuit and return to the vehicles negative battery terminal. If the headlights ground loosens or disconnects, the headlight will begin to blink, dim or go out completely.
Although vehicle headlights can vary drastically in look they all ground to the vehicle in the same way. Some knowledge of wiring is important to anyone trying to complete this task.
Instructions
- 1
Park the vehicle on a flat surface and set the parking brake. Open the hood and secure it in place with the hood prop. Disconnect the negative battery cable.
2Unplug the wiring harness from the rear of the headlight. Trace the route of each of the wires coming from the wiring harness until the ground is found. The ground is the wire that runs directly to the chassis. If it has broken off of the chassis, it will be hanging free at the far end.
3Start screwing a self-tapping screw into the vehicle chassis. Wrap the end of the ground wire firmly around the screw, then tighten the screw until the head pins the wire to the chassis.
4If the end of the wire is damaged or no wire is showing, clip off an inch of the ground wire with wire cutters. Strip one and a half inches of insulation from the end of the wire and expose enough of the ground to wrap around the screw.
How to Remove the Transmission Cooling Line on a 1996 Dodge Ram 1500

Removing the cooling lines from the transmission in your Dodge truck is an essential step in removing the transmission or transmission cooler. If you have a damaged transmission cooling line, youll need to remove it before you can install a new one. Transmission cooling lines are available from your Dodge dealer as well as from many auto parts stores. If you are working on your Rams transmission fluid cooler or transmission and the lines are in good shape, you can reuse them.
Instructions
- 1
Position a jack under the front of your Ram and raise it off the ground. Place a set of jack stands under the frame to support the truck, then remove the jack.
2Slide an oil drain pan under the transmission cooler, under the front of the Ram. Slide a quick-disconnect tool onto the cooling line and slide it into the fitting, releasing the connector. Pull the line off the transmission cooler.
3Follow the line back to the transmission and locate the fitting on the transmission case. Position another drain pan under this end of the line, then loosen the fitting on the line with a wrench.
4Turn the fitting counterclockwise until it is free from the transmission, then carefully slide the line back and out from under the truck. Repeat the process on the second line if you need to remove it as well.
How to Jack Up a 2000 Ford Taurus

A lonely, moonlit road, in the middle of nowhere is not the place to discover that you do not know the proper jacking procedure for your Taurus. Getting the vehicle safely up, and off the ground is best learned in a calm and safe setting. Learning the proper procedure first, before you actually need it, can go a long way toward ensuring that you can safely raise and lower your Taurus when that unexpected flat tire, or other roadside emergency arrives.
Instructions
- 1
Place the Taurus on level ground. Engage the parking brake and put the transmission in park.
2Locate the wheel which is diagonally opposite the wheel that is being lifted and block it. It can be blocked with a rock if necessary.
3Locate one of the four notched sections of the rocker flange. There is one near each wheel, under the body panel, at the bottom. The top of the jack is designed to fit into this notch.
4Place the jack under the notch and raise it by turning the handle clockwise. Guide the jack face into the notch. Continue turning the jack handle clockwise until the vehicles tire is off the ground. To lower the jack, turn the handle counterclockwise until the vehicles tire is back on the ground and the jack can be removed. When finished, be certain to unblock the opposite wheel.
Tuesday, November 19, 2013
How to Troubleshoot a 2006 PT Cruiser

The Chrysler PT Cruiser is a compact-size vehicle first introduced in 2000. As with any automobile, there are a number of things that can go wrong with a PT Cruiser. A dead battery, bad alternator or loose wires are just a couple of things that can cause issues. You do not have to be a Chrysler mechanic to get your PT Cruiser back on the road. You can fix many of the small problems yourself in a relatively short amount of time.
Instructions
- 1
Listen for a clicking noise when attempting to start the car, which may indicate that the alternator is malfunctioning. Have the car towed to a service shop to get the alternator checked out.
2Open the hood and check the battery connections to make sure they are tight. The battery is located next to the engine with two terminals attached to it.
3Use a pair of insulated pliers or wrench to tighten the connection of the positive and negative terminals on the battery. If the car still wont start, use a battery tester to test the 12-volt battery.
4Attach the red and black leads of the tester to the red and black leads on the battery. If the tester displays significantly less than a 12-volt reading, you can attempt to "jump-start" the vehicle.
5Connect jumper cables to the positive and negative terminals on the battery. Connect the jumper cables to a another vehicle. Start the other car and then start your PT Cruiser. Allow the PT Cruiser to run for a minimum of 15 minutes to charge the battery.
6Turn the engine off and then try to turn it back on. If the car will not start back up, replace the battery with a new 12-volt battery.
7Remove the steering wheel cover if your turn indicator lights are dimming. Turn the key in the ignition, but do not start the engine.
8Move the wiring harness while you turn the wheel until you get the wires to a point that the lights do not dim. Secure the wires in place with a small wire clip or tie. Put the steering wheel cover back in place.
How to Replace an Oxygen Sensor in the 2002 Hyundai Sonata
You might need to replace the oxygen sensors on your 2002 Hyundai Sonata if you notice your fuel consumption increasing, or if your "check engine" light illuminates. The oxygen sensor measures the amount of oxygen being expelled through the exhaust and adjusts the fuel necessary to meet certain oxygen levels. You have two sensors, one in the manifold and one inline with the catalytic converter. Remove both in the same manner.
Instructions
- 1
Locate the oxygen sensor in the exhaust manifold or the exhaust pipe next to the catalytic converter. It resembles a spark plug and has one thin wire extending from it. Use the replacement sensor for a visual aid.
2Push in on the lock on the wire harness at the top of the sensor. Pull the wire off.
3Remove the sensor with a deep well socket or wrench. Due to the extreme heat generated in the manifold and exhaust pipe, it is common for the sensor to become stuck. If necessary, use spray-on rust breaker such as liquid wrench to aid in the removal process.
4Place a small amount of anti-seize compound on the threads of the new oxygen sensor and thread the sensor back into the manifold or tail pipe.
5Push the connector of the wire back onto the oxygen sensor.
Signs That a Catalytic Converter Is Going Bad
A catalytic converter is an exhaust emissions device that is part of a vehicles exhaust system. In charge of lowering the exhaust emissions that exit a vehicles tail pipe, a catalytic converter can negatively impact vehicle performance if it goes bad or stops working properly. What follows is a brief list of the most common signs of a bad catalytic converter.
Reduced Exhaust Flow
A major sign of a plugged up and/or bad catalytic converter is reduced exhaust flow measured at the vehicle tail pipe. Engine exhaust must travel through a catalytic converter before exiting the tail pipe; a bad catalytic converter can block and/or impede exhaust flow.
Reduced Engine Power
If a bad catalytic converter seriously impedes the flow of a vehicles engine exhaust flow, reduced engine horsepower can occur. This is due to the increase in engine exhaust back pressure that results whenever engine exhaust flow is impeded and/or reduced.
Reduced Exhaust Pipe Temperature
It is common for a bad and/or plugged catalytic converter to cause abnormally low exhaust pipe temperatures on the backside of a catalytic converter. As engine exhaust exits an engine and travels down the exhaust system and through the catalytic converter, the exiting exhaust flow can be restricted enough to cause significantly reduced exhaust pipe temperatures between the catalytic converter and the tail pipe.
Increased Hydrocarbon Emissions
Catalytic converters work by reducing the levels of hydrocarbon emissions exiting a vehicles tail pipe. A bad catalytic converter can lose its emissions-lowering capabilities and cause an increase in exhaust hydrocarbon emissions, a condition that is normally picked up when a vehicle is undergoing a routine smog inspection.
Reduced Fuel Economy
Any obstruction and/or abnormality in a vehicles exhaust system has the potential to reduce vehicle gas mileage by creating exhaust back pressure within a vehicles engine. A bad catalytic converter can cause a reduction in vehicle fuel economy if it restricts the flow of engine exhaust to the point of causing a marked increase in engine exhaust back pressure.
Instructions on How to Install a Billet Grill

A billet grill is a grill that has slats in it just wide enough to allow water and air to circulate to and from the cars radiator but narrow enough to prevent rocks and other debris from damaging the radiator itself. Billet grills are usually installed on trucks and cars to give a more customized, unique look. Of course you must remove the old grill before beginning the installation procedure.
Instructions
- 1
Raise up the hood of your car or truck and prop it open with the bar.
2Position your assistant in front of the vehicle holding the new billet grill in place against the front of the vehicle. Push the bolts through the holes and tighten with a socket and ratchet.
3Lower the hood of the car.
Monday, November 18, 2013
How to Remove a Bolt on a Battery Cable
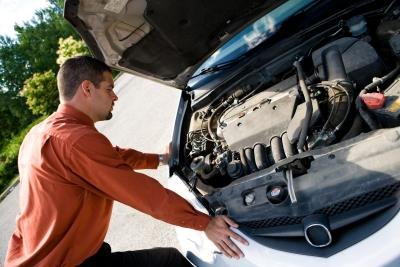
Automotive batteries come with either top mount or side mount terminal applications. Top mount batteries require battery cables with clamps that secure over the battery posts. Side mount batteries require cables that have a bolt that threads into the battery. Battery cable bolts can corrode and crack requiring replacement of the bolt. The bolt fits into a groove or channel inside the end of the battery cable. Removing the bolt on a battery cable requires basic brute force and some manipulating of the cable.
Instructions
- 1
Disconnect the negative battery cable from the battery with a wrench. The negative cable is the black cable and the terminal hole has a - stamp near it. Disconnect the positive battery cable from the battery in the same manner.
2Grasp the sides of the battery cable where it surrounds the terminal bolt. Bend one of the sides down with your thumb and push the thread end of the bolt to walk the bolt out of the cable end. If necessary, use a pair of pliers to hold one side while you bend the other with your fingers. The hard rubber cable end does bend, but it requires some effort.
3Hold the battery cable end with your fingers. Insert the threaded end of the new bolt into the battery cable at an angle to insert one of the sides of the bolt ring into the groove in the cable end
4Twist the bolt with your fingers to thread the ring all the way into the groove, much like you would insert a bicycle rim into a tire. Bend and manipulate the end of the cable as necessary until the ring of the bolt is within the groove and the bolt spins freely with your fingers.
5Connect the battery cables back into the battery starting with the positive cable first. Tighten the battery bolts to the battery with a wrench.
What Are the Causes of a Burnt Motorcycle Clutch

The clutch on a motorcycle is what the rider uses to change gears as he rides. Clutches can burn out, which basically means that they wear out and no longer work the way that they should. The clutch works by causing friction between two metal plates that have grooves. When these grooves get worn down, it causes the clutch not to work as well.
Defective Clutch
If the motorcycle clutch is defective in any way, it will not work properly. A defective clutch will cause the motorcycle to either simply stop working or to burn out due to improper wear. If this is the case, you will generally notice it within the first ride or first few rides.
Regular Wear and Tear
A rider can do everything properly with motorcycle and clutch maintenance, but most things wear out or wear down eventually, and so too will the motorcycle clutch. Ensuring your clutch is adjusted correctly and lubricated is important, but the clutch will still wear out, depending on the use of the motorcycle. The general time frame to check or change the clutch is about 50,000 miles.
Driver Error
If a rider "rides" the clutch, she will wear it out faster than normal. Riding the clutch means that the rider keeps the clutch pushed in a little on a constant basis, which will weaken the clutch, the springs and other parts on the clutch. The clutch on a motorcycle is on the handlebars of the bike as opposed to a car, which has the clutch next to the brake pedal on the floor. A motorcycle rider who keeps his fingers pushing on the clutch lever is riding the clutch.
Steep or Rough Terrain
If the primary area that the motorcycle is used in is hilly or rough and causes a lot of starting and stopping, it will cause the clutch to burn out faster. Shifting up and down, depending on ascending or descending landscape, makes the clutch work harder and more often.
How to Remove Spark Plug Wires From a 2003 B2300
The 2003 Mazda B2300 was produced at the Twin Cities Assembly Plant, in St. Paul, Minnesota, side by side with the Ford Ranger. The 2003 B2300 came equipped with a 2.3-liter, in-line four-cylinder engine. The ignition system on the 2003 B2300 is a coil ignition type, meaning that all of the spark plugs are controlled by a coil module that meters the spark through each wire to the plugs. The spark plug wires are usually removed when changing the plugs, or in order to replace damaged wires with new ones.
Instructions
- 1
Open the hood of the B2300 and set the hood prop. Remove the negative battery cable from the battery, using a 3/8-inch drive ratchet and socket.
2Locate the ignition coil -- the box into which all four spark plug wires are routed from the engine. Follow each plug wire from the coil to the engine by running your hand along each wire; as you do so, remove any wire clips from the wires, using a small flat-head screwdriver. These clips are important for keeping the wires in place, so that they do not short out on anything in the engine compartment.
3Twist the rubber boot at the engine end of one of the wires, while pulling it up off the spark plug. Trace the wire with your hand back to the ignition coil, and remove only one wire from the ignition coil. Pay close attention to the direction the wire is routed in the engine compartment, as it will have to go back the exact same way.
4Spread the new wires out over the front of the radiator so that you can see the length of each wire. Match the length of the wire you have removed from the B2300 with one of the new wires.
5Install the new spark plug wire onto the ignition coil. Route the wire through the engine compartment to the engine. Insert the wire and twist it, while pushing the wire downward onto the engine.
6Repeat Steps 2 through 5 to complete the wire replacement on the entire engine. Secure all of the spark plug wires with the clips that were previously removed, snapping the clips closed, by hand. Double-check that each wire is securely pushed onto each spark plug, and onto the ignition coil.
7Install the battery cable back onto the battery and tighten the tie-down nut snug with a ratchet and socket.
Information on a GM TH200 4R Transmission
The Turbo-Hydramatic 200 4-R was an automatic transmission with overdrive that was manufactured by General Motors. The TH200 4-R was produced and used in a variety of GM vehicles made between 1981 and 1990.
Identification
The identification tag on the TH200 4-R provides information about the transmissions production history. The first through third digits give the month and date of production. The fourth digit names the shift it was produced on. This is followed by a letter indicating the plant the transmission was made at. The TH200 4-R was manufactured at the Three Rivers and Warren, Michigan GM plants and in Windsor, Canada.
Specifications
The TH200 R-4 had a first gear ratio of 2.74-to-1 and a second gear ratio of 1.57-to-1. The third gear ratio was 1.00-to-1. The fourth gear was the overdrive with a .67-to-1 gear ratio.
Swapping TH200 4-R
The TH 200 4-R is a popular transmission to use to upgrade from an older transmission that is lacking an overdrive gear. The TH200 4-R is used by car enthusiasts to replace the earlier Powerglide and the TH350 model transmissions.
Sunday, November 17, 2013
How to Replace a 2000 Ford Focus Thermostat

The thermostat in the 2000 Ford Focus works by opening a jiggle valve as the temperature of the radiator fluid rises. As the valve opens, the thermostat allows more fluid to flow through the radiator, thus cooling the fluid and the engine temperature down. Over time, engine buildup in the coolant system causes the thermostat to corrode. This corrosion causes the thermostat to fail. When this happens, the valve stays in the open position and reduces the engine temperature, thus reducing the amount of heat the Focus produces inside of the car. This means you must replace the thermostat in your 2000 Ford Focus.
Instructions
- 1
Open the radiator drain plug by inserting a -inch ratchet drive into the drain plug, then drain 2 gallons of radiator fluid into a drain pan. The plug loosens by turning the ratchet counterclockwise. Close the drain plug once you drain the fluid. This drops the fluid in the radiator below the height of the thermostat. This prevents fluid from draining from the radiator hose as you replace the fluid.
2Locate the area on the top of the engine where the upper radiator hose connects. The hose connects to the thermostat housing. Remove the hose by loosening the band clamp with a screwdriver, then pull the hose off the thermostat cover.
3Remove the two bolts that secure the thermostat housing to the Ford Focus with a 9/16-inch socket. Lift up on the housing to remove it from the engine.
4Pull the old thermostat out of the intake manifold and then place the new one into the intake. The design of the thermostat allows it to fit into the intake in one manner.
5Lift the old gasket off of the intake manifold and wipe the surface clean with a shop towel. Place the new thermostat gasket onto the intake.
6Wipe the bottom of the thermostat housing clean with a shop towel and place it on top of the gasket. Tighten the thermostat housing in place with the old bolts.
7Slide the hose onto the thermostat housing and secure it by tightening the band clamp with a screwdriver.
8Open the radiator cap on the top of the radiator and drain the 2 gallons of fluid back into the Focus. Close the cap once you are finished.